Energy efficient motors are the most economical because these motors have higher efficiency than conventional motors like EFF-1 and EFF-2. The economic production of the product is the need of the day, and therefore, every industry uses energy-efficient motors. The major energy-efficient motors are IE1, IE2, IE3 & IE4. In this post, we will discuss energy efficient motors and their applications.
Efficiency Classes of Energy Efficient Motors
The efficiency of the equipment is the prime consideration for the designer and the user. The efficiency of the equipment must be as high as possible to save electricity. Efficiency is defined as how efficiently the system converts the input electrical energy into other forms of energy. The losses in the conversion process need to be minimized to get higher efficiency.
Much research has been done to reduce the losses in the induction motor. As a result, the premium efficiency (IE3) and supreme premium efficiency (IE4) classes of motors are available on the market.
About 30-40 % of the generated electrical energy worldwide is consumed by electric motors. Therefore, there is a need of the day to improve the efficiency of motors.
Two types of losses – Iron losses and copper losses- mainly occur in the induction motor.
Constant or Fixed Losses
The constant or fixed losses in the motor are voltage and frequency-dependent. The voltage and the frequency almost remain fixed, so the losses on account of voltage and frequency- Eddy current and Hysteresis losses remain fixed. The fixed losses can be reduced by selecting a soft material with high permeability. The losses can be reduced by designing a low air gap length motor.
Variable Losses
The variable losses depend on the loading of the motor. The higher loading on the motor leads to more slip and more copper losses. The resistivity of the winding material plays a vital role in assessing the copper losses in the induction motor.
Efficiency is defined as the ratio of output to input power.
Efficiency= Output (Power developed at the shaft)/Input (electrical power input)
= (Input-Losses)/Input
= 1-(Losses/Input)
If the losses are zero, the efficiency is 100 %. However, pragmatically, it is not possible to achieve 100 % efficiency. If the motor’s efficiency is 90 %, it converts 90 % of electrical energy into mechanical output, and the balance 10 % of the electrical energy is dissipated as heat.
Classifications of the efficiency classes as per IEC:
Standard IEC Line Motors (IEC 60034-30-1)
The new standard IEC 60034-30-1 replaces the standard IEC 60034-30:2008, which has defined three efficiency levels for three-phase induction motors. The updated standard IEC 60034-30-1 now includes the fourth efficiency level IE4. Furthermore, 8-pole motors and an extended power range are now included in the standard.
In the IEC 60034-30-1, the following efficiency classes are defined for induction motors (IE = International Efficiency).
What is IE?
IE is “International Efficiency” with classes 1, 2, 3 & 4, i.e. IE1 & IE2, IE3 & IE4.
IEC Efficiency Limits
The chart below shows the efficiency of the motor in different efficiency classes.
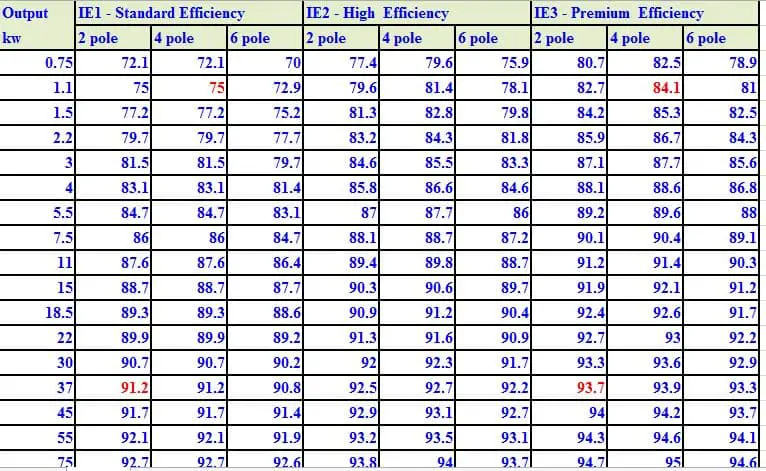
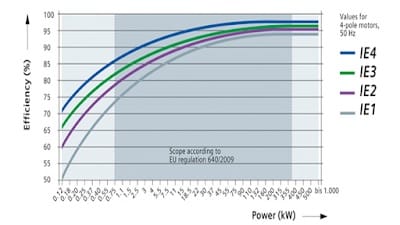
How is higher efficiency achieved in energy-efficient motors?
The materials and mechanical and electrical design of the motor are the factors that affect its efficiency. Energy-efficient motors are manufactured using high-quality material with an optimized design.
The following design considerations are adopted for energy efficient motors.
- A large-diameter copper wire is used for winding to reduce the coils’ resistance. Reduced coil resistance reduces the motor’s copper losses.
- Optimization of the air gap length to reduce the stray & magnetization losses. The motor’s power factor also improves with less air gap length. The overload capacity of the motor gets reduced with the reduction of the air gap length. Therefore, the driving load characteristics must be checked before installing energy-efficient motors.
- An optimized cooling fan design to reduce windage loss.
- Thinner and higher-quality steel lamination in the stator and rotor core reduces the core losses.
- High-quality bearings are used to reduce friction losses.
Calculation of cost saving in Energy Efficient Motor

- Hrs = Annual running hrs
- kW= Motor rating in kW
- % FL = Fraction of full load in running condition
- ηstd = Efficiency of Standard Motor
- ηeff = Efficiency of energy-efficient motor
Great article