Pressure Gauge calibration is the procedure for comparison of measurement values of a unit under test with those of a more accurate calibrated standard gauge. The pressure gauge is one of the most basic field instruments to measure pressure.
The pressure gauge can be used to measure the pressure of any line, vessel, or tank. The pressure gauge is often not given importance in plants as we have already installed pressure transmitters in the same line. But the actual importance of the pressure gauge is realized when there will be a blackout in the plant or when the pressure transmitter will fail. Hence, it is recommended to calibrate the pressure gauge every time whenever the calibration is due or whenever the pressure gauge is having any issues.
In this article we will discuss the whole procedure of pressure gauge calibration in detail.
What are the requirements for pressure gauge calibration?
Some basic things are needed for the calibration of the pressure gauge. These things are mentioned below:
- Pressure gauge to be calibrated
- A pressure calibrator which can be a pressure pump or Scandura or a dead weight tester is needed as a Test and Calibration Instrument (TCI)
- A calibrated pressure gauge for reference
- Temporary tubing
- Standard tool bag
- Fittings
How to calibrate a pressure gauge?
For the calibration of a pressure gauge, a standard calibrated and certified TCI is required as mentioned above in the requirements section. Below arrangements can be made to calibrate a pressure gauge.
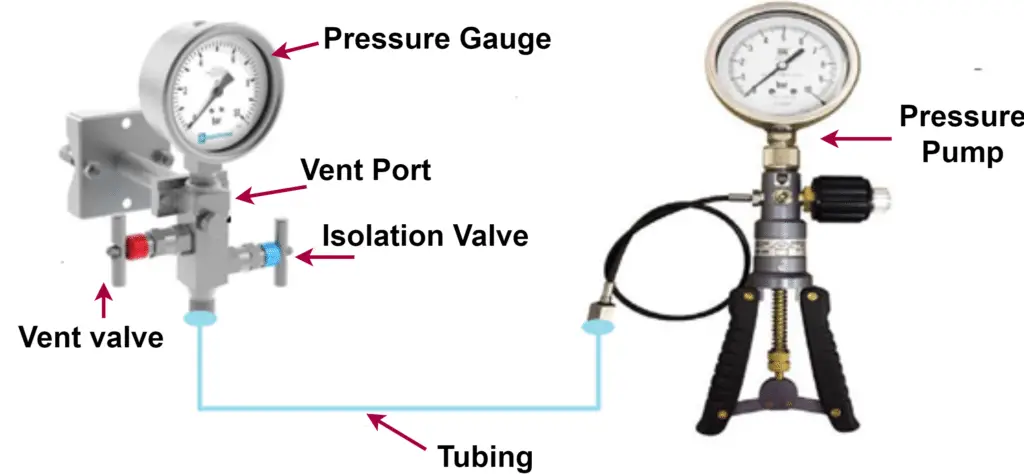
Before proceeding with the calibration of the pressure gauge let us clarify one concept of the manifold which is shown in the figure also.
The manifold of the pressure gauge has a vent valve, an isolation valve, and a vent port. Whenever the pressure gauge is in line, the isolation valve is in open condition, the vent valve is in closed condition and the vent port is also covered with a vent plug. This vent valve is also termed a bleed valve.
But mostly on the manifold, you will find vent written on it. So, whenever we want to vent the fluid inside the tube between the main line and the pressure gauge or between the isolation valve of the manifold and the pressure gauge, we will open this vent plug and open the vent valve. The purpose of the isolation valve is to isolate the pressure gauge from the main process line.
Steps for Calibration of the Pressure Gauge
Follow below mentioned steps to do the calibration of the pressure gauge:
Step 1
Arrange all the equipment as shown in the above figure.
Step 2
First, check the zero reading of the pressure gauge in the atmosphere. If the pressure gauge does not show zero, then try cleaning the manifold and the pressure gauge using instrument air. If still the zero of the pressure gauge is disturbed, then adjust the zero using the zero setting screw given on the pressure gauge. (Note: Most of the pressure gauge has zero setting screw on the display which can be accessed by removing the glass.) If the pressure gauge does not have a zero setting screw, then remove the pointer and set it to zero pressure.
Step 3
Now apply the maximum pressure as per the datasheet of the pressure gauge or the maximum pressure value as shown on the pressure gauge display. Apply the pressure using any pressure calibrator like a pressure pump, Scandura, or a deadweight tester. Check the value on the reference pressure gauge as well as on the pressure gauge under calibration.
If the readings match, then the pressure gauge is OK. If there is any mismatch between the values of both the pressure gauges, then set the span of the pressure gauge under calibration using the span setting screw (only a few pressure gauges have this span setting screw).
Step 4
Again after setting the span of the pressure gauge, check the zero of the pressure gauge. Set the zero of the pressure gauge if found disturbed and repeat the process of setting zero and span until both are found ok.
Step 5
Now check the values like 0%, 25%, 50%, 75%, and 100% in upscale as well as in downscale. Doing this will ensure that the pressure gauge’s linearity is ok or not. The linearity can be confirmed after plotting a graph of input vs. output