The necessity of a starter in a DC motor is crucial because it controls high inrush currents, ensures smooth acceleration, protects against damage, enables automation, and enhances energy efficiency.
DC motors are widely used in industrial and commercial applications due to their controllability, reliability, and efficiency. However, starting a DC motor without a starter can lead to several operational challenges and potential damages. This article describes the critical necessity of starters in DC motors, detailing their functions and protection.
There is a necessity of starter in a DC motor for the following reasons.
Reasons for Use of Starter in DC Motor
1. High Initial Current (Inrush Current) Control
One of the primary reasons for using a starter with a DC motor is to manage the high inrush current that occurs during startup. When a DC motor is initially powered on, it draws a current several times higher than its rated operating current. This occurs because:
- Low Armature Resistance: At startup, the armature resistance is very low, leading to a surge in current. The resistance increases after running the motor because it increases with the increase in motor temperature.
- Absence of Back EMF: The motor has not yet started to generate back electromotive force (EMF), which normally opposes the supply voltage and limits current. The back EMF develops when the motor starts rotating and is zero when the motor is at a standstill.
Mathematically, the armature current is expressed as,
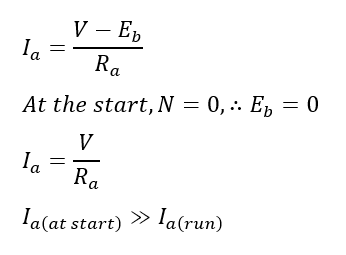
The above clearly shows that the DC motor draws a high starting current. To limit the starting high current, the starter adds resistance in the series of the armature resistance to limit the starting current.
This high inrush current can cause several issues:
- Electrical Stress: Excessive current can lead to overheating and potential damage to the motor windings.
- Power Supply Fluctuations: A high initial current can cause voltage drops in the power supply network, affecting other connected devices.
- Increased Wear: The sudden torque can cause mechanical stress on the motor and associated machinery.
Starters limit the inrush current by gradually increasing the current supplied to the motor, ensuring a smoother startup and reducing the risk of damage.
2. Controlled Acceleration
Directly starting a DC motor can result in rapid acceleration, which may not be desirable for several reasons:
- Mechanical Stress: Sudden acceleration can cause mechanical shock to the motor and the load it drives, leading to wear and tear or mechanical failure.
- Safety Concerns: Rapid, uncontrolled acceleration in machinery can pose significant safety risks to operators and nearby personnel.
Starters allow for controlled acceleration by incrementally increasing the voltage or current supplied to the motor. This controlled ramp-up ensures the motor reaches its operating speed gradually, minimizing mechanical stress and enhancing safety.
3. Motor Protection
Motor starters often come equipped with various protective features that safeguard the motor during both startup and normal operation:
- Overcurrent Protection: Starters can detect and limit excessive current, preventing overheating and potential damage.
- Under-Voltage Protection: If the supply voltage falls below a critical level, the starter can disconnect the motor to prevent damage from under-voltage conditions.
- Thermal Protection: Many starters include thermal overload protection, which disconnects the motor if it overheats.
These protective mechanisms are crucial for maintaining the motor’s longevity and reliability, especially in demanding industrial environments.
4. Automation and Remote Control
Motors are started and stopped frequently in many industrial applications, sometimes under varying conditions. Manual control of each operation can be impractical and inefficient. Starters enable:
- Automated Control: Starters can be programmed to start and stop motors based on predefined conditions, such as time schedules, temperature, or load demands.
- Remote Operation: Modern starters often allow for remote control, facilitating motor operation from a central control system or a remote location.
This automation and remote control capability enhances operational efficiency, reduces the need for manual intervention, and improves overall process control.
5. Energy Efficiency
Modern electronic starter such as, thyristor drives for starting and speed control of the DC motor,, are designed to optimize energy usage. By precisely controlling the voltage and current supplied to the motor, these starters ensure that the motor operates at peak efficiency. This reduces energy consumption and lowers operational costs and environmental impact.
Conclusion
The necessity of starters in DC motors is highlighted by their ability to manage high inrush currents, provide controlled acceleration, protect the motor from various operational hazards, and facilitate automation and energy efficiency. Starters are essential for ensuring the safe, reliable, and efficient operation of DC motors in various applications. Understanding the specific requirements of your motor and application is key to selecting the appropriate starter, ultimately enhancing the performance and longevity of your DC motor system.