Control Valve Cavitation is the rapid creation and subsequent collapse of air bubbles in a fluid.
When the internal pressure in a pipe that carries water begins to fall below atmospheric pressure, then a vacuum develops. With pressure drops, the vacuum increases, although the water remains liquid. It is from a certain vacuum value when the water changes state and transforms into steam.
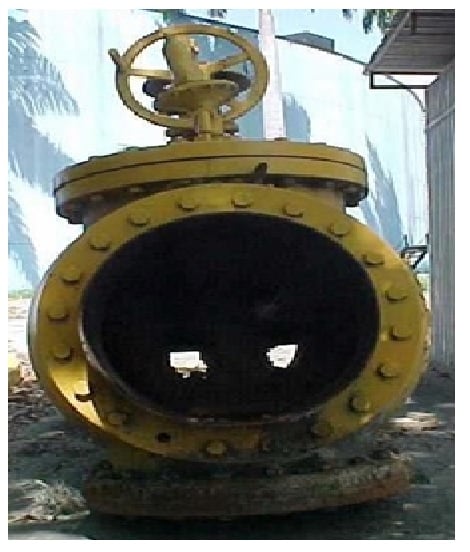
Cavitation Phenomenon in Control Valve
A liquid can become vapor due to two circumstances, either because its temperature increases or because its pressure decreases. In the case of water, and for a temperature above 24ºC, is considered the average temperature of the water in the pumps.
When the water turns to steam, it releases dissolved gases. As a result, this process forms the bubbles called cavities. Thus, the phenomenon of traveling bubbles with the liquid stream, and again gaining the pressure downstream explode with violence. This phenomenon is called cavitation.
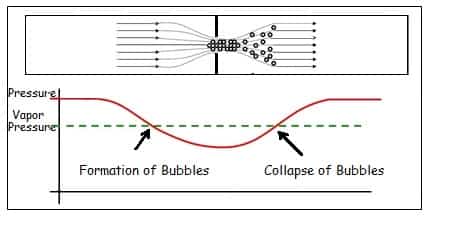
If, for example, a control valve in a pipeline operates with a small opening and a high flow rate, it causes a high-pressure loss due to the friction of the liquid stream with the valve plug. At the same time, there is a notable increase in fluid velocity, a direct consequence of the decrease in the passage area since:
Where “Q” is the flow through the constriction, “A” is its cross-section and “V” is the speed of the fluid. According to the Venturi effect, the speed of the fluid increases by decreasing the section area.
Q = A V
This increase in speed brings a decrease in pressure. If this pressure drop below the vapor pressure of the fluid, it creates steam bubbles, and then cavitation happens.
These steam bubbles travel with the current to areas where the pressure increases again because the section becomes larger. This actually occurs in a very small space. Thereby causing their violent implosion of them. If the bubbles explode in the vicinity of the diaphragm or the walls of the valve or the pipe, they can cause significant damage. At the same time also generates noise and vibrations in the installation.
Speed & Pressure Drop in Control Valve
In the following diagram, we can visualize the increase in the speed and pressure drop.
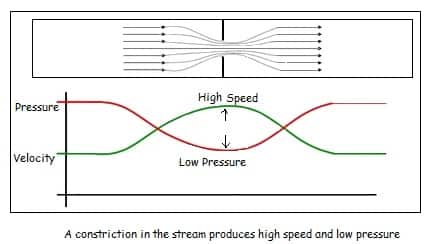
Clearly, the issue of cavitation is of no importance when it comes to opening and closing valves. There will be no problem with cavitation as long as we fully valve & fully close the valve. However, it can become a basic issue when it comes to regulating valves. Cavitation in control valves is evident if they work with high-pressure reductions and high flow rates.
Valve manufacturers usually give detailed information on the risks of cavitation according to the conditions of use of the valve. Taking into account the upstream and downstream pressure differential cavitation damage zone is provided by the manufacturer.
Noise emission
When a control valve works under cavitation conditions, the noise emission increases considerably. The increased noise depends on the pressure drop and design of the valve.
Operation under the effect of cavitation
If cavitation is unavoidable, what can be done is to take measures that help reduce wear (for example, squeeze the seat and cone plug of globe valves or reduce the diameter of the seat). On the other hand, as the damage caused is the immediate effect of the bubbles imploding inside the valve, it will also be reasonable to separate the cavitation zone from the control valve.