What is DC Motor?
DC motor or Direct Current Motor converts electrical energy into mechanical energy. It is used to drive the mechanical loads. The electric motor operated by the AC supply is called the AC motor, and the electric motor operated by the DC supply is called the DC motor.
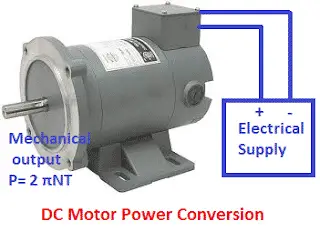
The DC motor and DC generator are similar in construction, but electrically, they are the opposite. The DC generator converts mechanical energy into electrical energy.
Working Principle of DC Motor
The DC motor works on the principle of Lorenz law. When a current-carrying conductor is placed in a magnetic field, it experiences a force. Thus, the force is exerted on the conductor when it is placed in a magnetic and electric field. The force causes motor rotation.
We can find the direction of motor rotation by Fleming’s left-hand rule.
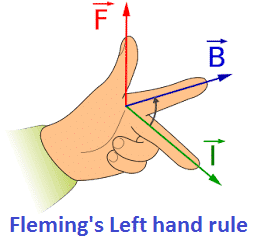
Fleming’s left-hand rule states that if the index finger, middle finger, and thumb of your left hand are extended mutually perpendicular to each other, and if the index finger represents the direction of the magnetic field, the middle finger indicates the direction of the current. The direction of the thumb shows the direction in which the conductor experiences the force, and the DC motor shaft rotates in that direction.
Working of DC motor or Direct Current Motor
The DC motor has two main parts: field winding and armature winding. The armature is the rotating part of the motor, and the conductors of the armature experience the Lorenz force when it is placed in the magnetic field. The field coils produce the magnetic field. The field coils are stationary parts of the DC motor.
DC supply to the armature is given through the carbon brushes. The carbon brushes are required because the armature is rotating, and its supply part is stationary. The carbon brushes are softer than the commutator of the DC motor, so the brushes get worn after running the motor for a certain time. If the brushes are harder than the commutator material, the brushes can damage the commutator. The Electrographite ( EG grades) are generally used in the DC motor.
The DC motor is named according to the connection of the field winding with the armature winding. There are the following types of DC motors.
1. Series Motor
2. Shunt Motor
3. Compound motor
Let us take separately excited DC motors to understand the working of the DC motor. The armature coil has a certain resistance, and the voltage drop occurs in the armature winding when current flows through the armature conductors. Let the resistance of armature be Ra.
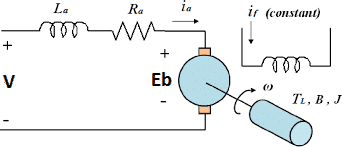
When DC voltage(V) is applied across the armature winding, the motor draws a high current as back emf(Eb) induced across the armature winding is zero. The EMF starts developing as soon as the motor starts rotating. The emf developed across the armature winding opposes the main armature DC supply and thus counterbalances the supply voltage, and the emf developed is called back emf. The back emf(Eb) developed across the armature winding depends on the following;
1. Field Flux
2. Number of armature conductors
3. Speed of rotation of the motor
4. Number of poles
5. Number of parallel paths
The back emf(Eb) can be expressed as;
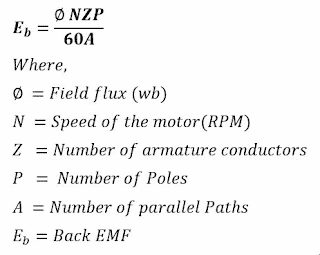
The back emf (Eb) is directly proportional to the speed of the motor. The back emf increases or decreases with an increase or decrease of motor speed. When the load on the motor is increased, the speed of the motor decreases, and a decrease in speed results in a reduction of back EMF. The armature current increases because the voltage difference between the supply voltage and back emf (V-Eb) increases. The torque of the motor is proportional to the armature current, hence the torque increases, and the motor speed again increases. This way, the motor maintains the same speed under variable load conditions.
The armature current of the DC motor is represented by
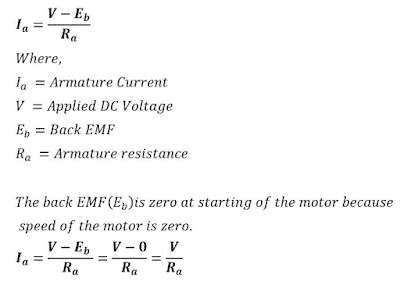
At the start, the DC motor draws a large current because the back emf is absent, and, the armature resistance of the winding is very low. Therefore, a starter is needed to limit the high starting current of the DC motor. In DC drives, the speed reference is increased in the ramp-up manner to limit the starting current.
Read Next:
2 thoughts on “DC Motor or Direct Current Motor”