Classification of Control Valves: We can classify the Control valves based on the application, function, motion, port size, and failure states. According to the classification of control valves, the classes of valves are Globe Valve, Gate Valve, Butterfly Valve, Check Valve, Ball Valve, Disk Valve, Diaphragm Valve, Linear Valve, and Rotary Valve.
Table of contents
Classification of Control Valves
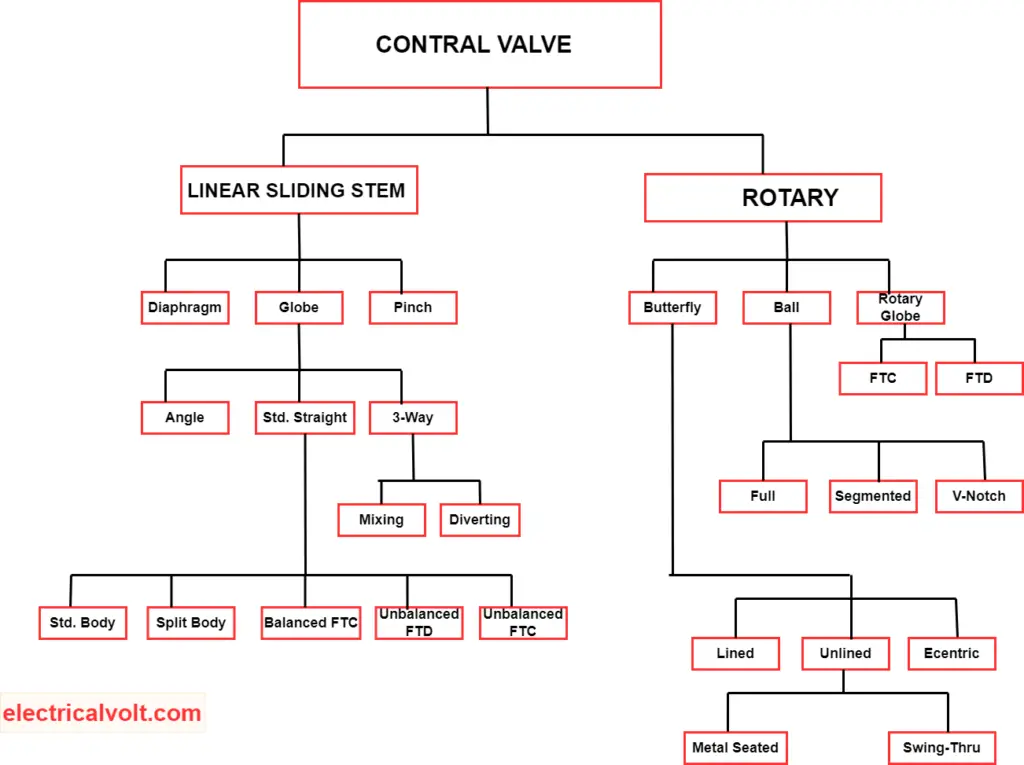
1. Classification of Control Valves-Based on the application
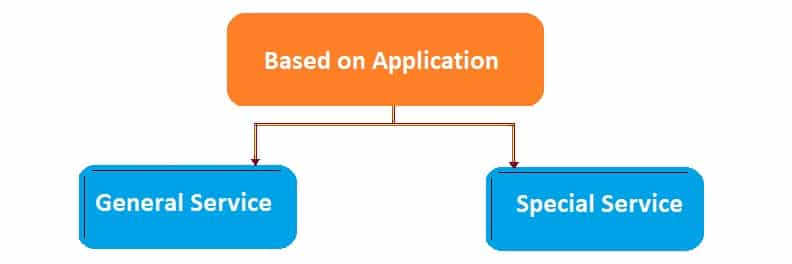
According to applications, We divide the Control valves into two categories- General Service and Special service.
General Service:
- General Service valves are suitable for most common applications.
- Generally, they have a lower pressure-rated category.
- Its pressure ratings lie between ANSI class 150 and 600.
- General Service valves are not suitable for corrosive fluids and high-temperature service.
- Fewer chances of cavitation or flashing.
- To some extent, general service valves are exchangeable.
- Flexibility Built into the design suits them best for a broader range of applications.
- General Service valve body materials are stainless or carbon steel.
Special Service:
Special service valves are suitable for severe service applications. The valve has special features to handle unstable applications. The special service valve can handle high-pressure drops. As we know, the high-pressure drop causes severe cavitation, flashing, choking, and high noise. Special service valves have engineered trims in globe-type and ball-type rotary valves to prevent the high-pressure drop problem.
2. Control Valve Classification- Based on function
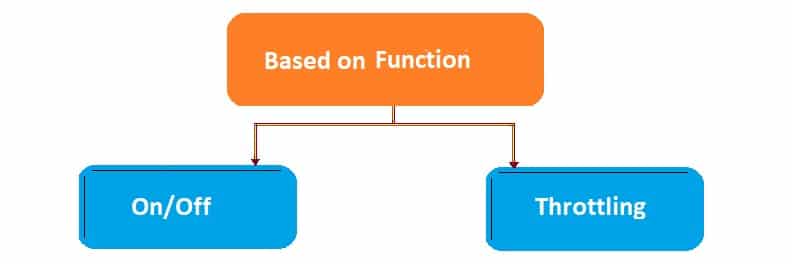
On/off Control Valve:
On-off valves or block valves allow or block the fluid flow. The valve is completely shut off or open. Examples of on /off valves are ball, gate, plug, pressure relief, and tank bottom valves.
On-off valves are generally used for applications where there is a need for flow to be diverted around an area. This need arises when,
- Maintenance is being performed.
- Personnel working need to be protected from potential safety hazards.
- Used in mixing applications where fluids are combined for a predetermined amount of time without measurement.
- Safety management systems also require automated on-off valves to promptly shut off the system in emergencies.
Pressure relief valves are self-actuated open-close (on-off) valves. Pressure relief valves open only when pressure exceeds the preset value. Thus, these valves guard against the over-pressurization of a liquid service. On the other hand, safety valves (on-off) are most suitable for gas applications. The safety valve vent opens during the over-pressurization of the system. Failing of a safety valve leads to a safety or process hazard, and it may cause untoward incidents in the plant.
Throttling:
Throttling valves allow the flow regulation at any point between fully open to fully closed. The plug valve and throttling valve are suitable for on-off and throttling. Globe valve is suitable for on-off and throttling service.
3. Control Valves Classifications-Based on the motion
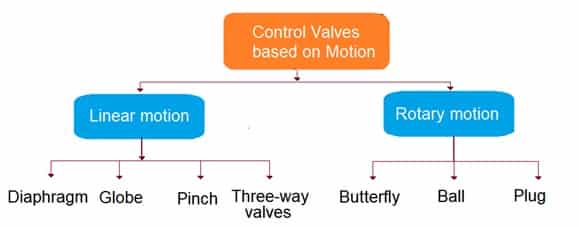
Linear motion:
Linear motion valves or linear control valves are the most common valves. This type of valve has a sliding-stem design. The sliding-stem design makes it move the closure element into an open or closed position.
Examples of the basic linear valves are Globe, Pinch, and Diaphragm.
Linear valves have the following features.
- Simple design
- Easy maintenance
- Versatility with more size
- Range of pressure class
- Design options than other motion classifications.
Rotary motion:
Rotary–motion valves use a rotary closing element that moves through a quarter-turn or 45-degree range to open to allow the flow or close to block the flow.
- Rotary valves are generally smaller in size
- Weigh less than comparable linear valves
Butterfly and Ball valves are basic examples of rotary motion valves. Butterfly valves are suitable for low and modest-pressure service. Ball valves require less maintenance and have the greatest flow capacity among all control valves.
Application-wise, rotary valves are confined because of specific pressure drop issues. Rotary valves are prone to cavitation and flashing problems. However, rotary-valve has advanced designs. And rotary valves can overcome these inherent limitations. Nowadays, the use of rotary valves is on an increasing trend.
4. Classifications Based on port size
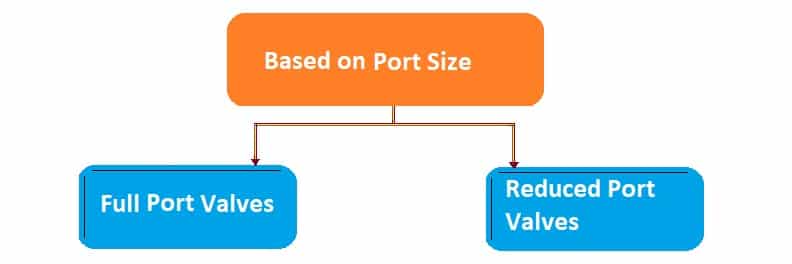
Reduced port valves:
Reduced-port valve closure elements limit the flow. The flow area (seating) of that port of the closure element is substantially smaller than the full port. It is approximately one pipe diameter on gate valves and 60 percent of the full bore on the ball valves.
The primary purpose of reduced-port valves is to regulate the flow by reducing the flow or through throttling.
Full Port valves:
Full port or bore valves are most suitable for high flow capacity. Ball and gate valves have relatively large internal flow passageways in the valve body. Thereby, it allows smooth flow without significant restriction.
Such valves are called full-port valves because the internal flow is symmetrical to the full area of the inlet port.
Full-port valves are widely used in on-off and blocking services, where the flow must be stopped or diverted.
5. Valve Classification Based on the action in failure states
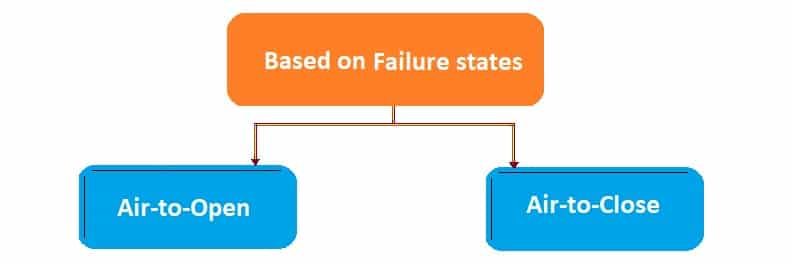
Air-to-close:
The plug on the stem of the air-to-close valve closes the orifice to stop the fluid flow when the air pressure input signal above the diaphragm increases. The plug opens the orifice if the air pressure input signal is unavailable or air pressure comes down. These types of valves are also called fail-open valves. The pic is shown in the figure below.
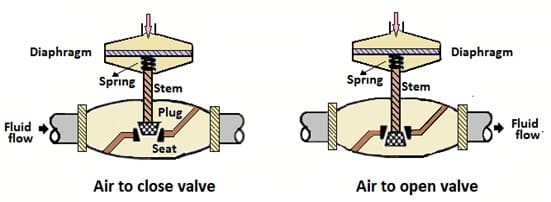
Air-to-open:
The plug on the stem of the air-to-open valve opens the orifice to allow the fluid flow when the air pressure input signal below the diaphragm increases. The plug on the stem stops the fluid flow when the air pressure input signal is unavailable, or air pressure comes down. An air-to-open valve is shown in the image below.
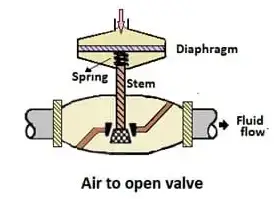
- Types of Control Valves Noise
- How to Reduce the Control Valve Noise?
- Control Valves Pre-Commissioning Checklist
- Common Terms Used in Control valve
- How does the Diaphragm Valve works?
- Basics of Globe Valves
- Advantages and disadvantages of gate valves
- Self-actuated Temperature Regulator-Principle types
- Impulse line – Purpose & Tapping Point Location
- What are Linear Control Valves and rotary Control Valves?
- Types of Check Valves