Proportional control is a process control technology that responses in proportion to the difference between the set point(SP) value and current value of the process variable(PV). In proportional control the set point value is continuously monitored with the current process value and the difference between these two values generates an error signal e(t). The proportional controller does the proportional control action.
Proportional controller or commonly called P controller gives the output which is proportional to the error signal. The error signal is the difference between the set point and the current process value.
The proportional controller compares the set point with the actual value or feedback process value and generates an error signal. The resulting error is multiplied with a multiplication factor to get the output. The multiplication factor is called the Proportional Gain Factor (KP)of the proportional controller.
If the error value is zero, then the controller output is zero. The more the value of the proportional gain factor KP), the faster is the response of the control system. The lesser the value of the proportional gain factor, the slower is the response of the control system.
We all want a fast system for maintaining our control system. But the only problem we face by increasing the proportional gain factor (KP) is that the overshoots and undershoots in the system increases. Also, by decreasing the proportional gain factor (KP), the output of the control system becomes slow which is not acceptable for many systems.
Working of Proportional Control
Block diagram of proportional controller is given below,.
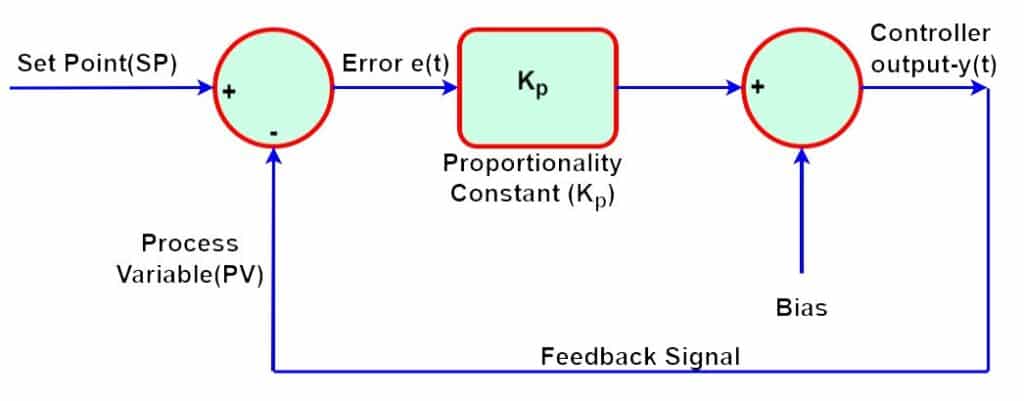
Mathematically, Proportional controller is defined by:
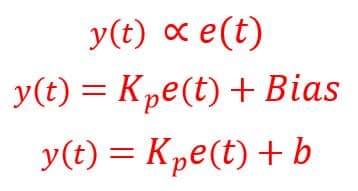
Where y(t) is the output of the proportional controller
KP is the Proportional Gain Factor
e(t) is the error between the set point and actual value
b is the bias signal
Bias is a constant term added to the output of the proportional controller. The reason for use of Bias value is very simple. As discussed, the output of the proportional controller is proportional to the error signal.
Assume that we are controlling the level of a tank by controlling a control valve. The input for the control valve opening is given using a proportional controller i.e. calculated error by using the tank level set point and the actual tank level.
Suppose tank level set point is 50%. Valve keeps on throttling till it makes the tank level as 50%. Now at this point of time, the error will be 0. So proportional controller’s output will also become 0. So again, tank’s level will be disturbed (increase or decrease as per design of the system). Hence for this reason we use a Bias. So, when the error signal goes to 0, at that time this Bias will be giving some command to the proportional controller.
One important thing to note here is that the proportional controller behaves as a On-Off controller when the proportional gain factor (KP) value is set to too high.
The proportional controller is suitable under following conditions.
- There should be no big difference between the set point and feedback or process variable value.
- The deviation should not be abrupt.
Transfer Function of the proportional controller
The proportional controller produces an output, which is proportional to error signal.
y(t) ∝ e(t)
⇒y(t) = KP e(t)
Apply Laplace transform on both the sides, we get
Y(s) = KPE(s)
Y(s)/E(s) =KP
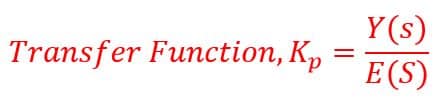
Therefore, the transfer function of the proportional controller is KP.
Where,
Y(s) is the Laplace transform of the actuating signal y(t)
E(s) is the Laplace transform of the error signal e(t)
KP is the proportionality constant
The block diagram of the unity negative feedback closed loop control system along
with the proportional controller is shown in below figure.
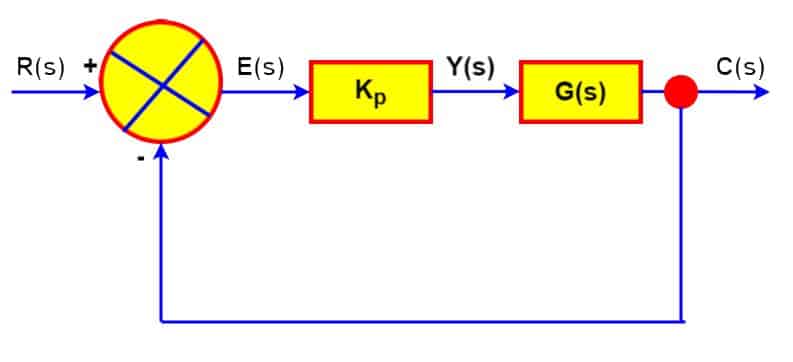
Advantages of Proportional Controller
The followings are the advantages of the proportional controller.
- The proportional controller reduces the steady-state error when the difference between set point and process variable decreases. Thus it improves the system stability.
- It is possible to improve the slow response of the overdamped system.
Disadvantages of Proportional Controller
The followings are the advantages of the proportional controller.
- The Proportional Controller produces steady state error. The special term used for this is the offset. This means that after some time, there will be a constant error between the input signal and the output signal. Proportional Controller cannot eliminate this error.
- Proportional controllers also causes overshoots and undershoots in the system.
Proportional Band of Proportional Control
Proportional band shows the percentage span change in input signal that causes hundred percent change in output signal.
For example, if the change in the output is 100 % with input signal span change of 100% ,then the proportional band is 100%. If the 40 % span change in the input signal cause 100% change in output, then the proportional band is 50%. Now, we can establish the relationship between proportional band and gain. The ratio of change in the output to input is called gain.
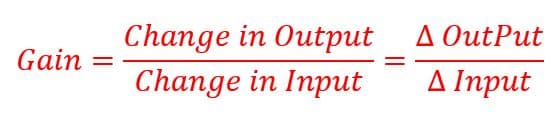
From above expression, it is clear that if output is equal to input, then the gain is 100%. Thus, PB is the reciprocal of gain, expressed as a percentage.
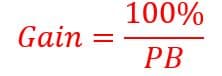
What is the gain of a controller for PB a) 60%, b)150%
Gain of the controller when PB is 60 %
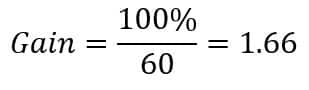
Gain of the controller when PB is 150 %
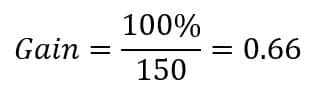
need an électronique diagram for température proportionnal control