Hydraulic actuators are most suitable for applications that require a large amount of motive force for valve operation. On the other hand, the pneumatic valve requires less amount of motive force. It is most suitable for applications that require a fast and accurate operation.
Table of Contents
Working of Hydraulic Actuator System
The hydraulic actuator diagram is as shown below.
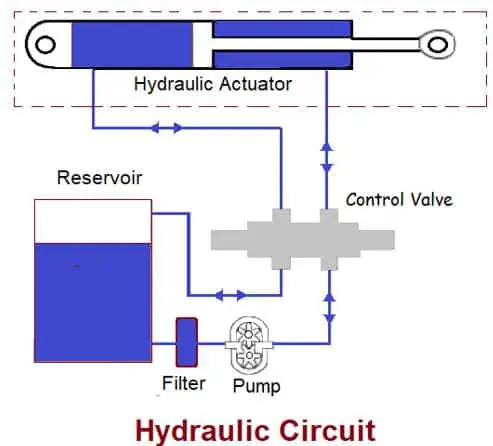
- Hydraulic systems use the pump to push the hydraulic fluid through the system to create hydraulic power.
- The control valve that directs the flow controls the cylinder movement. It is possible to operate the control valve by electrical or manual modes. The fluid line pressure allows the piston to raise and lower, as well as to stop the fluid flow.
- The hydraulic fluid can be water or liquid. The liquid is generally high-density incompressible oil.
- The hydraulic circuit system as shown below works in a similar way to electrical circuit theory, using linear and discrete elements.
Hydraulic means pressurized hydraulic fluid. Thus, any pressurized fluid that creates either linear or rotary motion is a hydraulic actuator. Basically, the hydraulic actuators are hydraulic cylinders.
Parts of Hydraulic Actuator
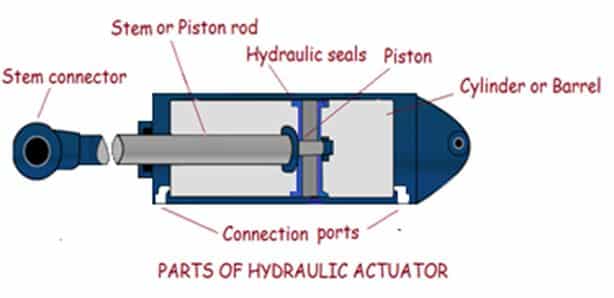
Hydraulic cylinders have various parts or various components in their internal construction. These are a barrel, hydraulic seal, a stem, a stem connector, a piston, and an inlet and outlet port.
Barrel or Hydraulic actuator Cylinder
This is the part of the actuator where the oil enters and leaves the hydraulic cylinders. When the oil enters through the Inlet Port it enters at strong or high pressures, then the barrel has to be very resistant, and that is one of the reasons why a Honed Tube is used.
Hydraulic Seals
Hydraulic seals block the passage of oil from one side of the Piston to the other of the hydraulic cylinders. In other words, they do not allow the oil that is entering to reach the outlet port. The oil is blocked or sealed in the part of the hydraulic cylinders where it has to be.
Stem
The stem is a Chrome Bar that allows the transmission of force generated by the oil inlet pressure in the hydraulic cylinders. The oil enters the Inlet Port and pushes the Piston, this makes the Rod pull out or the hydraulic cylinders with great force.
Piston
The inlet or outlet flow inside the barrel pushes the Piston or Plunger of hydraulic cylinders. When the Piston moves to either side of the cylinder, the Rod contracts or expands.
These are the parts of the basic hydraulic cylinders. There are more types of cylinders that are more complex in their construction. However, these components are essential to almost all hydraulic cylinders, and it is good to know what they are and how they work.
Types of Hydraulic Actuator
Single acting hydraulic cylinder:
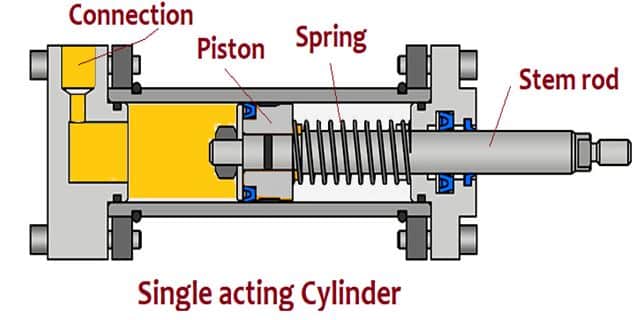
The linear movement is carried out in one direction by the action of the hydraulic pressure. The return movement can be mechanically by an internal spring returned with the external mechanical force when it stops having hydraulic pressure,
Double acting hydraulic cylinder
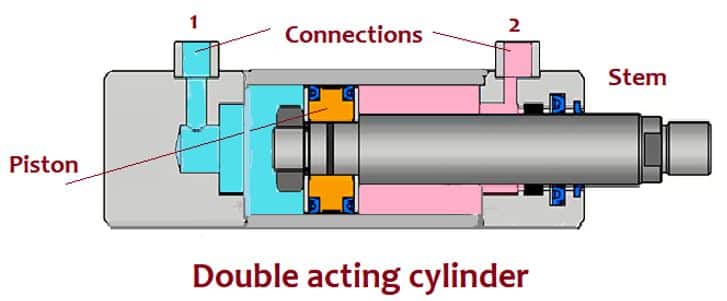
Double-acting hydraulic cylinders are linear hydraulic actuators that perform the movement in both directions by means of hydraulic pressure. The piston stroke in double-acting cylinders is much longer than a single-acting cylinder.
Rotary hydraulic actuators:
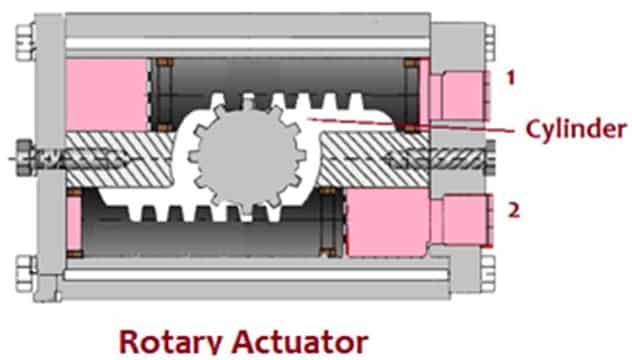
Rotary hydraulic actuators can be of a different type depending on the process to be carried out, be it continuous rotation or rotation by a certain number of degrees, to perform a small turn of a few degrees or up to 360 degrees, that is, one turn.
Hydraulic motors
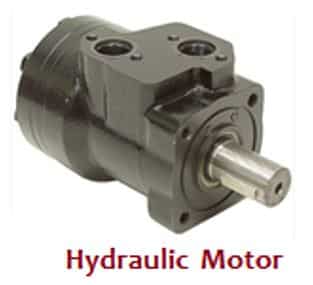
Hydraulic motors can perform the same function as an electric motor but with some advantages depending on the characteristics of the process. The size of the motor is much smaller since the hydraulic unit is usually located in an area independent of the place where it needs the movement.
Advantages of hydraulic actuators
- The actuators can be far from the pump and the circuit, hydraulic power station, without suffering the loss of force.
- They can perform more power with not-so-heavy equipment in relation to pneumatic or electric actuators.
- They can perform much higher forces, having equipment of the same size as other energies such as pneumatics. It is being able to exceed the force with respect to pneumatics by more than 20 times.
- Hydraulic actuators can withstand pressures up to 4000 psi.
Disadvantages of hydraulic actuators
- Hydraulic actuators and hydraulic circuits, in general, tend to have some small leaks of hydraulic fluid in certain parts of the circuit such as fittings, unions, valves. This generates small efficiency losses, normally negligible.
- To carry out a linear or rotary movement one need a large number of components that are part of the hydraulic circuit, such as the hydraulic power station, with the pump, tank, valves, etc.
- Noise is another disadvantage as hydraulic circuits tend to be louder than electric and pneumatic actuators.
Read Next: