Interposing Relay system is the system used to isolate two different systems working on the different magnitudes of voltages. The different voltages can be 24 VDC, 110 VDC, 240 VDC or even more. Thus, isolation of two different systems is necessary. The necessity of isolation is because we need to avoid any kind of damage that can be caused to the system working on lower voltage from the system working on higher voltage.
The best example of this system is the hardwired communication between the Programmable Logic Controller and the Motor Control Centre.
Let us see some cases in which Interposing Relay can be used.
Case 1: Interposing Relay system
Suppose we want to operate a motor through a command from the PLC. PLC works on 24 VDC and the motor runs on 230 VAC. We can use a relay in this case. The relay should have a coil voltage rating of 24 VDC and a contact rating of 230 VAC. This way the PLC can operate the relay’s coil which in turn will change the contact.
The contact changeover will supply voltage to the motor. This way both the systems remain isolated from each other but still, the purpose of starting the motor is fulfilled. Direct contact between the PLC and the motor’s supply voltage will damage the PLC.
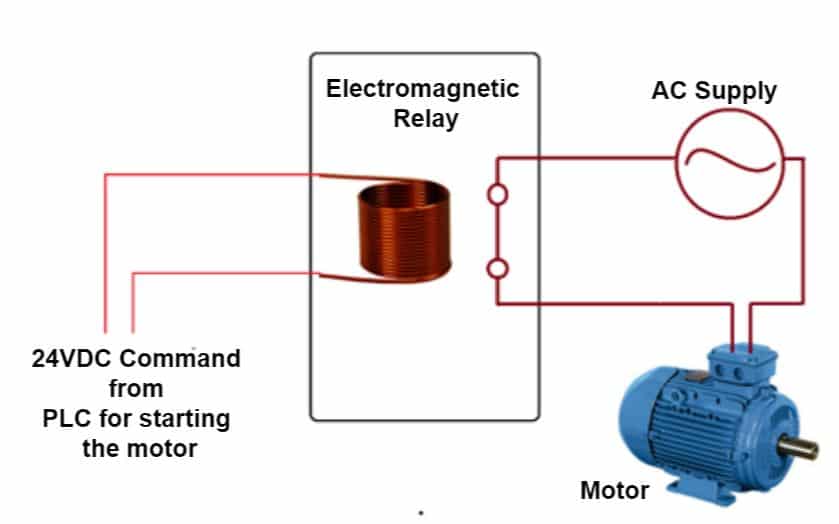
Case 2: Interposing Relay system
Consider there is a heater in the plant which operates at 110 VAC and at a much higher ampere rating. The heater starts and stops commands are to be controlled by the PLC. In this case, also a relay can be used which will physically isolate both the systems.
The coil will be energized from the PLC with a few volts and a few milliamperes. While the contact of the relay will be used to operate the heater based on the command issued to the coil. Any flow of voltage from the heater’s supply voltage to the PLC can lead to PLC damage.
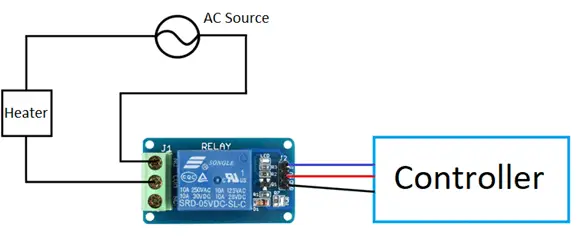
Interposing Relay System in a PLC
Thus, the relay is used to isolate the PLC and the higher-rated voltage supply. The relay will protect the PLC which is a delicate part of the control system.
The relays can also be used with circuits in which there are components working on different ratings. Suppose there is a vehicle’s headlight that is to be controlled by a toggle switch in a circuit. The vehicle’s headlight works on high power, while the circuit uses only 12 volts. Any short circuit between these two systems will totally damage the circuit.
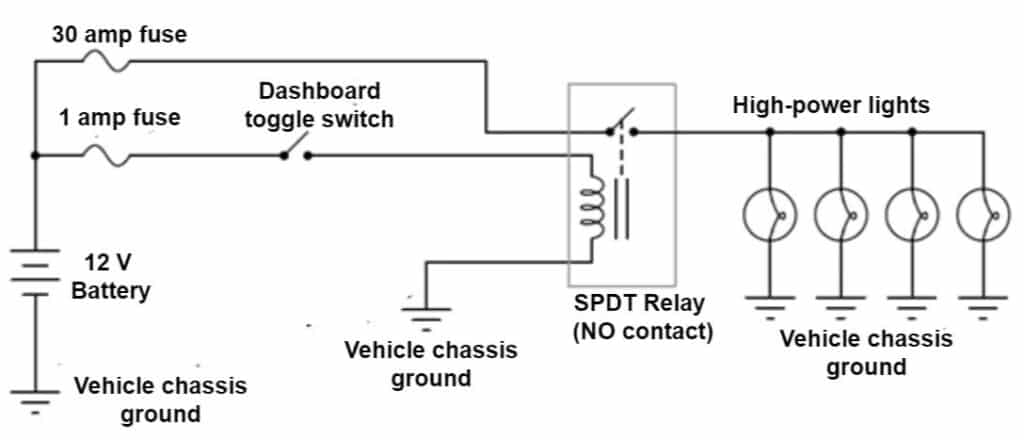
In the case of PLC also a variation is possible in which relays are extremely important. Some PLCs work on 110 VAC / 230 VAC. Now in this case how will we use the sensors which work on 24 VDC? Because sensors are generally working on 24 VDC. So here also we need to use relays to make communication between the high voltage rated PLC and low voltage rated sensors. A separate power supply of 24 VDC is given to the sensor as shown in the figure.
How does an Interposing Relay System Work?
When the sensor will sense the target and actuate, the 24 VDC will be supplied to the relay which will in turn change the contact. This contact changeover will be sensed by the PLC input. This way relay isolates the PLC working on 230 VAC and a sensor working on 24 VDC. The relay serves as an interposition relay between the PLC and the sensor working on different voltages. Hence, the relay is called Interposing Relay.
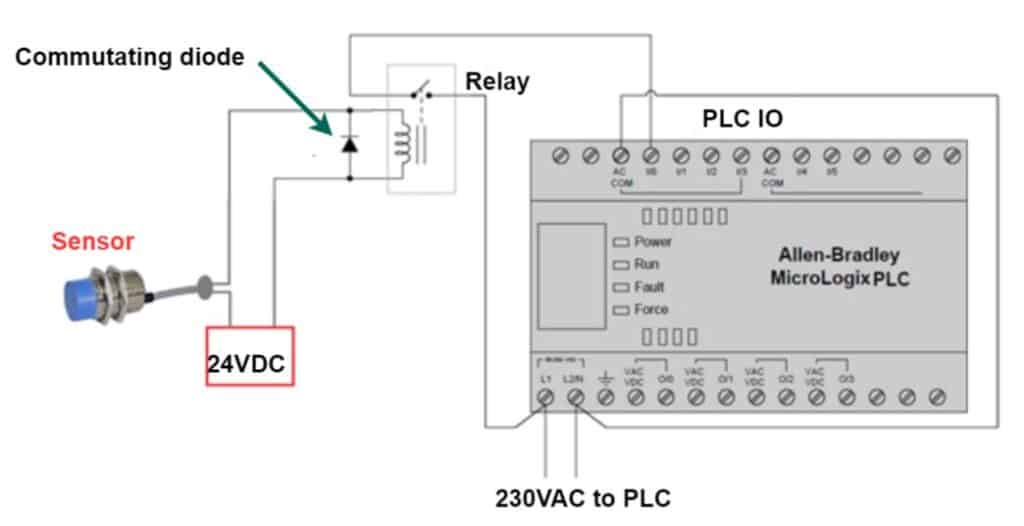
The commutating diode used in the circuit is used to protect the sensor. Without this diode in the circuit, the coil’s kickback voltage (hundreds of volts in some cases) will definitely destroy the proximity switch. Here the commutating diode is connected in backward with respect to the polarity of the 24 VDC power supply. This is done intentionally, as we don’t want the diode to conduct when the power supply is passed to the relay coil by the sensor.
Suppose if a diode is connected in the other way, then most of the current will pass through the diode itself. This will damage the sensor due to overcurrent flow. This diode will only turn on when the polarity of the power supply reverses. This will collapse the relay coil’s magnetic field.
Benefits of Interposing Relay
- Interposing relay saves one system when the system connected on the other side of the relay gets damaged. The damage can be due to a short circuit or earthing issue.
- Interposing relay controls the high voltage and high current rated machine to run from the command given by low voltage and low current rated PLC
- Interposing relay will also make communication between high voltage rated PLC and low voltage rated PLC.