The starting methods of the synchronous motor are damper winding, external prime mover( DC or induction motor), VVVF method, and slip ring induction motor start method.
Starting of a Synchronous Motor
A synchronous motor is not self-starting, which means the motor can’t simply start to operate when supplied. This is because of the inertia of the rotor. When a three-phase supply is given to the stator, it causes the generation of a rotating magnetic field, which begins to rotate at a synchronous speed instantly. But the rotor can’t rotate instantly due to its inertia of rest, and hence, it remains at a standstill. In order to start a synchronous motor, the rotor must be rotated by external prime movers until it reaches the synchronous speed. Once the rotor speed matches the synchronous speed, the external drive is turned off. The following methods are used to start a synchronous motor.
Methods of Starting Methods of Synchronous Motor
The following methods are used for starting a synchronous motor:
- Using a DC Machine
- Using an Induction Motor
- Damper Winding
- Using Slip Ring Induction Motor
- Using VF Drive
1. Using DC Machine
A DC shunt motor is coupled to the shaft of the synchronous motor. This DC motor is known as the pony motor, which makes the rotor rotate till it achieves a speed near the synchronous speed. Once the rotor achieves the sub-synchronous speed, the DC motor supply is cut off, and the rotor field winding is supplied by a DC source, which results in the rotor synchronization with the air-gap field. The pony motor must have fewer poles than the synchronous motor used.
2. Starting a Synchronous Motor Using an Induction Motor
We must bring the rotor of the synchronous motor to synchronous speed by coupling it with a small induction motor before switching it on. It should be noted that the number of poles of an induction motor must be lower than that of a synchronous motor. If not, the induction motor will not be able to reach the synchronous speed of the synchronous motor. This is due to the fact that the speed of an induction motor is always lower than the synchronous speed, and in order for it to become equal to the synchronous speed of the synchronous motor, its own speed must be increased.
Once the rotor of the synchronous motor reaches synchronous speed, we turn on the DC supply to the rotor and then disengage the induction motor from the synchronous motor shaft.
3. Damper Winding Starting Method:
The most commonly used method of starting a synchronous motor is through the use of damper windings. Damper winding is a short-circuited winding placed on the rotor. As the stator air-gap rotating magnetic field is generated, the damper winding interacts with this field. Being short-circuited, a current is generated within the damper winding, and it generates its magnetic field. As a result, the rotor begins to rotate to reduce and stop the rotor magnetic field according to Lenz’s law of electromagnetic induction (effect opposes the cause – the effect is the generation of rotor field, and the cause is the rotating magnetic field cutting across the damper windings). Once the motor reaches sub-synchronous speed, the rotor field winding is supplied by a DC source to synchronize the motor with the air-gap field.
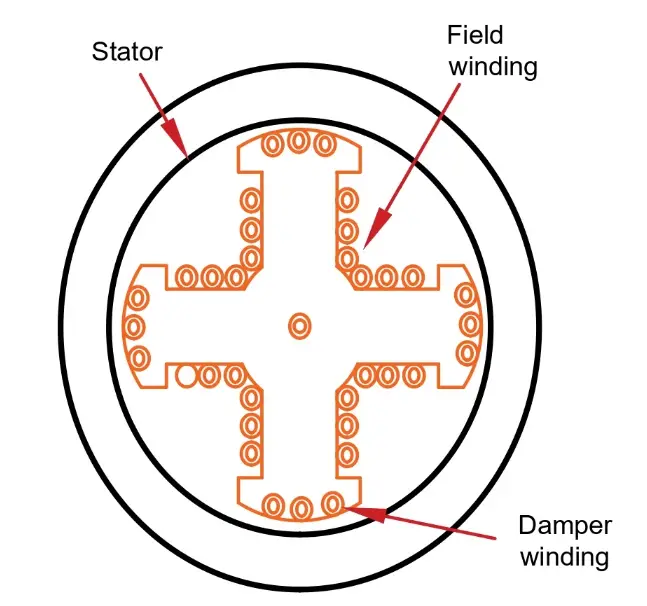
In the case of Damper winding, as evident, the motor begins to operate as an induction motor and then as a synchronous motor. This motor-starting method is used in the case of a salient-pole machine. It also reduces the hunting of the machine during frequent load changes.
4. Starting a Synchronous Motor Using a Slip Ring Induction Motor
To start the motor as a slip-ring induction motor, we connect an external rheostat in series with the rotor, as shown in the diagram below.
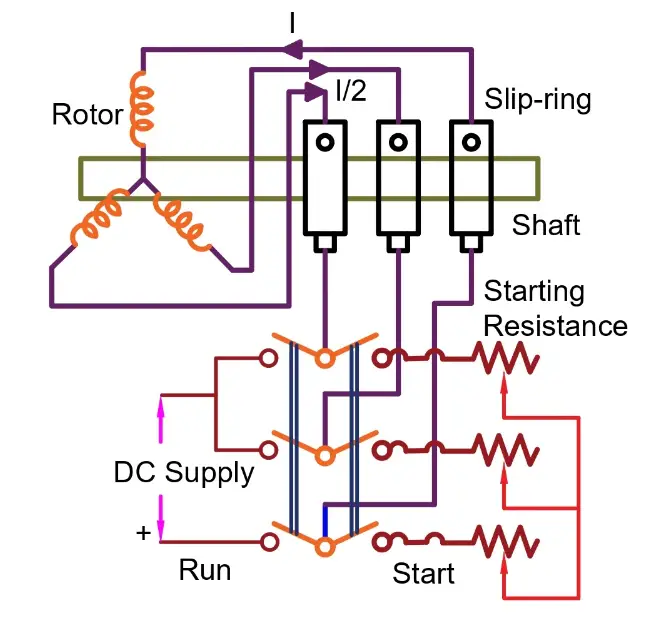
As the motor gains speed, we gradually reduce the resistance until it reaches near synchronous speed. Then, we provide DC excitation to the rotor to pull it into synchronism. Once it is synchronized, it will start rotating as a synchronous motor.
5. V/f or Variable Voltage Variable Frequency Method:
If the stator’s rotating magnetic field in a synchronous motor rotates at a low enough speed, the rotor can easily accelerate and lock in with the magnetic field. The stator magnetic field’s speed can be increased to its rated operating speed by gradually increasing the supply frequency to its normal value of 50 or 60 Hz.
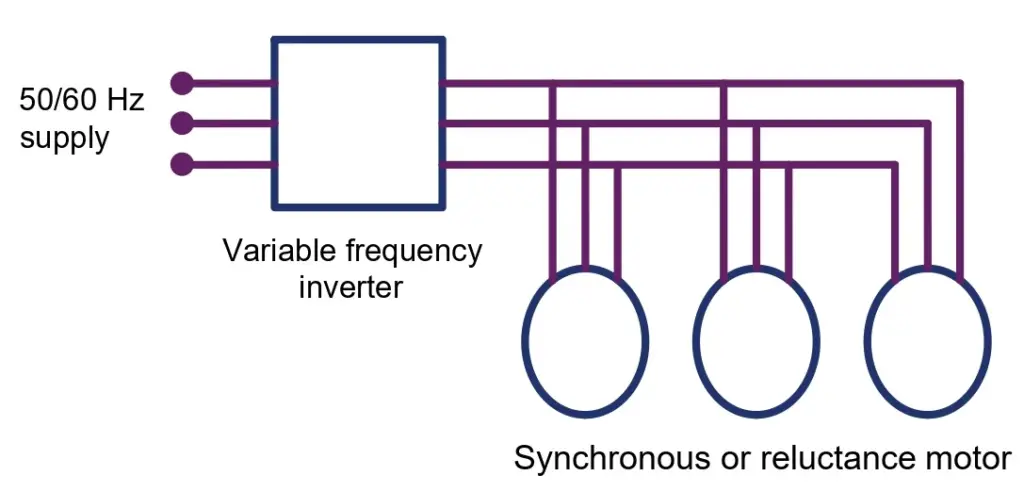
As we know, the synchronous speed depends on the supply frequency. Therefore, in this method, the supply frequency, along with the supply voltage, is reduced during the start, which reduces the synchronous speed and allows the rotor to start rotating. Once the rotor starts rotating, the frequency and voltage are increased gradually to its rated value. It must be noted that the frequency is reduced and increased along with the supply voltage to maintain a constant magnetic flux to avoid the core saturation of the motor. The voltage and frequency are altered in a way such that the maximum magnetic field flux within the machine remains constant. The voltage and frequency are related as
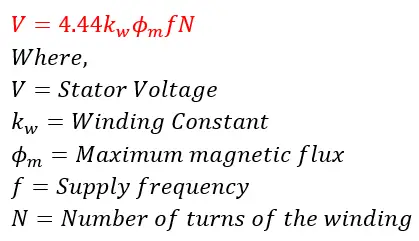
As evident, the maximum magnetic field flux is directly proportional to the v/f ratio because everything else is constant in a machine. so,
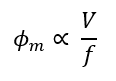
Thus, voltage and frequency are altered together to keep the maximum magnetic field flux constant to avoid saturation as well as a fall in the maximum torque of the machine.