What is Cogging and Crawling?
The phenomenon of cogging and crawling of the induction motor happens due to improper motor design or operation by feeding the harmonic-rich supply source. In the case of cogging of the induction motor, the motor does not accelerate at all, and it gets stalled. The cogging phenomenon is also called magnetic locking.
In the case of the crawling of the induction motor, the motor accelerates up to the speed of 1/7 th or 1/13 th of the synchronous speed of the motor, and it runs at a slow speed. The motor may operate at a lower speed if the load torque is less. The adverse effects of crawling and cogging of the induction motor can be eradicated or minimized by taking care while designing the motor and also by taking care when the motor is operated through variable frequency drive.
Cogging of Induction Motor
The motor may refuse to deliver the torque because of the magnetic locking between the stator and rotor teeth caused by the minimum reluctance If the number of stator slots is equal to or an integral multiple of the rotor slots. The reluctance is minimum when the stator slots are equal to or an integral multiple of the rotor slots.
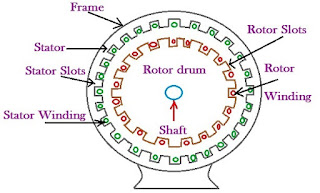
The phenomenon of magnetic locking created between the stator and the rotor teeth is called cogging. Cogging can be avoided using an appropriate combination of the stator and the rotor slots while designing the motor. The cogging in the induction motor is an undesired phenomenon.
Conditions that lead to the Cogging Phenomenon
If the harmonic frequency coincides with the slot frequency, it causes torque modulation and can create the magnetic locking condition. The characteristics of the induction motor of the refusal to start is known as cogging or the magnetic locking or teeth locking phenomenon.
How to reduce the Cogging Phenomenon?
There are the following ways to eradicate the problem of cogging.
- The number of stator slots should not be equal to the rotor slots.
- The rotor slots are skewed. The rotor slots are made not parallel to the axis of the shaft. This arrangement shown in the picture below is called skewing of the rotor.
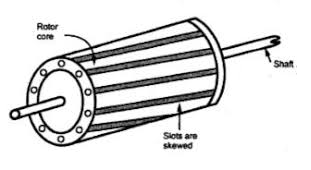
The rotor and stator slot harmonic order:
The stator slot harmonics depend on the number of stator slots and poles. The slot harmonic order generated in the stator is 2Ss/P+/-1, and the rotor slot harmonic order is 2Sr/P+/-1, where Ss and Sr are the numbers of the stator and rotor slots, and P is the number of poles. If the number of stator and the rotor slots are equal for a particular number of poles in the machine, the harmonic order produced will be the same.
Suppose the stator and rotor slot harmonic order are 11th and 13th. The 11th slot harmonic order will produce a backward-rotating field, and the 13th order harmonic will produce a forward-rotating field.
If the 11th harmonic order produces the same backward-rotating field, it is only if the rotor speed is zero. The field produced by the 11th slot harmonic order would be stationary when,
nr-(ns-nr/11)=-ns/11 nr=0 ——–(1) |
The 13th slot harmonic order produced by the stator and the rotor would be stationary if;
2Ss/P+1 = 2Sr/P+1
Ss = Sr ——-(2) |
2Ss /(P-1) = 2 Sr/(P+1)
Ss-Sr =P ——–(3) |
Where Ss and Sr are the stator and rotor slots, respectively, P is the number of poles.
From above, it is clear that the cogging phenomenon will happen if ;
- The number of rotor slots is equal to the number of stator slots.
- The difference between the stator and the rotor slots equals the number of poles.
The above points are considered while designing the motor to avoid cogging.
Solved problems on Cogging and Crawling of Induction Motor
A three-phase 440 volts, 6 poles,50Hz squirrel cage induction motor has the following design data.
The gross length of the stator = 0.20 m
Number of stator slots = 45
Calculate the number of rotor slots for cogging-free operation.
To avoid cogging,
Ss > Sr
Sr # Ss
The rotor slots must be less than 45.
Ss – Sr ≠ ±3P
Sr –±3P ≠ ±Sr →45 -3 x6 → 45 -18 →27
To avoid synchronous hooks and cups in slip torque characteristics
Ss – Sr ≠ ±P, ±2P, ±5P
Ss – Sr ≠ (45 – 6), (45 – 12), (45 – 03) ≠ 39, 33, 15
To avoid noisy operation
Ss – Sr ≠ ±1, ±2, (±P ±1), (±P ±2)
Ss – Sr ≠ (45 – 1), (45 – 2), (45 – 7), (45 – 8)
Ss – Sr ≠ 44,43,38,37
Considering all the above conditions, Sr = 42.
Crawling of Induction Motor
When the induction motor is operated with a VF drive, the harmonics of even and odd orders are generated. The harmonics current produces a rotating magnetic field in the stator, and the flux gets linked to the rotor. As a result, the current starts flowing in the rotor, which produces positive and negative torque with respect to the fundamental supply. The positive and negative torque produced by the various orders of harmonic current increases or decreases the net torque of the motor. The reduction in the net torque deteriorates the efficiency of the motor.
The order of harmonics and the phase sequence of harmonic current are given below.
Harmonic Order | 1 | 2 | 3 | 4 | 5 | 6 | 7 | 8 | 9 | 10 | 11 | 12 |
Phase Sequence | + | _ | 0 | + | _ | 0 | + | _ | 0 | + | _ | 0 |
The phase sequence of the 5th harmonic order is opposite to the phase sequence of the fundamental current. The fundamental current produces the positive torque, and the 5th harmonic order current produces the negative torque. The net torque of the motor is always less than the torque produced by the fundamental current if the voltage fed to the stator is distorted.
Similarly, the 7th harmonic order’s current produces positive torque, and the synchronous speed of the 7th harmonic order is Ns/7. If the torque demand is less, the motor can get a stable point of operation at Ns/7 speed. For example, a motor with a 1500 RPM speed can keep operating at the speed of 1500/7=214 RPM, and the speed of the motor does not increase beyond this point. The phenomenon of running the motor slowly is known as crawling. The motor can crawl at Ns/7 for the 7th harmonic order, and it can also crawl at Ns/13 for the 13th harmonic order.
How do the 7th and 13th Harmonic order Cause Crawling?
The motor’s slip at 5th and 7th order harmonic frequency is expressed below.
s = (Ns- N)/ Ns
The synchronous speed of the motor for fundamental frequency is Ns and equals 120f/P. The synchronous speed of 5th-order harmonics;
( f5=250 Hz) =120*(f5/P)= Ns/5
The slip of the motor at 5th order harmonics
s(5f)= Ns- (-Ns/5)/Ns
s(5f) =1.2
As the slip is more than unity, the 5th-order harmonics will exert negative torque on the rotor.
The slip at the 7th harmonic order
s(7f) = Ns- (Ns/7)/Ns
s(7f) = 6/7
s(7f) = 0.857
The slip at the 13th harmonic order
s(13f) = Ns- (Ns/13)/Ns
s(13f) = 12/13
s(13f) = 0.923
If the torque requirement is less, the motor can continue operating at 0.857 or 0.923 slip for 7th and 13th-order harmonic frequency.
A 1500 RPM motor can get its stable point of operation at 214 and 115 RPM for 7th and 13th order harmonic frequency, respectively. The operation of an induction motor at low RPM is known as crawling.
The torque slip characteristics of the induction motor for harmonics order frequencies are given below.
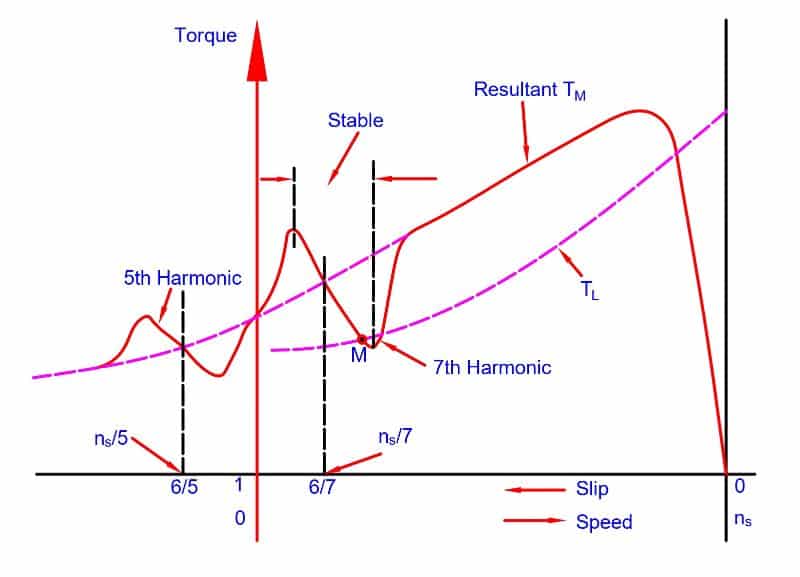
The overall efficiency of the motor operating under harmonic current deteriorates because the harmonic current reduces the motor’s torque and increases the heating in the motor because of higher copper losses. Suppose the sum of the negative torque produced by negative phase sequence harmonics is more than the positive torque-producing current. In that case, the net torque may not be sufficient to drive the equipment, and the motor may refuse to start.
The crawling and cogging are not predominant in slip-ring induction motors. The cogging and crawling are almost absent in wound rotor or slip ring induction motors.
Why is the Cogging absent in a slip-ring induction motor?
In an induction motor, the rotor bars are spaced apart, and the conductor has more spacing between them. The torque produced is not even throughout the revolution. By skewing the rotor bars, the cogging phenomenon can be reduced to a greater extent.
The rotor winding is distributed through slots in a slip ring or wound rotor induction motor. The wound rotor has more slots, and the slots are closer to each other than the slots of the squirrel cage induction motor. This arrangement of wound rotors produces an even magnetic field and more torque throughout the revolution, and cogging is eliminated.
Why is the Crawling absent in the slip-ring induction motor?
The slip ring or wound rotor induction motor produces much more torque than the squirrel cage induction motor. The external resistance added to the rotor resistance boosts the torque of the motor. Thus, the motor quickly passes through the 1/7th and the 1/13th of the motor synchronous speed, and thus the crawling is eliminated.