Solder paste is one of the fundamental and essential things required for soldering different electronic components onto a Printed Circuit Board or a PCB. Solder paste is used with an infra-red reflow machine during the PCB assembly process. But what exactly is a solder paste? What is it made of, and how to use it? Let’s address these questions one by one in detail.
Table of contents
What is Solder Paste and Solder Flux?
Solder paste is a mixture of solder in powder form and solder flux. The solder is a metal alloy made up of two or more metals, whereas the solder flux is a creamy material made up of different chemicals. Solder flux is used before and during the soldering process to remove oxides and impurities and thus enhance the flow of solder on the surface. Hence, a solder flux is also a purifying agent.
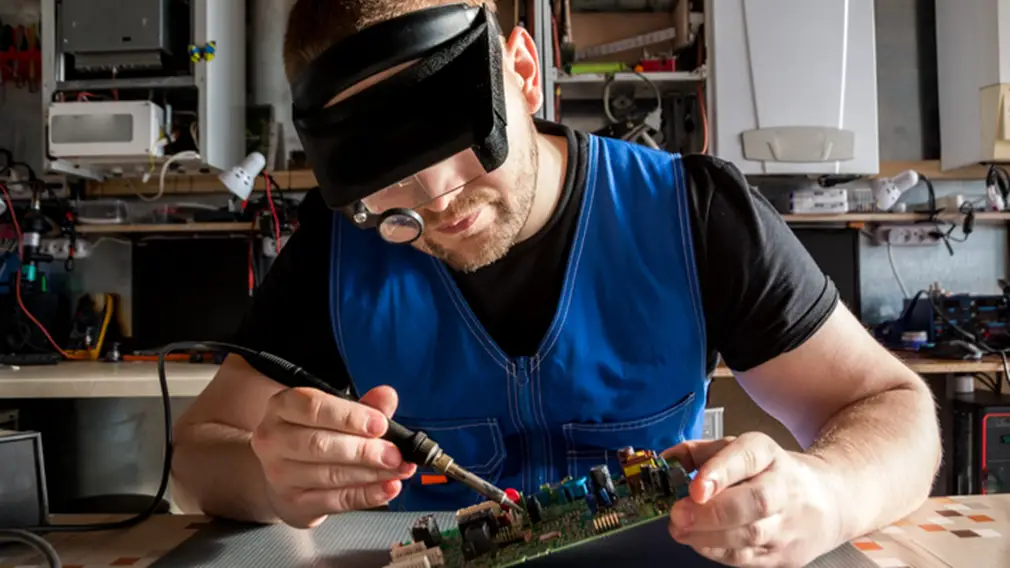
For a long time, solder made of Lead and Tin were used. But with awareness regarding health hazards that these elements could cause and stringent laws around the world, more lead-free alternatives are being used now. One such solder contains 99% Tin and 1% Copper, while a few of them have a small amount of other metals as well.
Classification of Solder Pastes
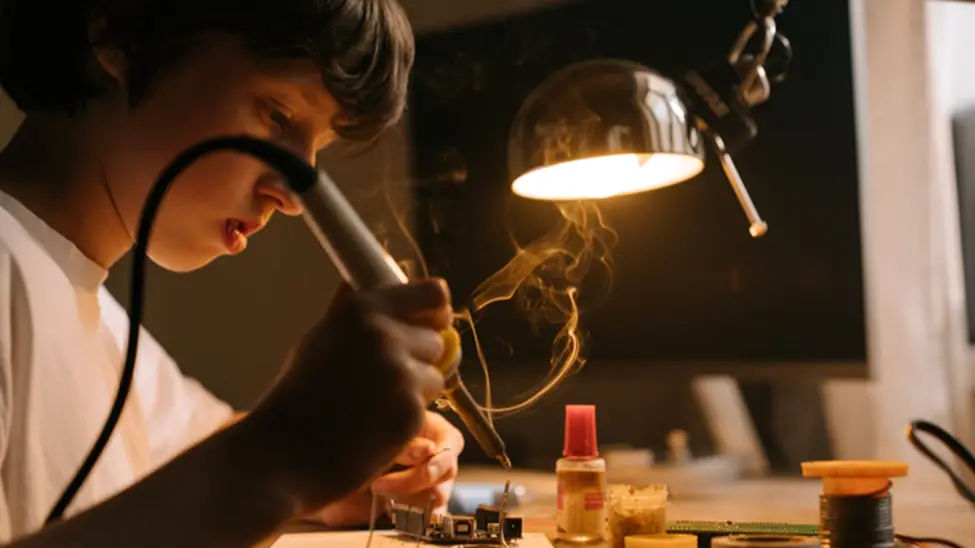
Solder pastes can be classified based on three criteria
- Classification based on Size
- Classification based on Flux type
- Classification based on Material
Classification based on size
There are various grades of solder paste based on the size of small solder balls. Before starting the PCB assembly, it is important to choose the required grade, which can help with the process. Based on the particle size as per the IPC J-STD 005 standard, here are the different types of soldering pastes.
Type designation according to IPC J-STD 005 Standard | Particle size in µm |
Type 1 | 150-75 |
Type 2 | 75-45 |
Type 3 | 45-25 |
Type 4 | 38-20 |
Type 5 | 25-10 |
Type 6 | 15-5 |
Type 7 | 11-2 |
Type 8 | 8-2 |
Classification based on Flux type
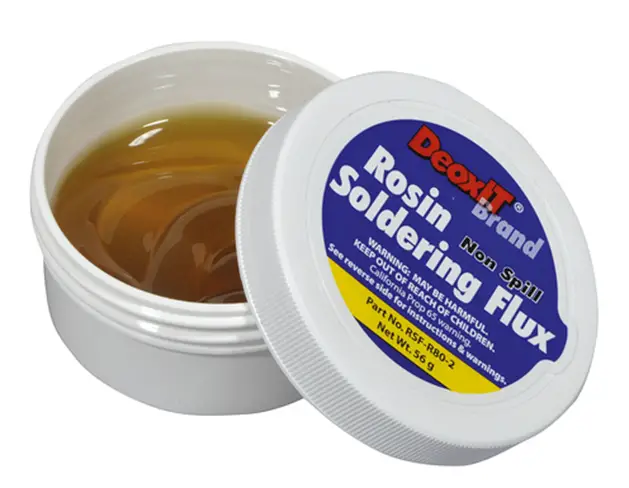
According to the flux type, there are three main types of the solder pastes.
- Rosin Flux: Rosin flux or Rosin paste is made of Rosin which is a natural extract from the Pine trees. Rosin flux forms a natural barrier against moisture and is suitable for clean and easy-to-solder surfaces. It has a relatively low activity. The remains of this flux can be cleaned after the soldering process using suitable solvents if required.
- Water-soluble flux: Water-based flux provides better and stronger bonds in the soldering process. It is made of different Organic acids, Thixotropic, and solvents. Its activity levels vary from no activity to extreme activity and can be used to solder on difficult or irregular surfaces. As it has a wide area of activity, it is important to take note of the product specifications as per the corrosion ability and electrical conductivity. There are many cleaning agents for these fluxes, including water.
- No-clean Flux: It is made of Rosins, solvents, and a small amount of activators. It is suitable for low to moderate activity. No-clean flux, as the name says, requires no cleaning, but if required, then water and a suitable solvent can be employed. This flux saves cost as no cleaning is required after the soldering process and hence it is highly preferred. However, this flux is suitable for clean and easy-to-solder surfaces only and may require a clean, inert reflow environment.
Classification based on material
- Lead-based solder paste: This paste consists of a metal alloy with Lead and Tin forming its base constituent. Owing to the environmental and health hazards that Lead poses, there are strong regulations around the world because these are not being used actively in industrial processes.
- RoHS Lead-free solder paste: RoHS stands for Restriction on Hazardous Substances, and hence, it promotes the use of Lead-free alternatives for solder paste. These are made up of elements like Copper, Tin, Nickel, Silver, Zinc, Bismuth, and Antimony. It is both environment-friendly and safe to use.
How does a solder paste work?
A solder paste helps in creating the bond between the metal surface and the electronic component on the board, known as SMD or Surface Mounted Devices.
A solder paste requires heat, just like in the case of regular soldering. The solder paste is applied on the printed circuit board or the PCB and is provided with heat. This causes the solder paste to melt into solder powder and solder flux.
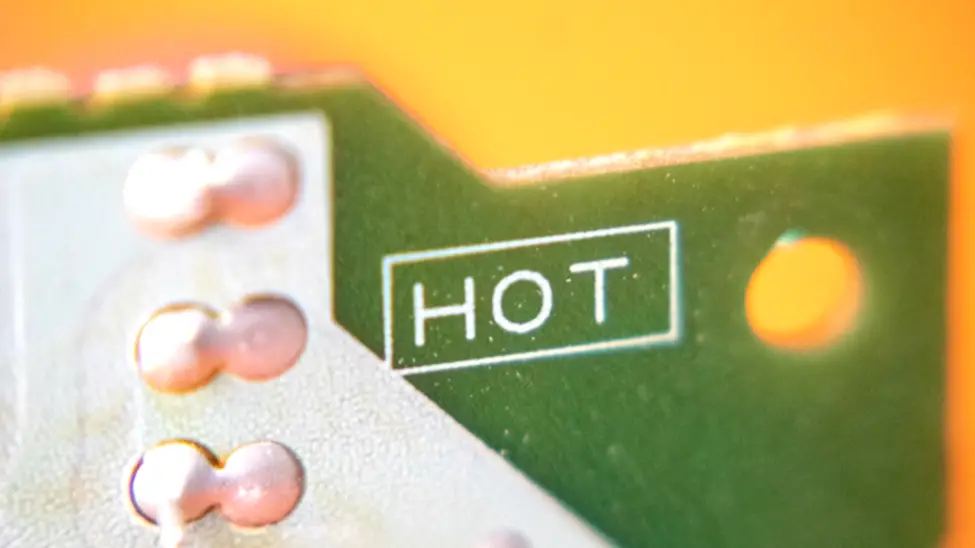
The solder powder primarily forms a bond between the metal surfaces, while the solder flux plays various roles. First of all, the solder flux gives flowing properties to the solder powder, which makes its application easy. Secondly, it acts as an adhesive material to hold the electronic SMD components in place on the board as they are soldered into it. Last but not least, it removes impurities and avoids oxidation from the electronic components for a better and stronger bond between the leg of the component and the surface of the PCB.
Storage of solder paste
Solder paste is one of the most important components that electronic hobbyists and manufacturers need most of the time. We have already discussed different types of soldering pastes and their properties. For optimum utilization and performance, the soldering paste must be stored correctly. Otherwise, it may lose its quality over time and will be rendered useless.
One of the greatest concerns for any solder paste is its oxidation over time. To prevent this, it is important to store the paste in an air-tight container so that it may not get exposed to air in any way. The very large surface area of the minute solder particles implies that it may be exposed to air and is getting oxidized.
Additionally, the solder paste must be stored at an appropriate temperature. Too high a temperature may degrade the quality of the solder paste, and it may lose its adhesive properties. Also, the problem of oxidation increases at high-temperature storage. However, these shouldn’t be stored below the freezing temperature as it is equally problematic.
One should be mindful of the expiry date of the paste as given on its package. The solder paste begins to degrade beyond the expiration date, and using it may not be that effective. In such a situation, there is a risk of the electronic component coming off its place and making contact with any nearby component, thus causing the entire board to blow up. In such a situation, the cost of replacing the board will be much higher than that of replacing the solder paste on time.
How to use solder paste?
It is easy to make use of the solder paste after using it in the soldering process a couple of times. Before making use of the solder paste and the entire solder process itself, it is important to make sure that the printed circuit board and the components are clean. Make sure that the soldering paste is at room temperature. Also, ensure that all the components that are required are at your disposal. Having done all of this, we can go ahead with the solder process, and here is how to do it step by step.
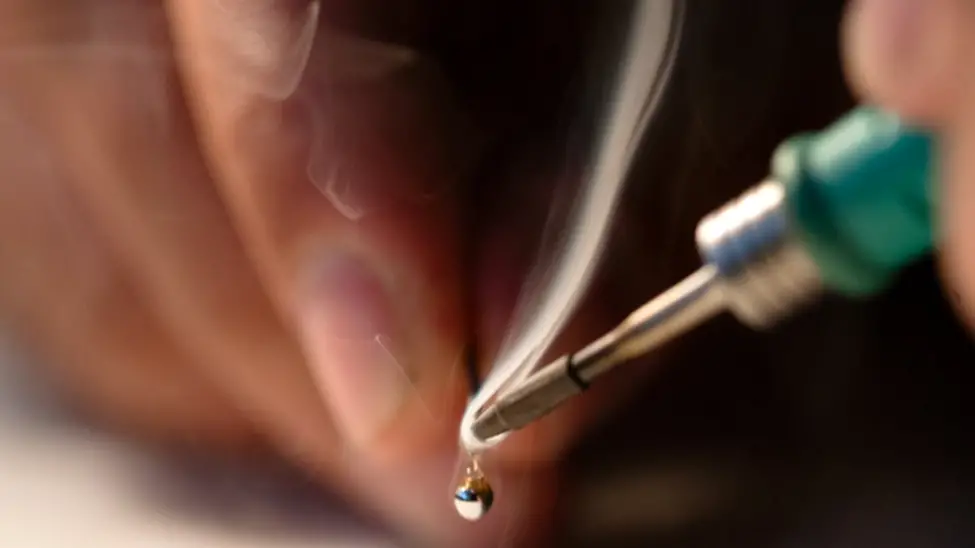
- Apply the solder paste where you want to mount the SMD component. This can be done using a Syringe or a stencil.
- Now, place the component on the circuit board carefully and ensure that it is properly aligned as required.
- Finally, apply the heat to melt the paste so that the solder powder and the flux can properly form the bond between the surface and the component.
- Ideally, the heat is provided by an Infrared reflow oven, but an economical and popular way to apply heat is by using a heat gun.
- A soldering iron can also be used for this purpose, but one should be cautious as the heat from the iron can destroy the electronic components if not handled carefully.
This is all about the solder paste, its type, characteristics, and usage.