What is Starting Torque of a DC Motor?
The starting torque of a DC motor is the maximum torque that a motor can deliver to the mechanical load for its rotation.
A DC motor is capable of delivering high starting torque, and the motor is suitable for driving high starting torque motor applications like a rotary kiln, which demands high starting torque at the time of starting.
The DC motor is capable of producing 6 times more torque than its rated torque at the time of starting the motor.
If the load demands higher torque than the motor’s capacity, the motor will stall and trip on overload. This condition is called stall torque, where the speed = 0 and the motor can no longer rotate the load.
Torque Equation of DC Motor
The torque of the DC motor depends on:
- Field flux (Φ)
- Armature current (Ia)
Torque formula:
T = K × Φ × Ia
Where:
- T = Torque
- Φ = Flux
- Ia = Armature current
In a separately excited motor, the flux is constant. Hence, the torque depends only on the armature current.
The armature current of the DC motor is very high when the motor starts. The separately excited DC motor circuit diagram is given below.
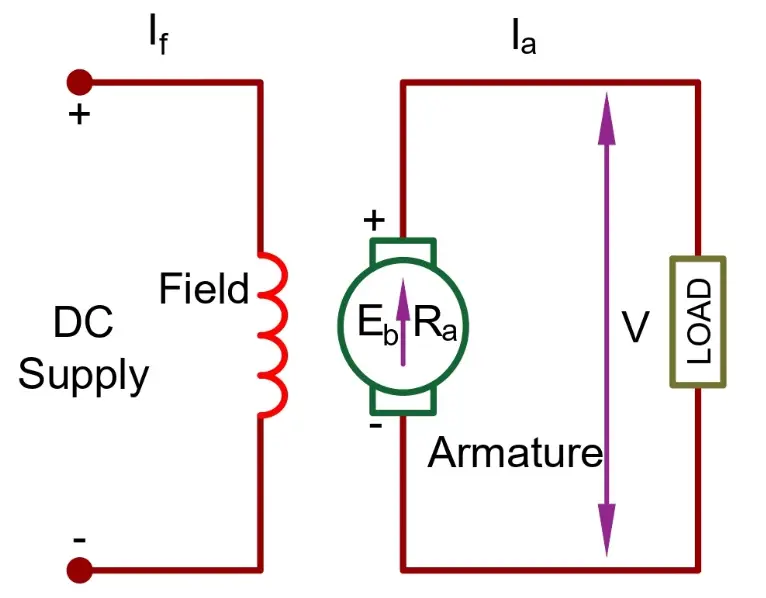
For Detailed Explanation- Read: Torque Equation of DC Motor- Its Derivation
Back EMF and Starting Current
The back emf induced in the armature can be expressed as;
Eb = V – Ia × Ra
Ia = (V – Eb) / Ra
When DC voltage is first applied:
- The back EMF (Eb) = 0
- This causes the motor to draw very high current initially.
Back EMF Formula in DC Motor
Back EMF depends on the motor speed and field flux. The formula is:
Eb = ΦNZ / 60 × (P/A) ——(1)
Where,
Eb = Back EMF induced in the armature
Φ = Main field Flux (Wb/m²)
N = Speed of the motor (RPM)
High Armature Current at Start
The torque produced by the DC motor is expressed by the following mathematical expression.
T = K × Φ × Ia ———(2)
At the start, the back EMF is zero; as a result, the armature current is 5 to 6 times the motor-rated full load current. Therefore, the DC motor starting torque is very high.
That is why the armature voltage is increased gradually or motor starter is used to limit the armature current to its safe operating range.
Read in detail : Necessity of Starter in DC Motor
Starting torque of DC Series motor
Why DC Series Motor Has High Starting Torque
The starting torque of the DC series motor is higher than the starting torque of the separately excited DC motor. The motor is used for the traction system. It is often chosen when the application demands a motor with high starting torque.
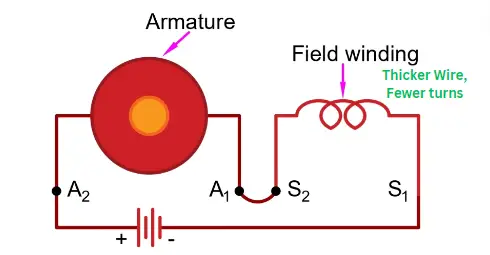
In the DC series motor, the field winding is connected in series with the armature winding. As the armature current flows through the field winding, the flux produced in the motor is very high.
T = K × Φ × Ia
Since Φ ∝ Ia,
T = K × Ia²
Read in detail why DC series motors have high starting torque.
Torque vs Armature Current
This equation explains the steep curve observed in the torque vs armature current graph of a DC series motor.
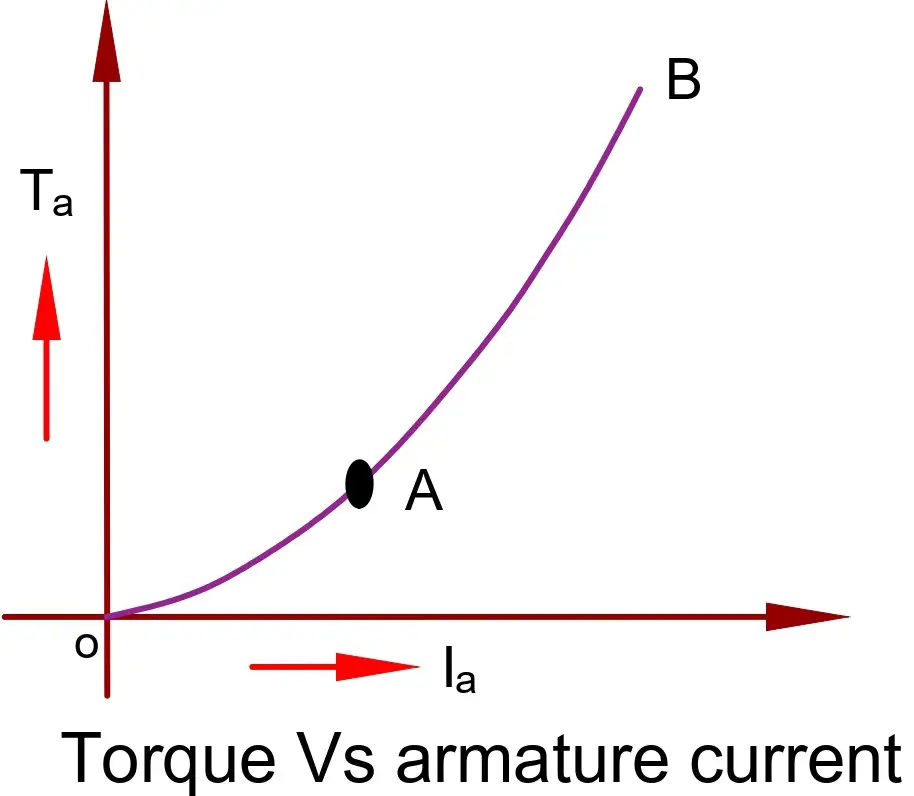
The torque of the DC series motor is proportional to the square of the armature current. That is why the DC series motor has high starting torque.
The DC series motor delivers the highest starting torque among all types of DC motors — significantly more than that of separately excited or shunt DC motors.
Applications That Require High Starting Torque
The DC series motor is used for driving high inertia loads, which demand higher starting torque. Examples of high-starting torque motor applications are:
- Rotary kilns
- Bucket elevators
- Railway traction
Contrary to the DC series motor, the starting torque of the DC shunt motor increases linearly with the armature current
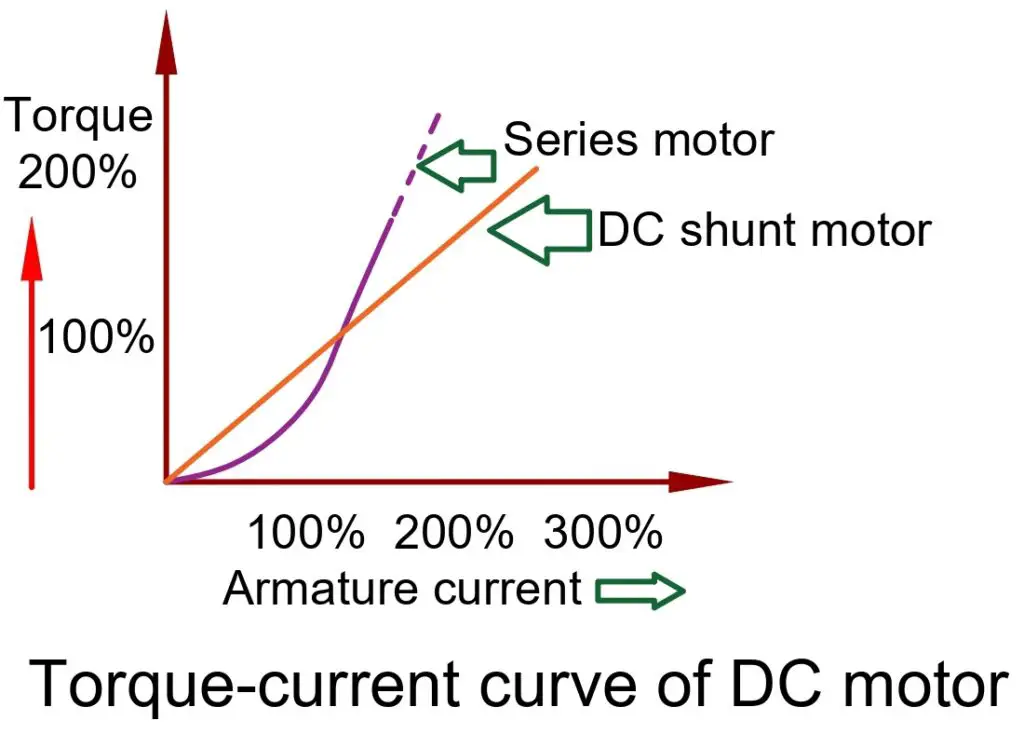
The DC motor can deliver the highest torque among all types of DC motors; however, the speed regulation of the DC series motor is poor. In the application where good speed regulation is required, the DC shunt motor or separately excited DC shunt motor is preferred.
One more thing about the DC series motor is that it should never be started at no load. The motor can attain an enormously high speed if run on no load. The field current is less when the motor is operated at no load. The speed detection system can be used to detect the over-speed of the motor, and the over-speed detection signal can be used to trip the DC drive.— learn more about why DC series motors should not be started at no load.
Starting Torque of DC Shunt motor
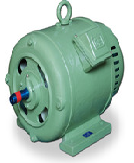
The DC shunt motor has field and armature winding. The field winding is connected in parallel to the armature winding. That is why the motor is called a DC shunt motor. The voltage across both windings is the same.
The connection of the field and armature winding is shown below.
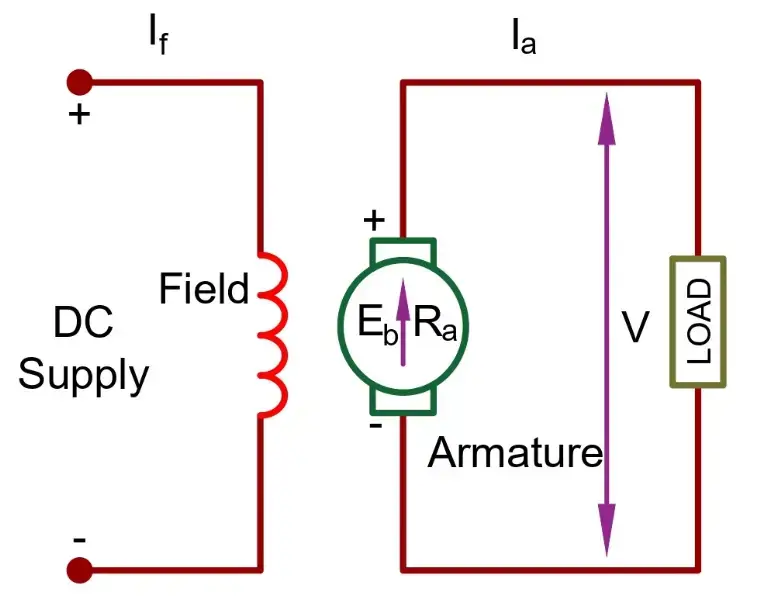
The DC shunt motor is best suited for applications where speed regulation is required. The starting torque of the DC shunt motor is less compared to the starting torque of the DC series motor. The flux in the motor remains constant, and the motor delivers the constant torque.
The torque of the DC Motor is proportional to the field flux and the armature current. In the DC shunt motor, the flux is constant; therefore, the torque is proportional to the armature current.
T = K × Φ × Ia
T = K × Ia (Φ = Constant)
The armature current and torque graph of the DC shunt motor is given below.
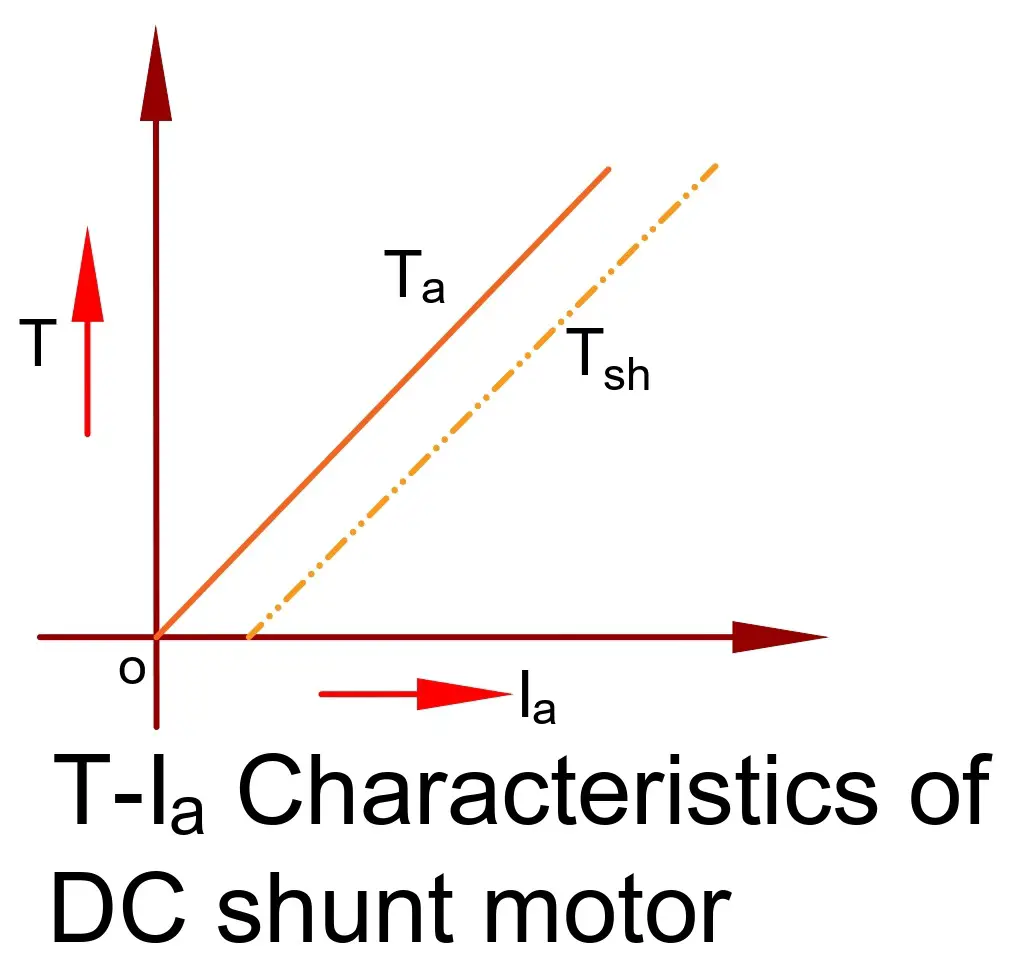
DC Series Motor vs Shunt Motor Starting Torque
- The starting torque of a DC series motor is higher than that of separately excited or shunt DC motors.
- Shunt and separately excited DC motors are ideal for applications needing good speed regulation.
Related Articles:
- Necessity of Starter in DC Motor
- Difference between AC and DC Motor
- Types of Braking in a DC Motor
- Types of DC Motors – Series, Shunt and Compound Wound
- What is Plugging or Reverse Current Braking of DC Motor?
- What is Shaft Torque of DC Motor?- Definition, Formula
- Direction of Rotation of DC Motor
- Working or Operating Principle of DC Motor
- Torque Equation of DC Motor- Its Derivation
- Condition for Maximum Power of DC Motor
- Back EMF and its Significance in DC Motor
- Commutation in DC Motor
- How to Change the Direction of Rotation of DC Series Motor?