A Strain gauge is used for measuring the displacement, pressure, force, and torque. It converts the force and pressure into an electrical signal that can be measured, transmitted, and displayed at the remote station.
When pressure exerts on the elastic element, the element tends to deform. We can easily convert the deformation in the element into an electrical signal. It is possible to convert the deformation into an electrical signal by the following devices.
- Strain gauges
- Capacitive
- Piezoresistive
- Magnetic
- Resistive
- Piezoelectric
The strain gauges are suitable for almost all pressure measuring applications. On the other hand, magnetic, resistive, and piezoelectric are suitable for very specific applications.
In this article, we will discuss the strain gauge & its working principle.
What is a Strain Gauge?
Meters based on strain gauges consist of one or more loops of very fine conductive wires. The wires are glued on the elastic element (diaphragm) of the pressure sensor.
On application of the force, the diaphragm deforms. The conductive wire attached to the diaphragm stretches or contracts, and as a result, the length and diameter of the wire modify. Finally, the resistance of the conductive wires changes with a change in their dimensions. We use a resistance bridge circuit to convert the change in the resistance into voltage or current.
Strain Gauge Working Principle:
The resistance of conductor material is directly proportional to the length and inversely proportional to the cross-sectional area. The following depicts the relation.
R = ρ L/A
Where:
A: Resistance between terminals.
ρ: Specific resistivity of the material.
L: Length between the conductor terminals.
A: Cross-sectional area conductor material.
On stretching of a metallic conductor, its length increases (L3), and its cross-sectional area decrease transversal (A3). And, as a result, its electrical resistance increases.
On compression of a metallic conductor in its longitudinal direction, its length decreases (L1), and its cross-sectional area increases transversal (A1). And, as a result, its electrical resistance decreases.
The figure below shows the modifications in the dimensions of conductive wire with an application of force.

The variation of the cross-sectional area of conductive wire to the deformation of the diaphragm is very small. Therefore, the resistance variation is also very small, and as a result, the strain gauge has low sensitivity.
How to increase sensitivity of strain gauge?
We can increase the sensitivity of the strain gauge transducer with the grid configuration on the potentiometric gauges. The configuration is as shown in the below figure. This grid pattern of strain gauge maximizes the amount of wire or sheet metal with respect to tension in the direction parallel thereto.
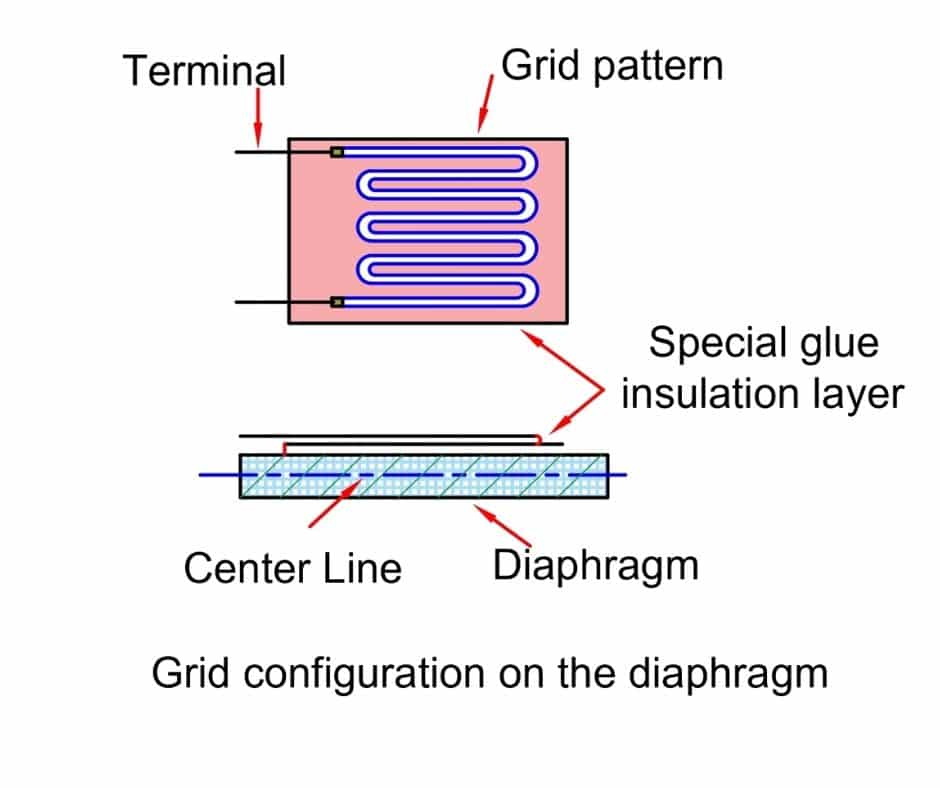
What is Gauge Factor?
Sensitivity is the fundamental parameter of the strain gauge. It is expressed as the gauge factor (GF). Gauge factor (GF) is defined as the quotient of the fractional change in electrical resistance to the fractional change in length (tension).
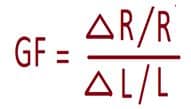
Where:
ΔR: Variation of electrical resistance.
R: Resistance.
ΔL: Difference in length.
L: Length.
The gauge factor (GF) in metallic strain gauges has typical values close to 2.
As explained above, the lead wires must be glued to the diaphragm as shown in the above figure. Adhesion between the gauge and the diaphragm is critical and found today one of the main disadvantages of this method.
Thermal compensation of Strain Gauge:
The differences between the coefficients of thermal expansion of the elements wrapped (diaphragm, glue, gauge insulation layer, and the gauge itself) cause temperature dependence of the output signal, Therefore, the measuring system has a thermal error.
Processing Unit of strain gauge?
Another important element in this type of meter is the processing circuit. This processing circuit amplifies the strain gauge signal which has a very low magnitude and delivers the amplified signal as an output signal.
To compensate for the effect of temperature on the measurement accuracy of resistive type transducer, the processing circuit must have a compensation circuit. A widely used configuration of the processing circuit is the Wheatstone bridge configuration, typical of resistive transducers.
Any change that occurs in the resistance of the active gauge will unbalance the bridge and will produce a voltage other than the bridge balance as shown in the figure below.
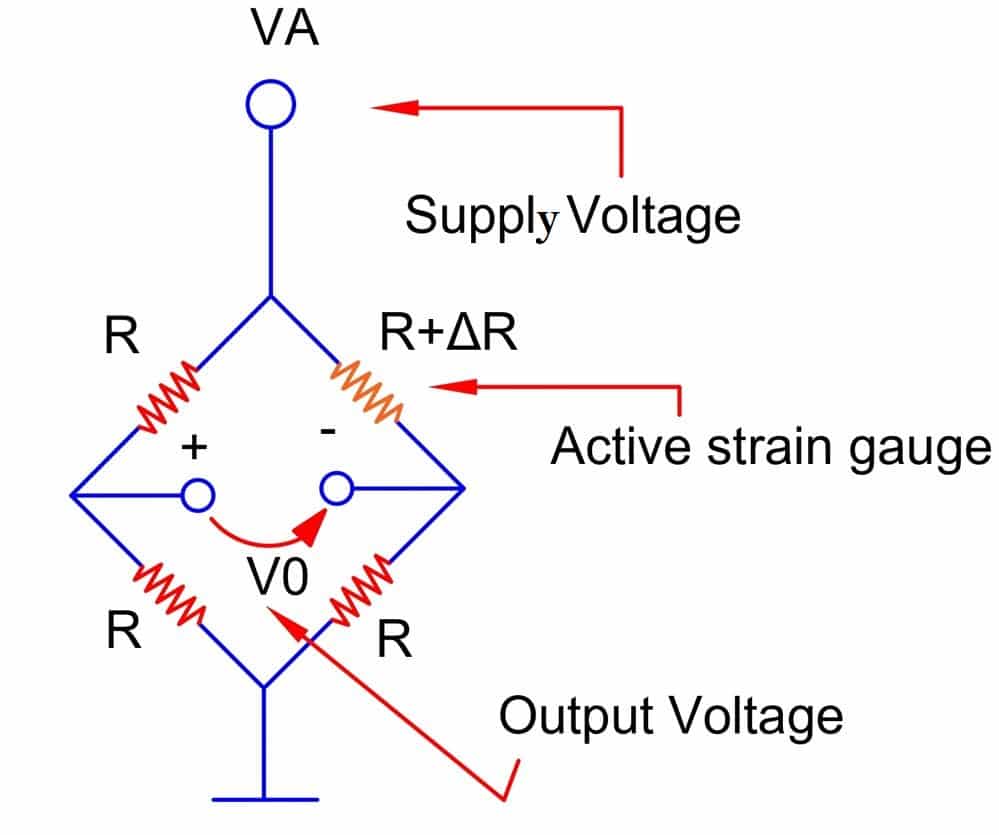
Temperature Compensation & Sensitivity Improvement of Strain Gauge Bridge
We do various modifications to the configuration of this bridge to implement offsets and sensitivity increases very simply.
If we use all four strain gauges as an active element, we can double the sensitivity. The condition is that two of the gauge must increase their resistance, and the other two gauges must decrease their resistance. By properly placing the gauges, the two gauges work in the stretching mode and the other two works in the compression mode on the application of the stress.
The below figure shows the configuration of this type of bridge.
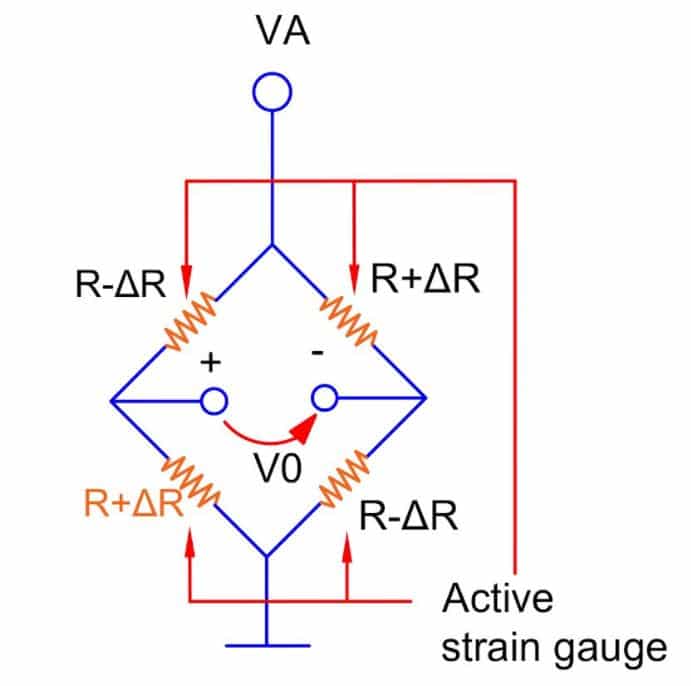
One way to perform thermal compensation on the same bridge is to place two Equal gauges at the top of the bridge. One of them is active, that is, it’s resistant to the change of pressure and the other is inactive because it is placed outside of the diaphragm, but very close to it.
In this way, the active gauge varies by the changes in pressure and temperature, and the idle gauge is only sensitive to temperature changes. Due to the bridge configuration itself, the output will be independent of temperature, shown in the below figure.
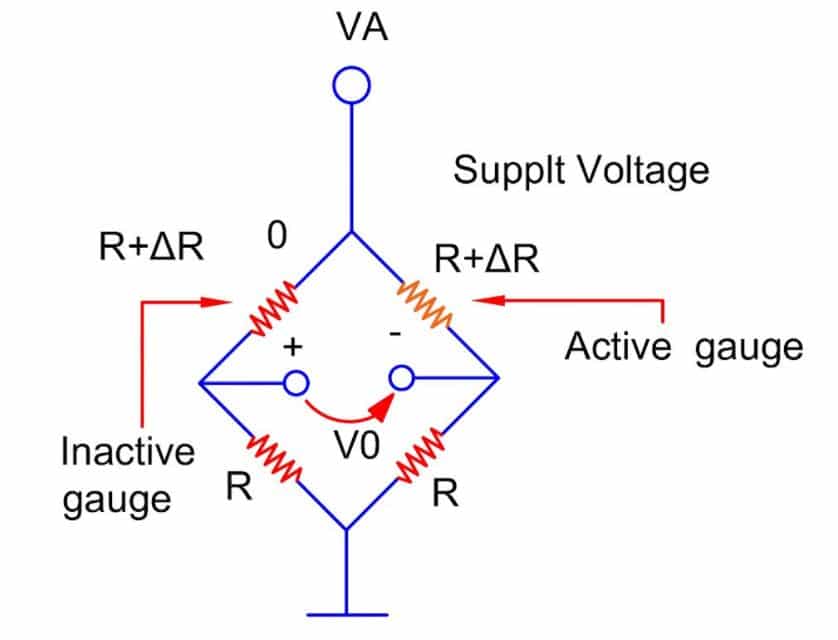
Advantages & Disadvantages of Strain Gauge
Advantages
- Those applications that are based on strain gauges have a temperature range of greater operation, which makes them more appropriate in some applications.
- Use the technology of microelectronics, which provides very low production costs.
Disadvantages
- The main disadvantage is the fact that the strain gauge has to be glued to the diaphragm.
- Another is its dependence on temperature applications.
- Taking into account the cost, which has a very important weight in the selection of the measuring instruments.
- These meters are more expensive as compared to capacitive and piezoresistive.
Read Next: