This article describes the pre-commissioning checklist of the control valve. The control valve pre-commissioning checklist includes installation, inspection, testing, and taking valve online operation. If done carefully, the pre-commissioning activities save a lot of time during the main commissioning phase.
Pre-commissioning includes the following activities.
- Checking of equipment
- Cleaning of valve
- Leakage detection tests
- Cold testing
- Valve calibration
Main Objectives of Pre-Commissioning
- To develop a pre-commissioning checklist for a uniform verification system, documentation, testing, inspection, quality assurance, and operation preparation.
- Checking the functional operation of control valves to ensure that the control valves or system are ready for operation without hurdles at the time of commissioning.
- Review and study the maintenance manual for better know-how about the control valves. In case of any doubt, the manufacturer may be contacted for clarification.
Control Valves Pre-Commissioning Checklist
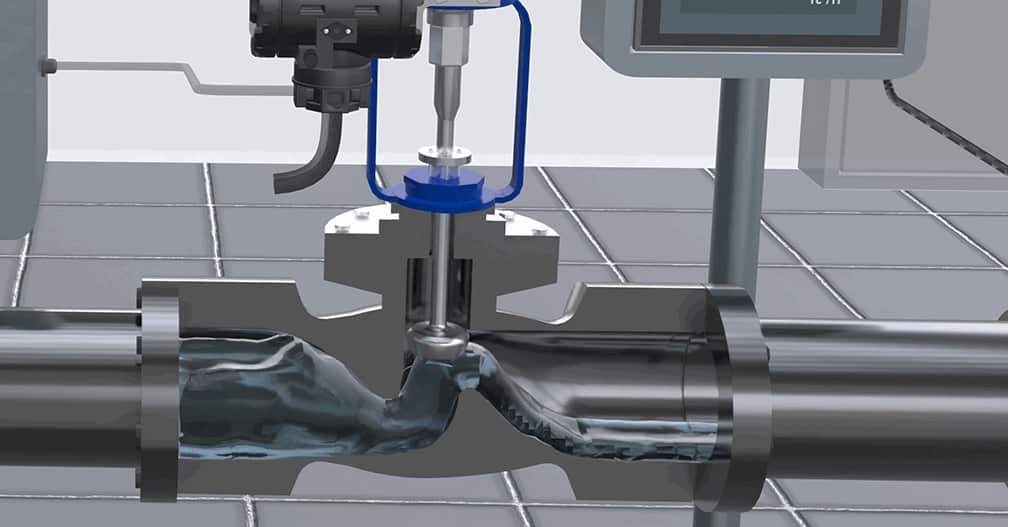
Before control valve commissioning, the below checklist provides a basic overview of pre-commissioning of the control valve.
- Refer drawing and ensure the field location of a valve
- Verify the specifications of the control valve as per the manufacturer’s datasheet.
- Isolation for control valves is also to be checked.
- Check the calibration certificate provided by the manufacturer and also ensure traceability certificates of master equipment.
- The flow direction data is available on the control valve. Verify control valve flow direction.
- Refer to the drawing and ensure proper installation of all tubing, fittings, solenoid valve, and other control valve accessories,
- The positioner is very important for the reliable functioning of the control valve. The control valve must sit in its position for open and close operation. Verify positioner operation by operating the valve for opening and closing. Also, verify the solenoid wiring for correct open-close operation.
- The instrument loop diagram provides a crystal clear picture of the instrument connected with the system. Ensure wire polarity and color as per the specified loop drawing.
- The solenoid valve operates the actuator, which closes or opens the control valve. The actuator must function properly to open and close the control valve. The improper installation of the actuator and over-stressed piping cause stress on the system, and the control valve may not function properly. Ensure all these during the installation stage,
- Ensure actuator rotation is indexed correctly with valve rotation for the rotary valve.
- The water must not enter the control valve for its reliable operation. The water may cause the failure of seals. Therefore, ensure and verify the installation of bug screens or other means of water ingress for all vented valve openings.
- Verify all ancillary equipment used for control valve operation functions appropriately. The compressor supplying control air to the valve must function correctly.
- Verify remote control valve operation through PLC/DCS as per process PID.
- Ensure accessibility for adequate space and platform for routine maintenance of actuator, plug, hand wheel, positioner, and solenoid valve.
- Proper support to the control valve, actuator, and other valve accessories.
- Ensure correct valve packing for application.
- Check the proper tightness of the packing gland.
- Ensure all the mounting parts of the valves are fixed properly. Verify tightness of all covers, screws, and fittings,
- Ensure proper and correct operation of the handwheel.
- The compressor air supply may not be available during the construction stage of the plant. Use dry and clean air or nitrogen for valve stroke check,
- Check the valve action through the valve controller by increasing the air signal and then again check the valve action by decreasing the air signal.
- Check the forward movement of the control valve in increasing the valve stroke from 0 % to 100 % in the steps of 0%, 25%, 50%, 75%, and 100% and the backward movement of the control valve in the steps of 75%, 50%, 25%, 0%.
- The valve stroke must be within a specified time. In the case of an emergency, the valve should close or open within the specified time.
- Valve open and close status may be recorded, and its indication may be checked in the central control room. The open/close information through PLC is taken at the remote station.
- The valve open/close position of the control valve must change on the graphic page on the SCADA.
- Also, on the alarm page, the control valve open/close position and descriptions like 5CV25 Valve open and 5CV25 Valve Close must be available.
- From the control valve controller, auto/manual operation of the control valve must be checked.
- The fail-safe action of the control valve must be checked. In two conditions- The electrical supply fails, and the control air supply fails.
Hello
I have a problem with the valve that does not follow the control value, the valve without flow is working fine, where is the problem please.
If the diaphragm of the actuator is have sharpe cut, leads to leakage while there is flow in the process line. It require some extra force during it’s function, than without pressure in process line.