Pneumatics is the technology that uses compressed air as a means of transmitting the energy necessary to move and operate mechanisms. Air is an elastic material and, therefore, when a force is applied to it, it compresses.
Pneumatic applications in the industry
Pneumatic energy has been used in industrial production processes for many years. As time goes by, pneumatic systems acquired greater prominence. A very clear example of this is robotics.
Nowadays, industrial pneumatics is widely used in different sectors. Pneumatic system is important for the manufacturing, automation, and processing industry (petrochemical, food, paper, etc.).
Some of the most representative pneumatic systems are double-diaphragm pneumatic pumps, refrigeration systems, industrial supplies, etc. Also, it is useful for automobiles, trains, aircraft brakes, or actuation of actuators.
What are the transmitters?
Transmitters are instruments that capture the process variable and transmit it remotely to a receiving instrument. It may be an indicator, a recorder, a controller, a control valve, or a combination of these.
In pneumatic instruments, air pressure is used as a signaling medium instead of electrical power. Let us take a pressure transmitter to illustrate further. A pressure transmitter gives an output that will be in the standard range to a pressure gauge calibrated accordingly.
Pneumatic System Pressure Range
The indicator is a special pressure gauge in the range of 3 psi to 15 psi. The signal 3 psi is the lower end of the process measurement scale, and 15 psi is the high side of the scale.
Generally, we do the transmitter calibration in the range of 0 to 300 PSI. The transmitter output of 3PSI represents that there is no pressure. A full process pressure of 300 PSI on the transmitter gives a 15 PSI output. The same indicates in the pressure gauge.
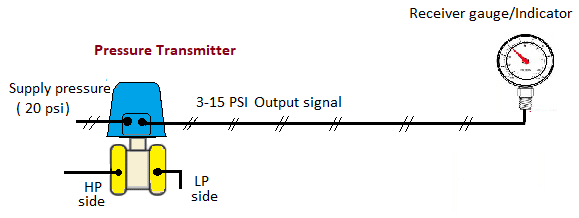
In other words, a 3 psi signal pressure represents 0% of the scale and a 15 psi signal pressure represents 100% of the scale. Pneumatic transmitters generate a linearly variable pneumatic signal from 3 to 15 psi (pounds per square inch) for the 0-100% variable measurement range.
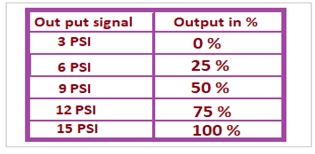
In countries that use the metric system, the pneumatic pressure is 0.2-1 kg/cm2 that is approximately equivalent to 3-15 psi (1 psi = 0.07 kg/cm2).
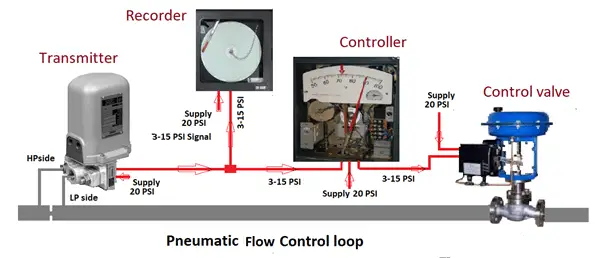
How to select a pneumatic system?
Through linear and rotary motion applications, the pneumatic system is the best substitute for electric actuators and motors.
It is generally suitable for smaller loads because pneumatic systems produce less force than hydraulic systems and because air is easy to compress, pneumatics can absorb excessive shock.
Pneumatics work in linear and rotary motion and is an easy way to activate an output motion or apply force. In selecting a pneumatic system for industrial applications, one must consider the requirements in terms of a sequence of operations.
When selecting a pneumatic system, one must consider the pressure and flow requirements for the best possible performance. The pneumatic system may not function properly on the selection of the wrong components.
Application example of pneumatics
It is possible to apply the pneumatic instrumentation from ordinary single loop indicating measurements to complicated loops such as cascade control as shown below figure.
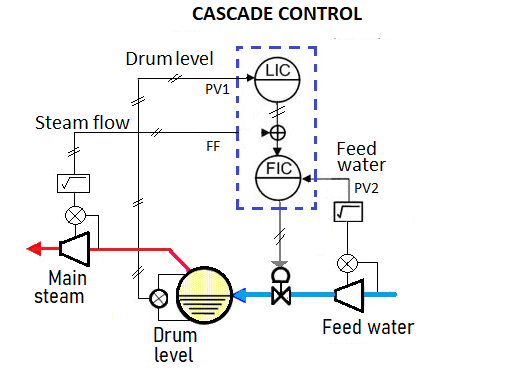
How do pneumatics and pneumatic systems work?
Industrial pneumatics is a simple and reliable way to get things moving, simply by using clean, dry air. Compressed air is the main input power to the pneumatic systems to generate mechanical power and motion. Further, the motion caused by the pneumatic system operates the factory automation systems. Pneumatics are also present in other applications, from trucks to medical applications and food preparation, through pneumatic tools and blow molding.
Precautions
- We must take care to monitor for air leaks and corrosion in pipelines to avoid breakdowns.
- The quality of the compressed air must be high enough to ensure efficient operation.
- Air preparation in pneumatics is essential. Therefore, there should be a removal system for moisture, unwanted dust particles, and oils. Otherwise, they can clog or corrode certain components such as valves and seals.
- The application of a filtration system and monitoring of the air supply will also ensure that the pneumatic system is working as it should.
Advantages of Pneumatics
- The elements that make up a pneumatic system are simple and easy to understand.
- Air in the atmosphere is abundant, that is, we can dispose of it in an unlimited way.
- The maintenance cost of pneumatic circuits is generally low.
- The pneumatic system is intrinsically safe and best suitable in explosive and hazardous atmospheres.
- It is easily transportable.
Disadvantages of Pneumatic system
- Pneumatic systems are sensitive to vibration. Therefore, system installation must be away from sources of vibration.
- Compared to other types of energy sources, it needs preparation before use (removal of impurities and moisture).
- It has limited working forces. (from 20 to 30,000 N).
- It is noisy, due to air leaks after use.
- It is expensive energy, which can be offset to a certain extent by good performance and ease of implementation.
- The pneumatic system occupies a huge space inside the panel with tubing, indicators, recorders, controllers, square root extractors, and air headers. On the other hand, panels with electronic instrumentation are not cumbersome, and easy to fix problems related to wiring.
Read Next:
I am interested in all especially instrumentation and automation
Kind regards