In this article, we will discuss the types of overhead conductors used for the overhead transmission line. In this article, we will also discuss the followings.
- Properties of Conductor
- Types of Conductor
- Application
- Thermal Characteristics of conductor
A conductor, or electrical conductor, is a substance or material that allows electric current to flow through it. In a conductor, electrical charge carriers, usually electrons or ions move easily from atom to atom when voltage is applied. Metals like copper, iron, silver, aluminum, and gold are good conductors of electricity.
The conductor is a very important component for electric power transmission whether it is an overhead or underground transmission. The selection of an electrical conductor is a very important criterion for good power transmission efficiency.
Properties of Overhead Conductor
An ideal conductor must have the following features.
- High electrical conductivity
- High tensile strength so as to withstand mechanical stresses
- Relatively lower cost without compromising much of other properties
- Lower weight per unit volume
Types of Overhead Conductors
In ancient days copper conductors were used for overhead transmission lines, but nowadays Aluminum and aluminum alloys are widely used for this purpose.
- Aluminum is less costly than Copper.
- When we use an aluminum conductor in place of copper, we have to take a larger cross-section area of aluminum. We know, the corona effect is less with the conductor that has a larger diameter. Therefore, if we use an aluminum conductor, the corona loss is minimum. The corona effect is the ionization of surrounding air due to high voltage which causes violet light around the conductor.
The aluminum conductor also has some disadvantages over the copper conductor. They are as follows.
- The aluminum conductor has a lower tensile strength and causes more sag. The tensile strength can be improved by the use of aluminum alloys. The tensile strength of aluminum and copper is 50-100 and 150-300 N/Sq.mm respectively.
- The conductivity of the copper and aluminum at 20°C is 5.98×10⁷ S/m & 3.5×10⁷ S/m respectively. Therefore, the conductivity of the aluminum conductor is about 0.58 times the conductivity of the copper conductor. We can say the conductivity of aluminum is lower than that of copper conductors.
- The aluminum conductor needs a larger diameter as a transmission conductor, as a result of increased surface area, the conductor experiences more air force and thus it swings more in the air than copper. Therefore, a larger cross-arm is required which increases the cost.
Basically, stranded conductors are used in overhead transmission lines than Solid Conductors. The reason is that stranded conductors offer more flexibility than solid conductors. The flexibility of stranded conductors is a good property that makes them easier to install and have longer life as compared to solid conductors. Also, the stranded conductors are capable to withstand more vibration and bending before breaking. Now we discuss the types of conductors used in the transmission line.
AAC (All Aluminium Conductor)
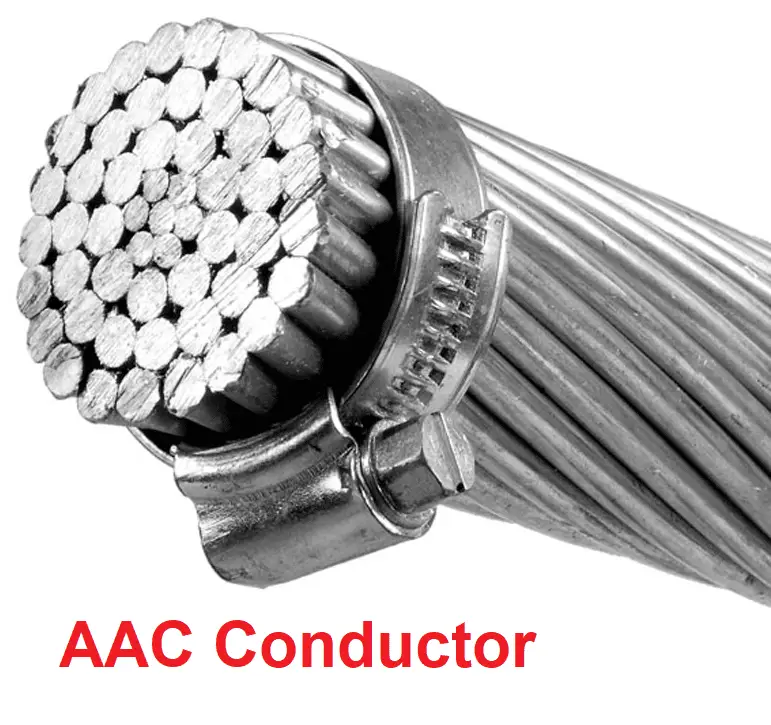
The pros and cons of the AAC (All Aluminum conductors) are given below.
- In comparison to other categories of transmission line conductors, it has lesser tensile strength and more sag per span length. Therefore, these conductors are suitable for distribution lines that have a lesser span compared to the transmission line.
- Better conductivity than ACSR at a lower voltage. Therefore, they are best suited at the power distribution level.
- The cost of an AAC conductor is at par with the ACSR conductor.
ACSR (Aluminium Conductor Steel Reinforced)
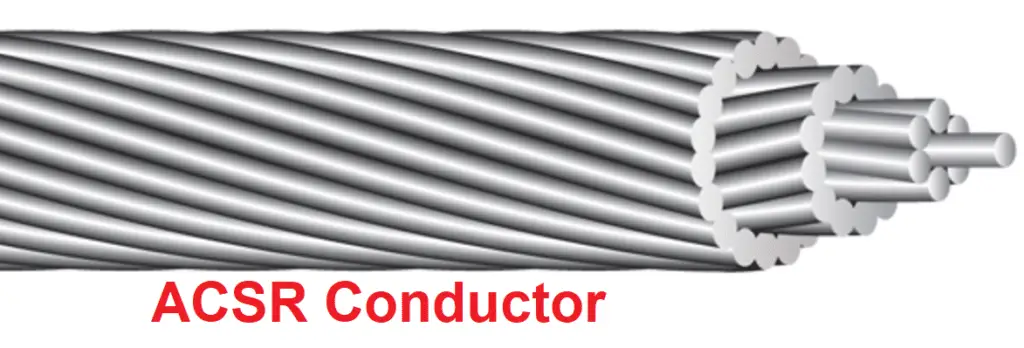
- The Strands of the ACSR provide flexibility. The flexibility in the conductor is a good property that prevents breakage and minimizes the skin effect.
- ACSR has a solid or stranded steel core. Around the steel core, there may be one or more layers of high-purity aluminum wires wrapped in a spiral manner.
- The core wires are zinc-coated (galvanized) steel or aluminum-coated (aluminized) steel.
- The steel core in the central part of ACSR provides additional mechanical strength and, hence, it has very less sag compared to all other aluminum conductors.
- It provides minimum sag, therefore it is best suited for longer spans.
- The number of strands in ACSR may be 7, 19, 37, 61, 91, or more. And a number of strands can be selected as per the application.
- The number of strands in ACSR is shown by x/y/z,
- Where ‘x’ is the number of aluminum strands, ‘y’ is the number of steel strands and ‘z’ is the diameter of each strand.
- If the filler, like paper, separates the aluminum and Steel strands, then this kind of ACSR is called expanded ACSR and it is used in EHV lines.
AAAC (All Aluminium Alloy Conductor)
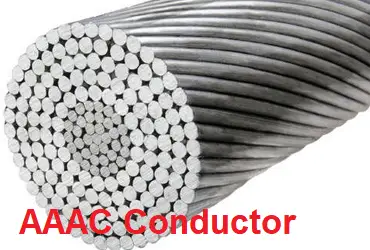
- AAAC has the same construction as AAC, except for the alloy.
- Its strength is equal to ACSR.
- It is light in weight due to the absence of steel.
- AAAC is expensive because it has alloy in it.
- It can be used for a longer span because its tensile strength is better than AAC. Therefore, it can be even used at the distribution level in applications like river crossing.
- AAAC has a lesser sag than AAC.
- The AAAC is lighter in weight compared to ACSR. Therefore it can be used in transmission and distribution where we use lighter support, such as mountains, swamps, etc.
- The difference between ACSR and AAAC is the weight. Being lighter in weight, it is used in transmission and sub-transmission where the lighter support structure is required such as in mountains, swamps, etc.
ACAR (Aluminium Conductor, Aluminium Reinforce)
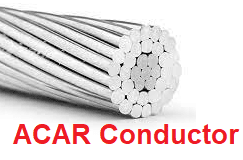
- It is apt to corrode, however, it is cheaper than AAAC.
- ACAR is suitable for transmission as well as distribution lines.
- The electrical and mechanical properties of ACAR are at par with ACSR conductors.
- ACAR is constructed by adding high-strength Aluminum-Magnesium-Silicon alloy to high-purity aluminum.
Summary of Types of Overhead Conductor in Tabular Form
Conductor | strength | sag per span | application |
AAC : All Aluminum Conductor | low | high | Distribution lines are extensive use in urban areas where spans are usually short |
AAAC: All Aluminium Alloy Conductor | equal to ACSR but due to the absence of steel it is light in weight | stronger tensile strength than AAC and is used for longer spans with lesser sag than AAC | sub-transmission where a lighter support structure is required such as in mountains and in corrosive environments |
ACSR: Aluminium Conductor, Steel Reinforced | Steel Strands provide more strength | longer spans keeping sag minimum | Transmission lines |
ACAR: Aluminium Conductor, Alloy Reinforced (concentrically stranded Wires of Aluminium on high strength Aluminium-MagnesiumSilicon (AlMgSi) Alloy core). | better than ACSR and AAAC | better than ACSR and AAAC | where the ampacity, strength, and light weight are the main consideration of the line design |
Number of strands in a stranded conductor
If there are n layers of strands in a stranded conductor-Number of strands of the conductor is;

Calculation of the overall diameter of the conductor
If d is the diameter of a single strand in the conductor, the overall diameter of the conductor is (2n+1)d mm.
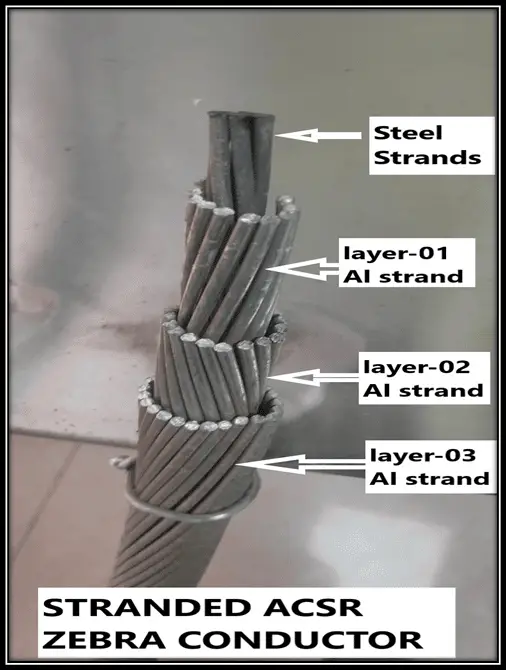
Application
For 132 kV lines ‘Panther’ ACSR Conductor is used that has 7-strands of steel of dia 3.00 mm and 30-Strands of Aluminum with a diameter of 3.00 mm. Similarly for 220 kV lines ‘Zebra’ ACSR conductor is used that has 7-strands of steel of diameter 3.18 mm and 54-Strands of Aluminum of diameter 3.18 mm. For 400 kV lines, Twin ‘Moose’ ACSR having 7-Strands of steel of diameter 3.53 mm and 54-Strands of Aluminum of diameter 3.53 mm is used.
Hollow Conductor
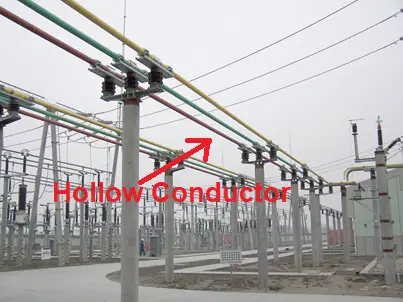
Hollow conductors have a larger diameter in comparison to solid conductors. The corona power loss is less due to the large diameter of the conductor. The skin effect in the hollow conductor is less as compared to the stranded conductor.
Stranded conductors can be used in transmission systems at up to 220 kV. But it is impractical to use a single-stranded conductor for the voltage beyond 220 kV systems. For ultra-high tension lines, the hollow conductor can be used to optimize the flow of electric current through it. But erection and maintenance of hollow conductors in the Extra High Voltage system are not economical. The problem is solved by using bundled conductors instead of the hollow conductor in the electrical transmission system above 220 kV voltage level.
Bundled Conductor
- A bundle Conductor is defined as the combination of more than one conductor per phase in parallel suitably spaced from each other in a transmission line. The individual conductor in a bundle is defined as Sub-conductor.
- The major advantage of bundled conductors is their ability to reduce corona discharge. Less power loss due to the reduction in the formation of corona discharge leads to improved transmission efficiency.
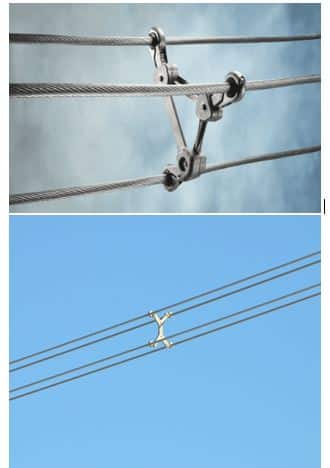
Thermal Characteristics of conductor
When a conductor is exposed environment, it has to encounter the weather surrounding of it. In any aluminum conductor like ACSR or other conductors, the whole conductor is not uniform. The current carrying capacity is not only dependent upon atmospheric temperature but also depends on the wind flow, solar radiation, proximity effect, skin effect, etc.
METEOROLOGICAL/ENVIRONMENTAL CONDITIONS
- Solar radiation– heat dissipation due to radiation including solar radiation with ambient temperature
- Wind velocity– Due to wind velocity the heat dissipates from the conductor to the surrounding atmosphere which reduces the temperature of the conductor. Thus, the ambient temperature affects the current carrying capacity of the conductor.
- Ambient temperature- With variations in ambient temperature, the vibration of metal ions varies. This further cause a change in the resistance of the conductor. The resistance of the conductor increases with an increase in the ambient temperature.
CONDUCTOR SURFACE CHARACTERISTICS
- Age of the Conductor.
- Maximum design conductor temperature.
- Allowable losses of the strength of aluminum metal at design temperature.
SKIN EFFECT
- When an Alternating Current flows through a conductor, it is not distributed uniformly throughout the conductor cross-section. AC current has a tendency to concentrate near the surface of the conductor and the phenomenon is known as the skin effect.
- Due to the skin effect, the effective cross-section of the conductor through which the current flows is reduced. Consequently, the effective resistance of the conductor is slightly increased.
PROXIMITY EFFECT
- When two or more conductors carrying alternating current are close to each other, then the distribution of current in each conductor is affected due to the varying magnetic field of each other. This is known as the Proximity effect.