Programmable Logic Controllers (PLCs) are essential components in modern industrial automation systems. PLCs are designed to control and manage various industrial processes, from simple machines to complex production lines. A PLC consists of several key components, each of which plays a critical role in ensuring the proper functioning of the system.
What is PLC?
A Programmable Logic Controller, or PLC, is an electronic device that is designed to control and automate industrial processes. PLC acts as the brain of an automation system, monitoring inputs from transmitters and sensors, executing the control logic, and communicating with other devices in the system to control outputs through devices such as valves, drives, or other equipment. Different makes of PLCs like Allen Bradley PLC, Siemens PLC, Omron PLC, GE PLC, and Honeywell PLC are available in the market.
Component of PLC
A typical PLC comes in a rack that has components like
- Power Supply Card of the PLC
- Processor or CPU of the PLC
- Communication Card of the PLC
- Digital Input Card of the PLC
- Digital Output Card of the PLC
- Analog Input Card of the PLC
- Analog Output Card of the PLC
- Redundancy Module of the PLC
- Programming
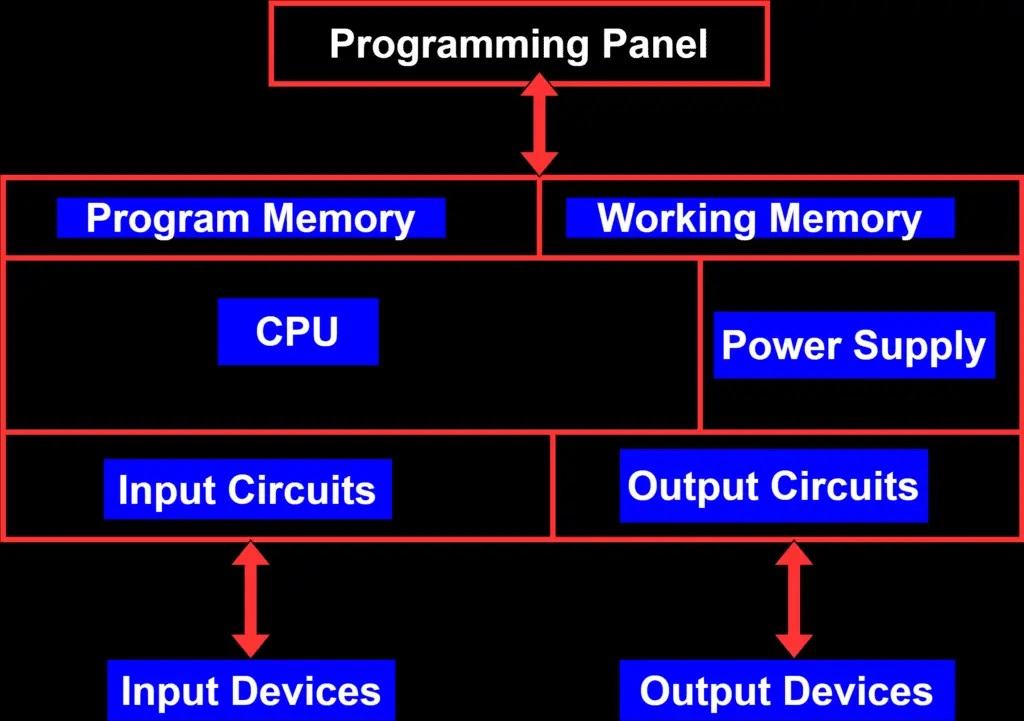
Power Supply Card of the PLC
The power supply card provides electrical power to all the other components of the PLC. The power supply ensures a stable voltage and current supply to the PLC, which is crucial for its proper functioning. Different ratings of power supply are accepted by the power supply card like 230 VAC, 120 VAC, 120 VDC, or 24 VDC depending upon the type.
Processor or CPU of the PLC
The Processor, or the Central Processing Unit (CPU) of the PLC, is the main component of the PLC that executes control logic and manages all other components in the system. CPU has a microprocessor that interprets and executes the program stored in its memory, and it is responsible for monitoring inputs, executing control logic, and communicating with other components in the system.
Communication Card of the PLC
The communication card of the PLC is an essential component of the PLC that facilitates communication between the PLC and other devices in the system. The communication card is responsible for transmitting and receiving data between the PLC and other devices, such as operator interfaces, remote I/O, and other controllers. Different systems like DCS, MCMS, and F&G need to communicate through the PLC. So, through the use of the communication card, communicating these systems with the PLC is easily possible. Mostly, MODBUS, Ethernet, or serial communication is used.
Digital Input Card of the PLC
The digital input card of the PLC is responsible for receiving digital signals from sensors and other devices in the system. The PLC then processes digital signals to control outputs and execute control logic. Some of the digital input devices to the PLC are pressure switch, temperature switch, level switch, flow switch, vibration switch, proximity sensor, limit switch, and feedback of run, trip, and stop from MCC for equipment like pump or compressor.
Digital Output Card of the PLC
The digital output card of the PLC is responsible for transmitting digital signals from the PLC to control actuators, drives, and other equipment in the system. A digital output card is used to give start and stop commands to MCC for equipment like a pump or compressor, for a solenoid valve.
Analog Input Card of the PLC
The analog input card of the PLC is responsible for receiving analog signals from sensors and other devices in the system. The PLC then processes analog input signals to control outputs and execute control logic. An analog input card is used to get data from analog output devices, transmitters like pressure transmitters, flow transmitters, temperature transmitters, level transmitters, different analyzers like pH analyzers, conductivity analyzers, sodium analyzers, silica analyzers, and control valve position feedback.
Analog Output Card of the PLC
The analog output card of the PLC is responsible for transmitting analog signals from the PLC to control actuators, drives, and other equipment in the system. Mostly analog output card is used for control valve command and VFD commands.
Redundancy Module of the PLC
The redundancy module of the PLC is a very important module. Every PLC has a redundant CPU and some other redundant cards like redundant communication modules and redundant Input-Output cards. So, to establish redundancy between them, the redundancy module is used.
Programming of the PLC
PLC programming is as important as the hardware of the PLC. Because the PLC program is the brain of the system. There are different programming languages like Ladder Logic, Function Block Diagram, Sequential Function Chart, Structured Text, and Instruction List. The program is written and loaded into the controller memory.
Why is PLC recommended?
Programmable Logic Controllers (PLCs) are recommended in industrial and commercial automation applications because of the following reasons:
- Reliability: PLCs are designed for harsh industrial environments and are built to be durable and reliable.
- Flexibility: PLCs can be programmed to perform a variety of tasks and can be easily reprogrammed if needed.
- Cost-effectiveness: PLCs are cost-effective compared to other types of control systems, making them an attractive option for small to medium-sized businesses.
- Safety: PLCs can be programmed with safety functions, such as emergency stop circuits, to ensure the safety of personnel and equipment.
- Ease of use: PLCs are user-friendly and can be programmed and maintained by personnel with limited technical training.
- Communication capabilities: PLCs can communicate with other devices and systems, enabling integration with a variety of automation systems.
- High-speed processing: PLCs can process large amounts of data quickly, making them well-suited for complex control applications
In conclusion, a PLC is a complex system that consists of several critical components, each of which plays a vital role in ensuring the proper functioning of the automation system. By understanding each component and its role, you can effectively design and manage PLC-based automation systems to meet your specific requirements.