Dry running a pump is a serious problem and must be avoided to prevent damage to the pump. When a pump runs dry, it generates enormous heat and force for which the pump is not designed and it can not handle that much heat and force. As a result of increased temperature and force, wear and tear in pump parts happens and that can quickly add up to inflated repair costs. Therefore, it is paramount not to run the pump dry in any case.
A pump is a mechanical device that is used to suction a liquid and discharge the same into its outlet with great force. This force is also sometimes called head or pressure. For a pump to function properly and safely, a minimum amount of liquid level must be ensured in its suction.
If the pump runs without any liquid, i.e., if a pump runs dry, it can be dangerous for its life and shorten its performance. In certain cases, a dry run of the pump can cause permanent damage to the pump. This may also lead to downtime of the equipment and also the process if any standby pump is not available.
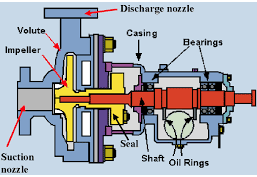
Dry Run of Pump
The dry running of the pump, as it sounds, means the pump is operated without liquid. Every pump needs some amount of fluid level to be maintained while the pump is running. When this flow is not maintained and the pump still runs, it is called dry running of the pump. A dry run of the pump can occur accidentally or intentionally. Commonly, a dry run of the pump happens due to human error, or how the pump is operated, monitored, and controlled.
Problems with Pump Dry Running
When a pump is run dry, some common results are seen. They are:
- The Impeller will melt along the shaft, causing the impeller to seize onto the shaft. If the impeller seizes, it will stop and would not rotate. For correcting this, the pump must be taken apart and a drill bit must be used to clean out the bore of the impeller.
- The rear housing may melt. A hole can develop in the rear housing, because of which liquid can escape. Sometimes, the boss of the rear housing, which secures the pump shaft, would get deformed. This would allow the shaft to move instead of remaining stationary. Due to this, the damage is caused to the impeller. Due to this, the impeller may bounce on the shaft which can result in the breaking of the shaft.
- The shaft in the ceramic may break due to thermal shock.
- The rotating bushing may block the shaft.
- In the case of a plastic pump, some plastic parts may melt. For example, the impeller, rear casing, internal magnet, etc. This is because of the sudden temperature rise during the dry run.
- Cavitation of pump: – Cavitation of the pump is a situation in which air bubbles are formed in the fluid flowing through pumps, which will rapidly collapse. These can cause issues like internal erosion of pumps. It damages the pump seal and the impeller.
The amount of time it takes for a pump to suffer damage from running dry depends on many variables like pump size, bore size, the liquid used in the pump, etc.
How to Prevent Pump Dry Running
Because dry run in a pump is normally caused by human error, dry running of a pump can be avoided by some sensing elements in the fluid line. This would help control the level of liquid. A pressure sensor or a transmitter may be installed in the suction line.
When pressure drops below a predefined set point, then the pressure sensor or pressure transmitter would generate an electrical output. This electrical output can be used in the control wiring to shut off the pump supply.
When PLC control is used, the pressure sensor or pressure transmitter input is provided to the PLC. If the PLC is controlling the pump, the pump will be turned off according to the program written. If a pressure transmitter is used, then a logic is written which would compare the transmitter input with a predefined set point in the PLC.
In cases where the pump is sucking liquid from a tank, and installing a pressure-sensing device is not feasible, level sensors or level transmitters can be installed. The PLC input is from the level sensor or level transmitter. In this case, the PLC will shut off the pump output when the level is below a preset limit.
In some cases, a flow sensor or a flow transmitter is installed in the pump suction line. Here, the flow sensor would measure the flow rate of liquid in the suction line of the pump. The input to the PLC is from the flow sensor or flow transmitter. The logic in the PLC is written such that the pump turns off when the flow rate is below a pre-defined set point.
Generally, flow switches are used in the suction line of the pump. Whenever the flow switch
Safe Options for Dry Pumping
For applications like tank transfer, where the tank needs to be emptied, the pump may run dry for a few seconds. If the pump is in a dry run state for less than 45-60 seconds, it should not suffer any damage. Whenever it is known that the pump may be in the state of a dry run for emptying the tank, operators must take care and ensure that the pump is run dry for the minimum amount of time. If a pump suffers from a dry run, it is not covered in warranty. Dry running may be an expensive hazard for the equipment but when taken care of and properly supervised, the life of machinery can be elongated.