Instrumentation & Control is the branch of engineering that deals with process measurement and its control. The various industrial processes require a series of measurements & controls to achieve the required final product. Thus, instrumentation has vital importance for these processes to control and maintain some variables constant.
The Instrumentation and control is a vast area, with two branches clubbed to form a new branch.
Instrumentation engineering especially focuses on the principle and operation of measuring instruments that have wide applications in the design and configuration of automation systems. The automation system may be applicable for electrical, pneumatic domains, or other domains.
It is a specialization that combines different sub-branches. These are control systems, automation, electronics, and information technology.
Instrumentation deals with the measurement of the process variables (PV). A few examples of process variables are pressure, flow, level, temperature, pH, conductivity, speed, humidity, etc.
According to Instrumentation and Systems Automation Society(ISA) the definition of Instrumentation as per Reference: ISA std. S 51.1– is a collection of Instruments and their application for the purpose of observation, Measurement, and Control.
Controls deals with automation and the development of process control systems.
Why instrumentation is necessary?
It has been possible to manufacture complex products in stable conditions of quality and homogeneity, with fixed characteristics, conditions. Without the support of measurements, it would be impossible or very difficult for the operator to control the process through manual control.
The instrumentation of a control system is the ability of the human being to be capable to measure and control processes and the environment.
Thus the major role of Instrumentation is
- Measurement of physical parameters like pressure, temperature
- Display of measured physical parameters in an interpretable form
- Input data for control loops to control the physical values at the site.
Measurement and control
The measuring instruments play the most important role, they allow for the maintenance and regulating of various process variables in ideal conditions. We can define measurement as a set of various elements that form an instrument. It converts a physical variable into a signal or indication that we can easily interpret.
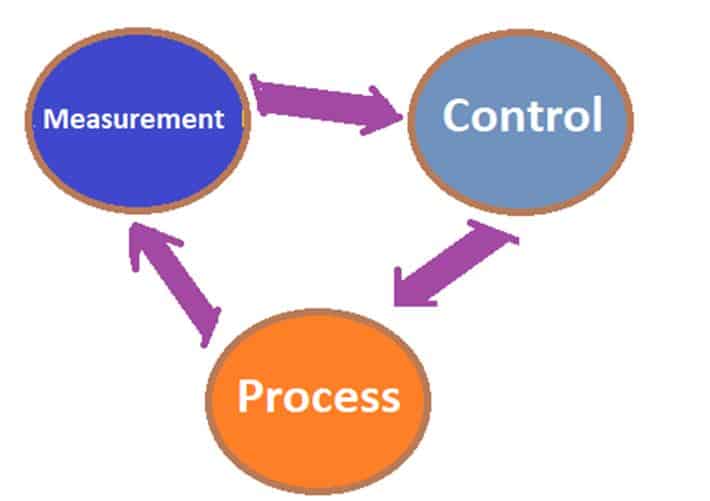
International standards such as ISA, API, IEC, NEC & ANSI regulate the measurements and control of processes used in instrumentation. International standards ensure that various elements are within the required limits.
Automation
Industrial instrumentation has a remarkable importance in automation processes. It is capable of maintaining controls and monitoring a complete industrial system. Additionally, to ensure the proper functioning of automated factors.
Plant automation ensures accuracy, efficiency with the least manpower. Further, it is capable of establishing quality standards and results.
Industrial instrumentation – a brief description.
Industrial processes, especially those aimed at automation, need industrial instrumentation. It is a set of factors that help ensure and improve industrial processes and how they manage their resources.
Industrial instrumentation considers variables, and measures, converts, and records them to ensure processes. To achieve this protocol, engineers in the area use special equipment as well as specialized devices.
As a starting base, there is the measurement and control of processes that usually measure physical factors such as:
- Pressure and force
- Flows and levels
- Temperature
- Speeds and weight
- Humidity and dew point
- Chemical features such as pH and electrical conductivity.
The transmitter output can be viewed – in-built local indicators, also gathered in the control room. The DCS, PLC, or SCADA systems receive the signal for further processing. We can view the display of measurements and loop control in the human-machine interface (HMI). Analysis of generated alarms and acknowledgment can be done from the same HMI panel.
Characteristics of real-time industrial instrumentation
The characteristics of industrial instrumentation in real-time applications are based on its architecture. In short, an instrumentation system has sensors, transducers or input devices, controllers, processors, transmitters, and actuators or output devices.
The sensor converts the physical value to an electrical signal. For example, RTD converts temperature into voltage for onward processing and displaying in PLC & SCADA systems.
The transmitter converts the electrical signal( generally in a voltage form) to a 4-20 mA current signal for transmission over a long distance.
It is possible to control the instrument directly if required. The signal is generally sent to a PLC.DCS, SCADA system, or other controllers. The system interprets the data and displays data to the operator, and it also simultaneously control the process.
Of the many factors that industrial instrumentation encompasses, one of the most important is the sensors. It is a process in which an input perceived by a sensor is converted into an output signal.
This function is of particular importance in automation since the perceived signals are translated into optical, electrical, mechanical signals, etc.
Instrumentation and Control- Question of guarantees
The importance of industrial instrumentation is determined by the care of the equipment investment, the use of resources, work equipment, safety protocols, environment, etc.
Ensuring the good quality of the devices used is vital to having intelligent and efficient processes in the work environment. Industrial instrumentation extends a guarantee in terms of competitiveness and good results in production, as well as cost savings.
The importance of industrial instrumentation has a particular impact on today’s commercial sector. Most benefited industries are
- Petrochemical industry
- Pharmaceuticals
- Power generation
- Chemicals, Pulp & paper
- Automotive industry
- Construction and cement
- Textile industry and Food and beverage industry
Responsibilities of an Instrumentation Engineer
The Instrumentation and Control Engineer is a professional with comprehensive training and skills to develop, manage and advise projects and assemblies for the automation of industrial processes. Solving automation problems, utilizing, and improving existing systems in the plant.
The instrumentation and process control engineer participates in the development of the technical specification sheets of the instruments. Specification sheets will integrate the control loops, as well as the control architecture. We use it for the review of the piping and instrumentation plans. Also for the development of the control logic, which can be electronic, pneumatic, or hydraulic.
Design, preparation, evaluation, revision, analysis, and/or modification of the following documents.
- List of Instrument, P&IDs,
- Instrument diagrams, Instrument datasheets,
- Wiring diagrams, Technical specifications,
- Requests for quotation, for purchase,
- Calculations,
- Both Preventive, predictive schedules,
- List of spares, Calibration planning,
Responsibilities of Instrument technicians, mechanics
The role of the maintenance technician may be more specialized in instrumentation & control, knowledge of the process, mechanical, and electrical. Assisted by mechanics in the installation of new equipment, modifications, calibration of equipment, inspection, routine tests, troubleshooting of specific machines. The responsibilities may vary based on the size, type of an organization.
Preventive maintenance tasks, attending breaks downs, and corrective maintenance in accordance with the maintenance protocols. Keeping various records is also part of the job.
Instrumentation and Control–Safety
It is of the utmost importance, in every aspect of day-to-day plant maintenance activities. Attention is required for a safe working environment for personnel working in the field and also equipment.
Advantages of instrumentation and control
There are several advantages of instrumentation & control in the process industries.
- Significant improvement in productivity.
- Increases competitiveness in the market.
- Data flow optimization.
- Increased safety of the workforce, especially in cases where hazardous, explosive atmosphere, temperature, and weight are present.