There are 8 types of check valves, including swing, tilting disk, water check, dual plate wafer, spring loaded, position check, ball check, and non-slam. Check valves are the valves that are used to prevent the backflow of fluid in a piping system. A check valve is also known as a non-return valve (NRV). Check valves are one-way valves designed to open with fluid movement and pressure. The check valve closes to prevent the backflow of pressure to the upstream equipment, for example, the pump and compressor.
Table of contents
Types of Check Valves
The different types of check valves are:
- Swing Check Valves
- Tilting Disk Check Valves
- Wafer Check Valves
- Dual Plate Wafer Check Valves
- Spring Loaded Check Valves
- Piston Check Valves
- Ball Check Valves
- Non-Slam Check Valves
Let us have a brief overview of all types of check valves.
Swing Check Valve
The swing check valve is available in two body designs: a straight body design and a y-pattern design.
The construction of a swing check valve consists of the valve body mounted with a disc that swings on a hinge or shaft. The disc will swing off the seat, allowing forward flow. When the flow is stopped, the disc swings back onto the seat, blocking the reverse flow. The swing check valve will offer very little resistance to the fluid flow.
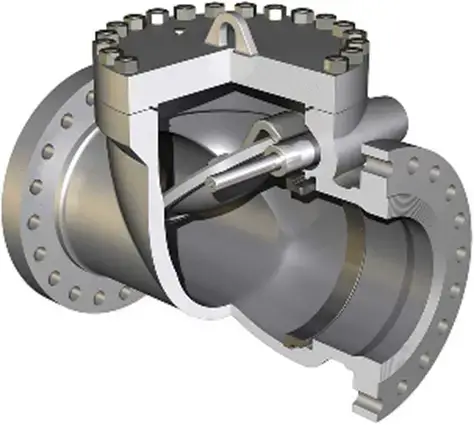
The swing check valves are used where the risk of pressure surges is low. Because of the full bore opening, a swing check valve is usually used for water and wastewater applications. A swing check valve is used in 2 inches and above pipe sizes. A swing check valve can be installed in either a vertical or horizontal position.
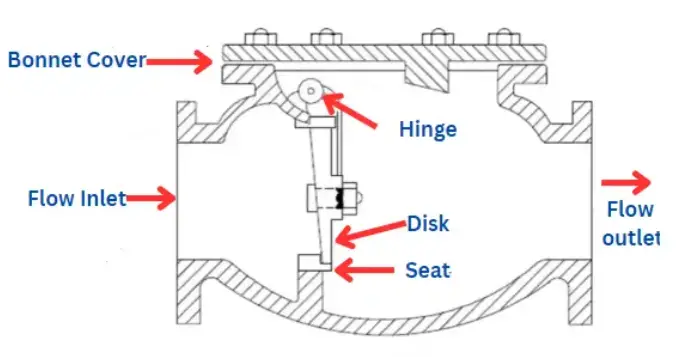
Advantages
- Turbulence and pressure drops in swing check valves are very low.
- Swing check valves have replaceable seat rings.
- The angled seating surface of a swing check valve enables easy opening at lower pressures.
- Swing check valves have positive sealing and experience less shock when closing under higher pressures.
Disadvantages
- Swing check valves cannot be used in systems that have pulsating flow, as the continuous flapping can be destructive to the seating elements.
- In a swing check valve, the closure response is slower than in other check valves because of the more extended disk travel and inertia of the disk.
Tilting Disk Check Valve
The tilting disk check valves are designed to fit between two flanges and provide a compact installation for large-diameter applications. The tilting disk check valves can be installed in vertical or horizontal lines.
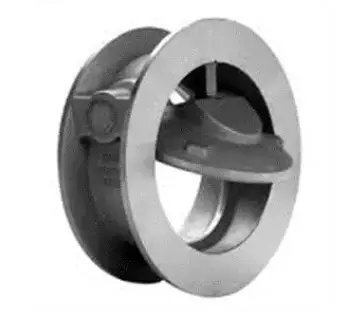
A shaft holds the disk in place in a tilting disk check valve. The shaft is positioned eccentrically from the valve body’s center line on horizontal and vertical axes. Because of the double eccentricity of the shaft, the lower section of the disc will occupy a greater area in the flow path. Hence, the disc will begin to flow at very low flow rates. The tilting disk check valves provide a quick closing response. The tilting disk check valves are best suited for pulsating flows with compressible fluids.
Advantages
- The tilting disk check valves have a very low-pressure drop.
- The tilting disk check valves are fast-closing valves.
- The tilting disk check valves do not stick in dirty systems, which means they operate satisfactorily.
- The tilting disk check valves minimize the risk of disk slamming.
Disadvantages
- The tilting disk check valve cannot be used in rapidly fluctuating flows.
The seat tightness can deteriorate at a low differential pressure in the tilting disk check valve.
Wafer Check Valve
The wafer check valves are compact and slim in design. The wafer check valves have a swinging disk to allow or block fluid flow. The wafer check valves are light in weight and have been used in various applications. The wafer check valves are available in various sizes. The wafer check valves are economically feasible.
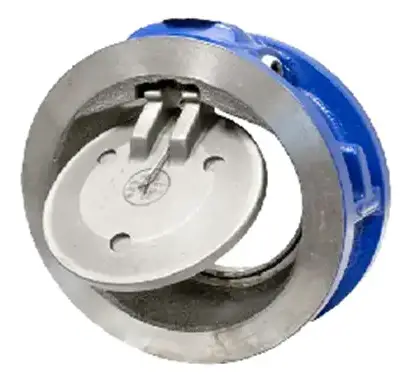
The wafer check valves can be used in services that require low-pressure loss. The wafer check valves operate at very low-pressure differences. In the wafer check valves, the eccentric disc shaft combination and the disc seat provide a positive shut-off of the returning media. The wafer check valves are suitable for mounting between slip-on or weld-neck-type companion flanges of different standards.
Advantages
- Compact in design.
- Low-pressure losses
- Relatively low cost
Disadvantages
- The wafer check valves are not appropriate for use in applications that involve pulsating fluid flow.
Dual-Plate Wafer Check Valve
The dual-plate wafer check valve is almost similar to the wafer check valve. But in the dual-plate wafer check valve, two spring-loaded plates are hinged on a central hinge pin.
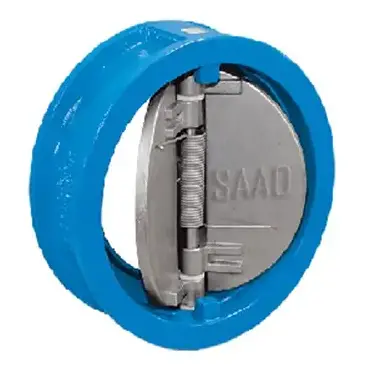
When there is a decrease in the flow rate, the plates will close before the reverse flow takes place due to the action of the torsion spring. Dual-plate wafer check valves are also called silent check valves and butterfly check valves.
Advantages
- The dual-plate wafer check valves have a low weight.
- The dual-plate wafer check valves require less space.
- The dual-plate wafer check valves are suitable for high flow rates.
Disadvantages
- The dual-plate wafer check valves have a higher pressure drop compared to the other check valves.
- In the dual-plate wafer check valves, there are chances of plate interference.
- The dual-plate wafer check valves are less suitable for low flow rates.
Spring-loaded Check Valve
Spring-loaded check valves are of two types: spring-loaded in-line valves and spring-loaded Y-valves. The spring-loaded in-line valves are also known as nozzle check valves or silent check valves. The spring-loaded in-line valves have a centrally guided stem-disc assembly and a compressor spring.
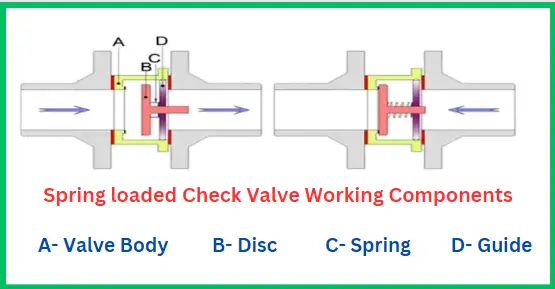
The fluid flow pressure should be greater than the spring force and cracking pressure for opening the spring-loaded in-line valve. When the inlet flow pressure exceeds the spring force and cracking pressure, the flow will push the disc, allowing the flow. When the inlet flow pressure reduces, the spring will push the disc against the orifice, returning it to its original position and shutting the valve.
The principle of operation of the spring-loaded y-check valves is almost identical to that of the in-line check valves. The difference between them is that the spring and movable disc are positioned in a ‘Y’ shape in the case of spring-loaded y-check valves. In spring-loaded y-check valves, there is the advantage that the valve can be inspected and serviced even when the valve is connected to the system.
A spring-loaded check valve finds low-risk applications where zero backflow is desired, such as HVAC systems, sprinkler pumps, etc.
Advantages
- The spring-loaded check valves are versatile.
- In the case of the water hammer condition, the spring-loaded check valves are more capable of diminishing any disruptive noises.
- Complete sealing is achieved with the spring-loaded check valves, and no backflow occurs.
Disadvantages
- The spring-loaded check valves are more expensive as compared to other check valves.
Piston Check Valve
The piston check valves are very similar to the lift check valves. The piston check valve has a piston and cylinder in its construction, which provides a cushioning effect during operation. The flow characteristics of a piston check valve are almost identical to those of a lift check valve.
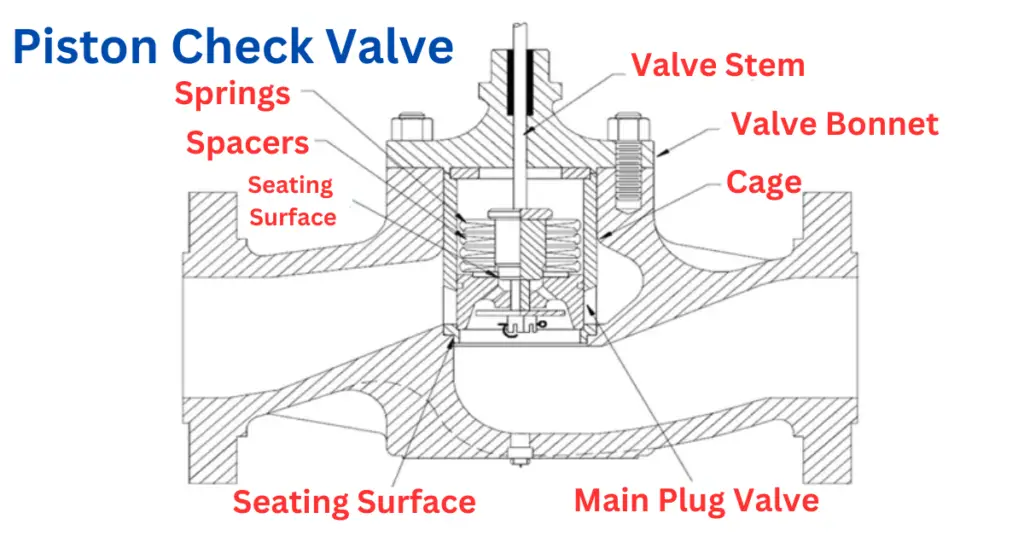
The piston check valves are used in conjunction with the globe and angle valve within the piping systems where flow direction is frequently changed. The piston check valves are used in water, steam, and air system applications.
Advantages
- The piston check valves are durable and versatile.
- The piston check valves support automatic operation.
- The piston check valves can maintain pressure.
- The piston check valves have a low-pressure drop.
- The piston check valves have zero fluid leakage.
Disadvantages
- The piston check valves are prone to water hammer problems.
Ball-Check Valves
In the ball-check valve, a ball inside it moves up and down, letting the flow pass or blocking it. The seat of the ball-check valve is machined in such a way that it fits the ball.
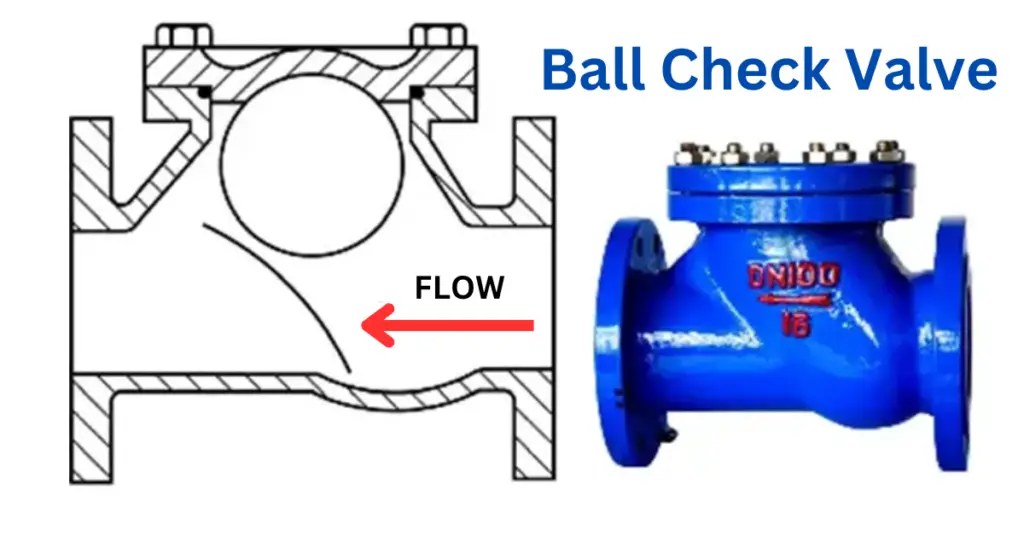
The chamber of the ball-check valve has a conical shape to guide the ball to the seat for sealing and stopping the reverse flow. Ball-check valves have applications in small pumps and low-head systems. The ball-check valves work well in both water and wastewater applications.
Severe slamming may be seen in the ball-check valves at high pressures and dynamics.
Advantages of ball-check valves:
- Compact in size
- No external parts
- Low-cost
- High reliability.
Disadvantages of ball-check valves
- In some instances, the ball-check valves do not have an open-close indicator.
Non-Slam Check Valves
The non-slam check valves resolve the issue of stress on the piping system with the swing check valves.
In the swing check valves, the abrupt closure of the disc due to gravity will cause a pressure surge, which results in shock waves. The high-pressure shock waves are capable of causing severe stress on the piping system.
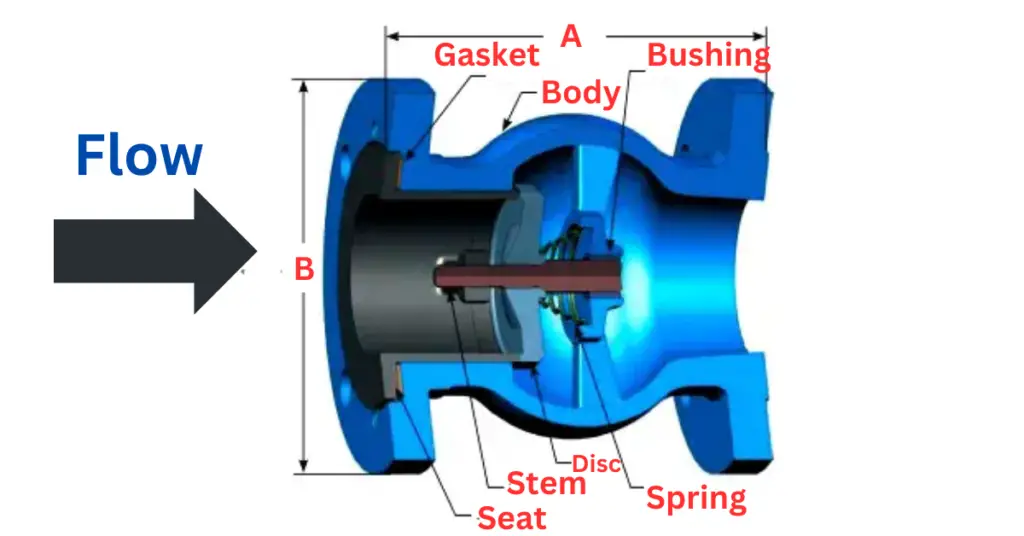
By using non-slam check valves, this issue is eliminated. The non-slam check valves do not depend on gravity. When the upstream velocity of the fluid decreases, the spring assist on the valve will start to close the disc. Thus, the disc will be completely closed when the upstream velocity comes to zero. The force necessary for producing a water hammer on both sides of the valve is also reduced significantly.
Advantages of non-slam check valves
- The non-slam check valves have a short stroke. So, the non-slam check valves facilitate soft closing quickly in the case of rapidly reduced flow, preventing water hammering.
- Low operational costs
- Minimal wear over time
Disadvantages of non-slam check valves
- The non-slam check valves cannot be used in areas where line cleaning or maintenance requires line pigging.
Conclusion:
In short, we can conclude that the check valves, or non-return valves (NRVs), are essential for every fluid system to prevent backflow. Swing Check Valves are suitable for low-risk applications; they offer low resistance and positive sealing, but they cannot be used in pulsating flows. Tilting Disk Check Valves are quick closing type and are efficient for large-diameter systems.
The disadvantage of using these valves is that they can suffer seat tightness at low-pressure differentials. Wafer Check Valves are compact and cost-effective with low-pressure loss. However, these check valves are not designed for pulsating flows. Dual-plate wafer Check Valves close quickly and are suitable for high flow rates but with a higher pressure drop.
These check valves cannot be used for low flow rates. Spring-loaded Check Valves are versatile, effective, and pricier, often used in low-risk applications. Piston Check Valves are durable and versatile. They maintain pressure with low-pressure drops but can face water hammer problems.
Ball-check valves are compact and reliable but may slam at high pressures. Non-Slam Check Valves prevent pressure surges and water hammer, offering soft, quick closing and reduced operational costs. They are not suitable for line cleaning with pigging. Selecting the correct check valve depends on factors like fluid type, flow, pressure, and system needs, each type having specific advantages and disadvantages for safe fluid system operation.