Common terms used in control valves are very important for understanding the functioning of the control valve. Many terminologies are used in control valves and some common terms are actuator, trim, bonnet, bench set, etc.
Now, we will discuss the various common terms and control valve terminology in brief for a better understanding of the functioning of the control valve.
Table of contents
- Common Terms Used in Control Valves
Common Terms Used in Control Valves
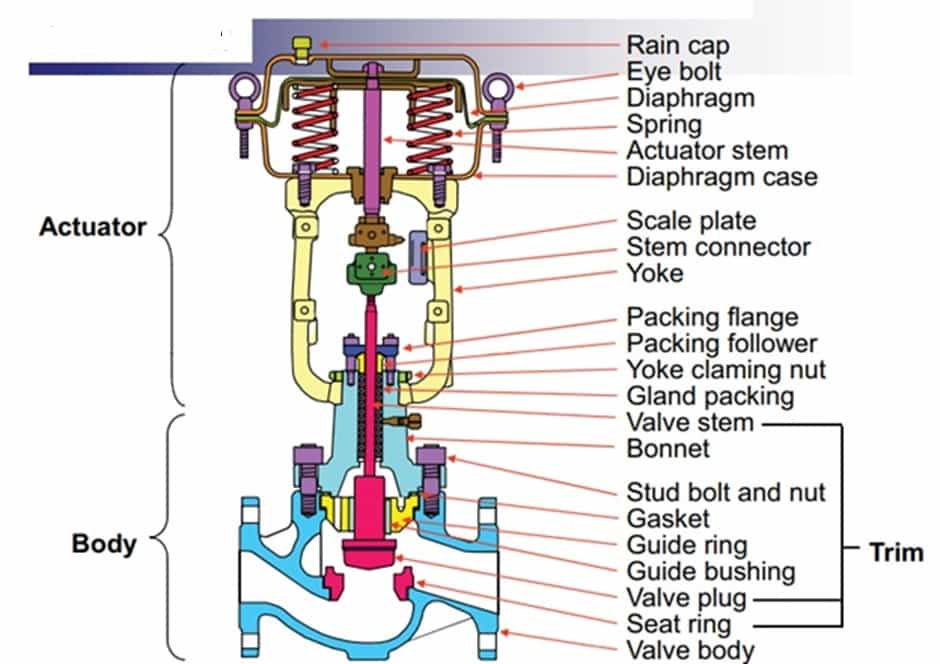
Actuator
An actuator is a part of a control valve that helps it to achieve physical displacement by converting pneumatic, hydraulic, or electrical energy into mechanical force. In simple words, the actuator of the control valve is the component of the valve that enables movement.
Bench-set
Bench-set is one of the important terminologies for the control valve. It develops the seating force of the plug against the seat during the fully closing of the control valve.
Proper seating stress is the most critical for the tight shutdown. On the other hand, Improper seating may have safety consequences.
Flow Coefficient, Cv
In the pneumatic industry, Cv is one standard that expresses the flow capacity of the control valve. Flow coefficient capacity Cv is very useful for calculating the size of the valve and fluid flow rate.
Valve Trim
Valve Trim consists of Internal Parts of the control valve that come into contact with Process Fluid and are apt to be worn. The Valve Trim includes Seat, Disc, Stem, Bushing, and others. There are various designs of the valve trim. Some of them are ;
(a) Anti-cavitation trim :
Cavitation causes serious damage to valves, system components, and nearby pipes. In water application, the control valves with anti-cavitation trim have the capability to overcome the problem of cavitation damage. Therefore, the valve used for the fluid which may cause cavitation, the valve trim materials must be selected accordingly.
(b) Anti-Noise trim :
A proper design of valve trim reduces the noise. There are two methods of noise reduction – Path treatment & source treatment. The Common source treatments include the proper design of noise-attenuation control valve trims. Therefore, the valve design must be done keeping the noise factor of the control valve into consideration.
(c) Balanced trim :
Control valve trim is designed in such a way as to minimize the net static and dynamic fluid flow forces acting on the trim.
(d) Reduced trim
Valve trim has a flow area smaller than the full capacity area of the valve.
(e) Soft-seated trim :
Valve trim made with the material like-
- Elastomeric
- Readily deformable material
Valve trim made of the above material provides a tight shutoff of the seat with minimal actuator force.
(f) Characterized Trim
The control valve trim provides predefined control valve flow characteristics.
(g) Erosion Resistant Trim
The valve trim is designed with special surface materials and geometry to prevent the erosion of control valve trim against the effects of the controlled fluid flow.
Control Valve
The control valve controls the flow rate of the liquid by controlling the flow passage as per the signal received from the controller.
Closure member
The closure member is a movable part that modifies the rate of flow through the control valve.
Control Valve Failure Mode
Whether a control valve closes or opens on losses of motive power is a very important design criterion.
(a) Fail-Closed :
In the fail-closed mode of operation, the closure member moved to the closed position on power source failure.
(b) Fail-Open :
In the fail-open mode of operation, the closure member moved to an open position on power source failure.
(c) Fail-in Place :
In the fail-in place mode of operation, the closure member stays at its last position on power source failure.
(d) Fail-Safe
Emergencies when loss of power triggers the actuator and move the valve into a predetermined safe position without the need for human control. It provides the safe and fast valve closure or valve fully open or remains in the last fixed position.
Vena Contracta
Vena Contracta is the section in the fluid stream where the cross-section of the stream became minimum. At vena contracta,
- The velocity of fluid is maximum
- The pressure of fluid is minimum
The vena contracta normally occurs in the control valve just downstream of the actual physical restriction.
Throttling
Throttling of the control valve regulates fluid by controlling the position of the closure member. It generates variable pressure across the control valve. Thus, by throttling of control valve flow, we can regulate the flow and pressure.
Travel Indicator
Travel indicator shows the position of control valve opening in terms of the following.
- Opening percentage
- Degree of rotation
Valve Travel
This terminology shows the movement of the closure member from the closed position to an intermediate or rated full open position.
Valve Seat
The valve seat is the area of contact between the closure component and its countermating surface which establishes valve shut off. Therefore, the valve seat is very important for fully closing of the control valve.
Seat Leakage
Ideally, the control valve should not pass fluid through it when the valve is fully closed. However, some fluid may leak from the valve. The quantity of fluid leakage when the valve is in the closed position is called seat leakage.
Seat Leakage Class
This is a classification established by ANSI B16.104 to categorize leakage tolerance for different sizes of control valve trims.
Hysteresis
The maximum difference between output and input value during calibration is called Hysteresis.
Valve Positioner
A valve positioner is a device that preciously adjusts the position of the valve actuator based on a control signal.
There are the following types of the positioner.
(a) Single Acting Positioner
Single action is a control valve that is driven by the air output of the control valve positioner on one side. While the other side is moved with the help of a spring or a membrane.
(b) Double Acting Positioner
Double action is a control valve that is driven by the output air of the control valve positioner on both sides (sides open and close).
Valve Packing
Valve packing is a component in a control valve that forms a pressure seal between the inside of the valve and the outside of the valve to avoid the process of fluid leaking out. Therefore, the proper valve packing is a must for ensuring the reliable operation of the control valve.
Read Next :