Harmonics in induction motors adversely affects motor performance, leading to temperature rise and increased losses, decreased torque, and noise problems.
Due to simplicity in construction and ease of operation and maintenance, induction motors have become the most popular prime mover, and about 80 % of the electrical drives are induction motors. An induction motor will perform best if the perfect sinusoidal voltage is fed to the induction motor.
V = Vm * sinϕ
Nowadays, variable frequency drives are widely used in industrial installation because the speed control of the motor can be efficiently and accurately achieved using VFDs.
Variable VFDs use semiconductor devices to convert input sinusoidal voltage to DC and again to a regulated variable voltage/ variable frequency. VFDs’ inverter and converter sections have semiconductor devices like diodes and IGBTs.
The semiconductor devices exhibit non-linear characteristics in applied voltage and current drawn. The nonlinearity of current with applied voltage introduces current harmonics in the electrical network. The harmonic current severely affects the performance of the induction motor.
Analysis of Induction Motor Fed from NON-SINUSOIDAL Voltage Supply
When supply to the induction motor is fed from an inverter or cyclo-converter, the motor terminal voltage is non-sinusoidal but has half-wave symmetry. A non-sinusoidal waveform can be resolved into fundamental and harmonic components using Fourier analysis. Because of the half-wave symmetry of the inverter output, only odd harmonics will be present.
Consider the fundamental phase component VAN = V1 sin wt, VBN = V1 (sin wt –2𝝅 /3), and VCN = V1 (sin wt –4𝝅 /3) with a phase sequence ABC. The corresponding 5th and 7th harmonic phase voltage is
VAN = V5 sin 5wt
VBN = V5 sin 5(wt – 2𝝅 /3) = V5 sin (5wt – 4𝝅 /3 )
VCN = V5 sin 5 (wt –4𝝅 /3) = V5 sin (5wt –2𝝅 /3)
And
VAN = V7 sin 7wt
VBN = V7 sin 7(wt – 2𝝅 /3) = V5 sin (7wt – 2𝝅 /3 )
VCN = V7 sin 7 (wt –4𝝅 /3) = V5 sin (7wt –4𝝅 /3)
The above equation shows that the 7th harmonic has a phase sequence ABC, the same as the fundamental supply voltage. Hence, it is a positive sequence harmonic. The 5th harmonic has a phase sequence ACB; hence, it is a negative phase sequence harmonic. When the motor is delta connected, tripplen( harmonics ( 3,6,9……etc.) circulate in delta winding, and the harmonic current of this order is not reflected at the source end. The motor phase current will be obtained by
I2 rms = I2s + ∑ I2m
m=3,5…
With harmonic current, the motor’s RMS current is higher than the fundamental current. The increased current due to harmonics increases the copper loss substantially. The core loss also increases because of harmonic currents.
Because of increased losses, the motor has to be de-rated because the power output obtained from the machine for the same temperature rise has to be smaller. The efficiency is also reduced due to an increase in losses.
Another important effect of non-sinusoidal supply is the production of pulsating torque due to the interaction between the rotating field produced by one harmonic and the rotor current of another harmonic.
Harmonics orders 5, 7, 11, and 13 significantly contribute to torque pulsations. 5th harmonic produces a backward rotating field, and the 7th harmonic produces a forward rotating magnetic field. As a result, the relative speed between the field produced by the fundamental and 5th and 7th harmonic current is six times the speed of the fundamental.
The same case is with the harmonics orders 11 and 13 that produce torque pulsation whose frequency is 12 times more than that of fundamental. When the motor supply frequency is low, these torque pulsations cause pulsation in speed.
Effects of Harmonics in Motor
The most critical performance parameters of the induction motor are as follows.
- Variation in Torque-speed characteristics
- Reliability Issues
- Torque Reduction
- Cogging and Crawling in motor
- Noise and vibration
- Decreased Efficiency and Temperature rise
- Higher losses due to Skin effect
- Stress on the first turns of the motor winding
1. Torque-speed characteristics
The motor should accelerate the load and continue to output the mechanical power demanded by the equipment. The harmonics in the motor deviate the torque-speed characteristics from its destined curve and negatively impact the motor performance.
2. Harmonics Cause Reliability Issues in Motor
The induction motor’s reliable operation depends on the insulating material’s life. The insulation resistance decreases as the temperature is increased. The harmonic current has a higher frequency, and because of higher frequencies of harmonic current, the eddy current and hysteresis losses increase, leading to the rising of core temperature.
The shaft voltage may also be set up because of increased stray capacitance at higher-order harmonic current. The higher shaft current may cause the bearings to fail. The bearing of the motor’s non-driving end(NDE) side must be insulated, or the shaft must be grounded through the carbon brush.
3. TORQUE Reduction in Motor:
The torque of the machine depends on the rotor input power.
Rotor Input power = Stator Input power – Power losses
Harmonic distortion causes increased losses in motors in the same way as in transformers. However, additional losses arise due to the production of harmonic-generated fields. Each harmonic has a sequence of positive (+), negative (-), and zero (0) sequences that indicate the direction of rotation that would result if it were to be applied to an induction motor with respect to the fundamental.
Harmonic Order | 1 | 2 | 3 | 4 | 5 | 6 | 7 | 8 | 9 | 10 | 11 | 12 |
Phase Sequence | + | _ | 0 | + | _ | 0 | + | _ | 0 | + | _ | 0 |
Zero sequence harmonics (3, 6, 9, 12), the third, and multiples of the third (Triplen) produce a stationary field. Still, since the harmonic field frequencies are higher, the magnetic losses are significantly increased, and the harmonic energy is dissipated as heat.
Negative sequence harmonics result in a counter-rotating field with respect to fundamentals, which results in reduced torque. Positive sequence components produce a forward rotating field that adds to the torque. The positive and negative sequence torque components result in vibration and reduce the service life of the motor.
4. Harmonics in Motor causes Cogging and Crawling :
The 5th and 7th harmonics order current produces a resultant flux distribution in the air gap that can cause a phenomenon called cogging( Refusal to start smoothly or crawl ( run at very high slip ).
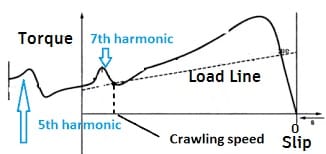
The synchronous speed of the motor is different for different order harmonics. When the motor accelerates, the base speed synchronous speed has to go through the synchronous speed of harmonics. If the load torque is met with the synchronous torque produced with the 7th-order harmonics, the motor speed will increase to 1/7th of the base speed. This phenomenon is known as crawling.
5. Noise and Vibration :
The noise due to asynchronous and synchronous torques is most evident during starting. The vibratory forces are caused when the number of pairs of poles of higher harmonic fields in the stator and rotor differs by 1, a magnetic pull is set up in a certain direction, and this travels around the machine, tending to make the stator-rotor oscillate.
If the pole pairs differ in numbers by more than one, several unbalanced radial forces will travel around the rotor and cause vibration and noise. The higher-order harmonics current produces the audible noise in the motor.
6. Efficiency & Temperature Rise :
A significant effect of harmonic voltage and current in the motor is increased heating due to increased iron and copper losses at the harmonic frequencies. This affects the machine’s efficiency and temperature rise. Due to harmonic, both copper and iron losses increase because both the losses are frequency dependent.
7. Increased Resistance Due to Skin Effect :
The current tends to flow at the outer surface of the conductor with an increased frequency, a phenomenon known as the SKIN EFFECT. The harmonic current has a higher frequency and flows at the outer surface of the conductor.
As a result, the effective area of the conductor gets reduced, and the resistance of the conductor gets increased because the resistance is inversely proportional to the cross-section area of the conductor. The higher resistance leads to higher copper loss( I2R Loss).
8. Higher Stress on Stator Winding
The IGBT PWM inverter fed the voltage to the motor’s stator. The motor receives non-sinusoidal voltage with a high rate of rise voltage( dv/dt) coupled with harmonics. This may lead to uneven voltage distribution in the stator winding, and the voltage of the first few turns of stator winding may rise to 2.5 times the motor’s rated stator voltage. The higher voltage stress on the first few turns on the motor may cause insulation failure.
In conclusion, the harmonics in the motor cause higher losses and deteriorate its performance.
Very informative post indeed!! It helps in better understanding of the scenario occurring in induction motors!!!thanks
Informative, Concise and Understandable