In this article, we will discuss the leakage & control valves leakage classifications. The main function of the control valves is to throttle the fluid flow, and the basic requirement is that the valve must fully close with no leakage.
It is worth noting that various process requires a different shut-off capability of the control valve. The degree of leakage in the control valve at different operating conditions is given by seat leakage classification.
How well a control valve shut off depends on the following.
- Seat Material
- Actuator thrust
- Pressure drop
- Type of fluid
Types of leakage
We can classify the leakage into two categories.
- Fugitive emissions
- Leakage in the processing pipeline
What are fugitive emissions?
Fugitive emissions are nothing but the leaks of the process fluid to the outside. Leakage takes place in the valve stems or shafts or through the packing and sealing systems. Also, there may be various reasons for leakage through the control valve.
Because of safety and environmental reasons avoiding emissions outside is necessary. Considering fluids that are toxic or pollute the environment. In addition to their danger if the emissions are flammable.
The maintenance of packing is one of the points that require continuous vigilance.
What are process leaks?
It is referring to the leaks of the valve in the process that is how the valve acts as closing elements.
The leaks between plug and seat depend on the design of the trim in terms of the material, manufacturing quality, and tightness. Therefore, the quality of the valve parts plays a vital role in leakage. It further depends on the types of actuators selected.
Reasons for leakage
There are the following reasons of leakage.
- The common reason is not tight shutoff.
- Damaged valve seat
- Damaged seal
- Poor selection of valve packing.
Seat leakage classification
The ANSI/FCI 70-2 standard was developed to measure levels (classes) of plug-to-seat leakage, in control valves only.
The ANSI/FCI 70-2 is an industry standard for control valve seat leakage, specifies six leak classes (Class I, II, III, IV, V, VI) for control valves, defines the procedure, and supersedes ANSI B16.104 standard.
Each leakage class uses a different acceptance procedure and criteria.
The most commonly used classes are CLASS I, CLASS IV and CLASS V, and CLASS VI. Metal seat or Soft seat (such as PTFE) must be selected in the engineering design according to the characteristics of the process medium and the opening frequency of the valve.
Leakage class rates I, II III are less used classes due to requests for lower levels. Generally, leakage class-IV, class-V, or leakage class-VI are suitable for a higher level of tight shut-off requirements.
Leakage Class: Class I
It is popular by the name dust-tight and can refer to metal or resilient seated valves. The followings are the test acceptance procedure and criteria for the Class I control valve.
- Maximum Allowable Leakage – No need of shop test
- Test Medium – Not applicable
- Pressure Requirement– Not applicable
- Test Qualification: No need of proof, but buyer and seller should agree.
- Valve Type: Metal or resistive seated valves
Leakage Class: Class II
Acceptance procedure and criteria for Class II are;
- Maximum Allowable Leakage: 0.5% of rated capacity.
- Test Medium: Air or water at 50-1250 F (10-52 0 C).
- Pressure Requirement: 3.5 bar, operating pressure differential, whichever is less.
- Test Qualification: Less than 45 to 60 psi or maximum operating pressure differential.
- Valve Type: Commercial double-seat or single-seat balanced control valves with a piston ring seal and metal-to-metal seats.
Leakage Class: Class III
Acceptance procedure and criteria for Class III are;
- Maximum Allowable Leakage: 0.1% of nominal capacity.
- Test Medium: As in class II.
- Pressure Requirement: As in class II.
- Test Qualification: As in class II.
- Valve Type: Same as class II, but a higher degree of seat and seal tightness.
Leakage Class: Class IV
It is a metal-to-metal seat classification. Its acceptance criteria are;
- Maximum Allowable Leakage: 0.01% rated capacity.
- Test Medium: As in class II or class III shown above.
- Pressure Requirement: As in class II or class III shown above.
- Test Qualification: As in class II or class III shown above.
- Valve Type Commercial single-seat unbalanced control valve and balanced single-seat control valves with extra tight piston rings or other means of sealing and metal to metal seats.
Leakage Class: Class V
Acceptance procedure and criteria for Class V are;
- Maximum Allowable Leakage: 0.0005 mL per minute of water /inch of valve port diameter/psi pressure differential.
- Test Medium: Water at 50-125 Deg F (10-52 Deg C).
- Pressure Requirement: Maximum service pressure or operating pressure drop across the valve plug, not exceeding body ANSI rating.
- Test Qualification: Maximum service pressure through valve plug does not exceed ANSI rating.
- Valve Type: Metal seated, unbalanced single-seat control valves or balanced single-seat designs with exceptional seating and tightness.
Leakage Class: Class VI
Class VI is for a “resilient seating” closure. It is also known as soft-seat classification. The seat or shut-off disc or both has a resilient material such as Teflon.
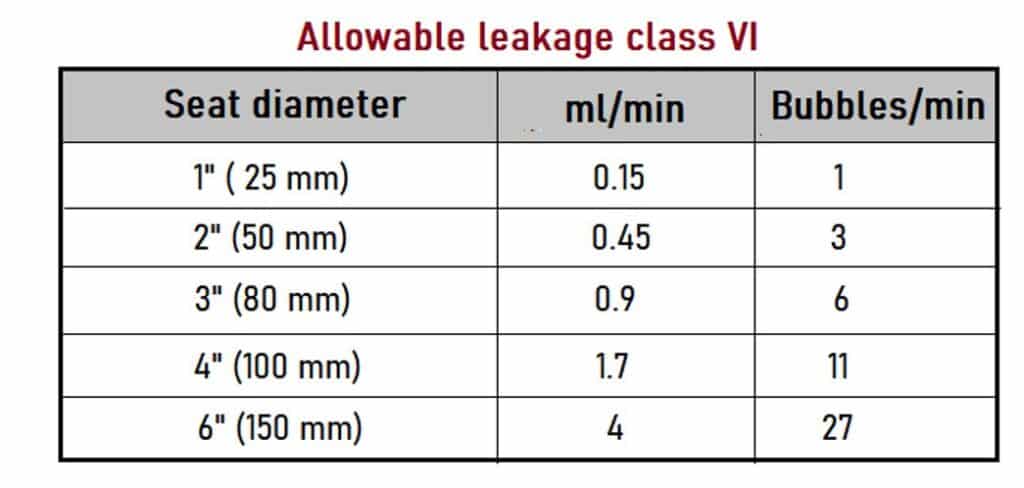
Acceptance procedure and criteria for Class VI are;
- Maximum Allowable Leakage: One should not exceed the number as shown in the table above, based on the port diameter.
- Test Medium: Air or Nitrogen at 50-125 Deg F (10-52 Deg C).
- Pressure Requirement: 50 psi (3.5 bar) or maximum rated Differential pressure across valve plug whichever is less.
- Test Qualification: Maximum service pressure through the valve plug must not exceed the ANSI rating.
- Valve Type: Resilient Seated Control Valves, also unbalanced single-seat or balanced with O-rings or identical gapless seals.