Hazard Identification and Risk Assessment (HIRA) is a systematic approach to the minimization of hazards. A hazard can be human-made or naturally occurring. Humans and their activities contribute to the causes of hazards. These hazards affect people, the natural environment, property, and services like food production, energy supply, communication, transport, etc.
In the industries, whether an employee gets injured or not, depends on the ability of the person to react to the hazard, the exposure to the hazard, and the severity of the outcome of the exposure.
In some cases, there may not be any injury to the employees, but it is still advised to address the hazard as it may cause future injuries.
To keep a track of all the hazards in a plant, there is a document named Hazard Identification and Risk Assessment (HIRA). This document is used for safely executing routine as well as non-routine jobs. HIRA is one of the most important documents for maintenance as well as operation engineers based on which a job can be executed safely. A job using HIRA is carried out in such a way that all the risks involved in the job are managed using appropriate mitigation factors.
Importance of HIRA
The HIRA document is important for the industry because:
- HIRA helps to determine all possible factors which may harm the workers.
- HIRA helps to determine the probability of incidents and incidents. HIRA also analyzes its severity.
- HIRA helps to identify the existing safeguards and controls.
- HIRA helps to assess the safety risks and make sure they are within acceptable limits.
- HIRA also gives suggestions to counter the likelihood of hazards.
Types of HIRA
There are three types of Hazard Identification and Risk Assessment (HIRA). documents. They are:
Baseline Risk Assessment
A baseline risk assessment is conducted for identifying the risk occurring at the first time. Based on the outputs of the baseline risk assessment, definite aspects or issues will be made noticeable. A baseline risk assessment must be reviewed at regular intervals.
Issue-based Risk Assessment
Issue-based risk assessment is conducted due to prominent aspects or issues, the occurrence of new processes, installing new machines, or the ongoing assessment of hazards in an organization.
Continuous Risk Assessment
Continuous risk assessments are a part of all the observations and inspections that take place on regular routine basis.
Phases of HIRA
Hazard Identification and Risk Assessment (HIRA) have three phases. They are:
Phase 1: Identification of Hazard
The identification of hazards has all the possible incidents determined and cataloged. In this step, field visits and study of all procedures related to operations and input documents like drawing and process write-ups are used in the identification of hazards.
Phase 2: Risk Assessment
Risk management has two sub-parts. They are:
1. Inputs needed in HIRA risk assessment
The Hazard Identification and Risk Assessment (HIRA) is a highly dependent document on the availability and accuracy of the input data. When complete input data is provided, higher confidence in the validity and robustness of the results are achieved.
2. Risk Assessment Methodology
The HIRA is employed for risk management and safety improvement in many industries. It provides a quantitative assessment of the potential risks known. It also provides a basis for the evaluation of process safety with reference to planned risk acceptance criteria. This study method is a combination of identification, analysis, and brainstorming based on the hazards that are identified. It is divided into four main sections. They are:
- Section 1: External and Environmental Hazard
- Section 2: Facility Hazard
- Section 3: Health Hazard
- Section 4: Assess Risk to:
- People
- Asset/Production
- Environment
3. Eliminating the Risk
Here the known hazards are listed and checked within the risk matrix to grasp the importance of risk, safeguarding controls, etc. Measures are described based on the risk rank and at the end, recommendations would be provided to prevent/eliminate the potential hazards.
Steps for making a HIRA
The following steps must be followed for making a Hazard Identification and Risk Assessment (HIRA)
- The job to be done must be identified.
- Job must be split into smaller parts or sub-parts.
- The hazards for all the sub-parts of the job must be identified.
- According to the hazards, a list of all the consequences must be formed.
- The probability and severity of all these risks must be mentioned.
- To control the risk, follow the hierarchy of control.
Likelihood Rating
Likelihood | Description | Rating |
Most Likely | Presumably result of the hazard or event being realized | 5 |
Possible | It has a good probability of occurring and is not unusual | 4 |
Conceivable | It might occur at some time in future | 3 |
Remote | It has not been identified to occur after several years | 2 |
Inconceivable | It is practically not possible and has never occurred | 1 |
Severity Rating
Severity | Description | Rating |
Catastrophic | It has numerous fatalities, irreversible property damage and productivity | 5 |
Fatal | It has a non-fatal injury or permanent disability | 4 |
Serious | It is a disabling but permanent injury | 3 |
Minor | It has minor abrasions, bruises, cuts, first aid kind of injury | 2 |
Negligible | It has minor abrasions, bruises, cut, first aid kind of injury | 1 |
Risk Matrix
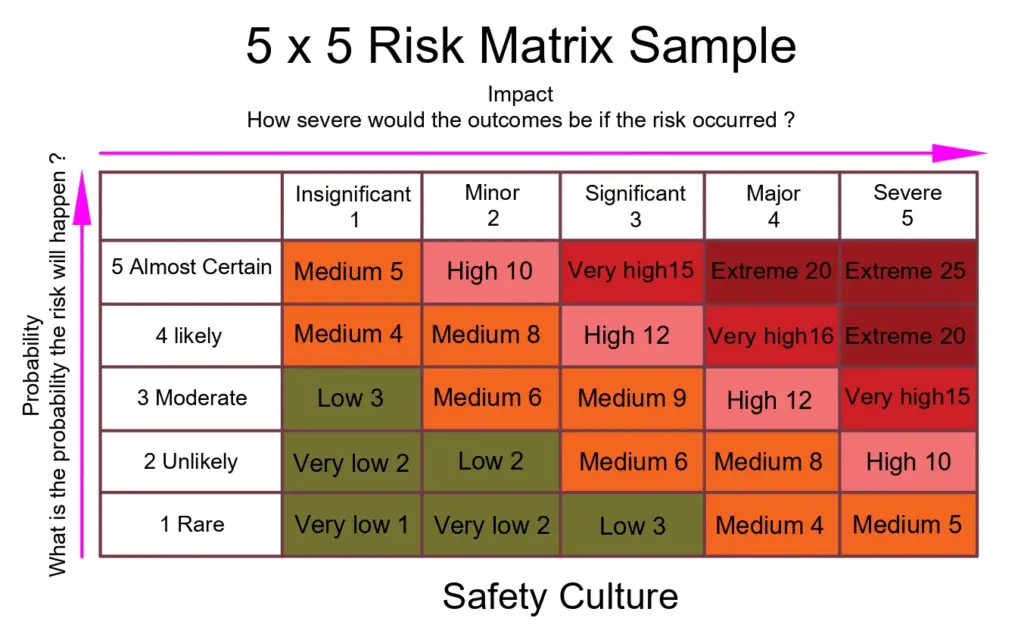
Risk Rating
Risk | Description | Action |
15-25 | HIGH | A medium-risk will need a planned approach for managing the hazard and applying temporary measures when needed. The actions taken must be documented on the risk assessment form as well as the date for completion. |
5-12 | MEDIUM | A medium-risk will need a planned approach for managing the hazard and apply temporary measures when needed. The actions taken must be documented on the risk assessment form as well as the date for completion. |
1-4 | LOW | A low risk can be considered acceptable and any reduction may not be necessary. However, if the risk can be resolved quickly and expeditiously, control measures must be enforced and recorded. |
For low-risk jobs, there are no major precautions that are needed to be taken.
For moderate-risk jobs, it is advised to take precautions so that the risk gets reduced.
For high-risk jobs, higher-level authorities need to be approached. The risk must be discussed with the higher authorities before proceeding with the job. Approvals must always be taken from higher authorities for doing risky jobs.
Hierarchy of control
The hierarchy of control defines the priority for the control of hazards. The figure below shows the same.
The hierarchy of control has five levels by which the risks can be controlled.
- First Level: PPE (Personal Protective Equipment).
- They are worn by the worker performing the job.
- Second Level: Administrative Control Level
- At this level, the way of working can be changed so as to eliminate the risk.
- Third Level: Engineering Control Level
- At this level, engineering measures are taken to minimize the risk.
- Fourth Level: Substitution Control Level
- At this level, the ways of working and hazards are substituted.
- Fifth Level: Elimination
- In this level, the sub-method of doing work is either eliminated or the hazard is eliminated.
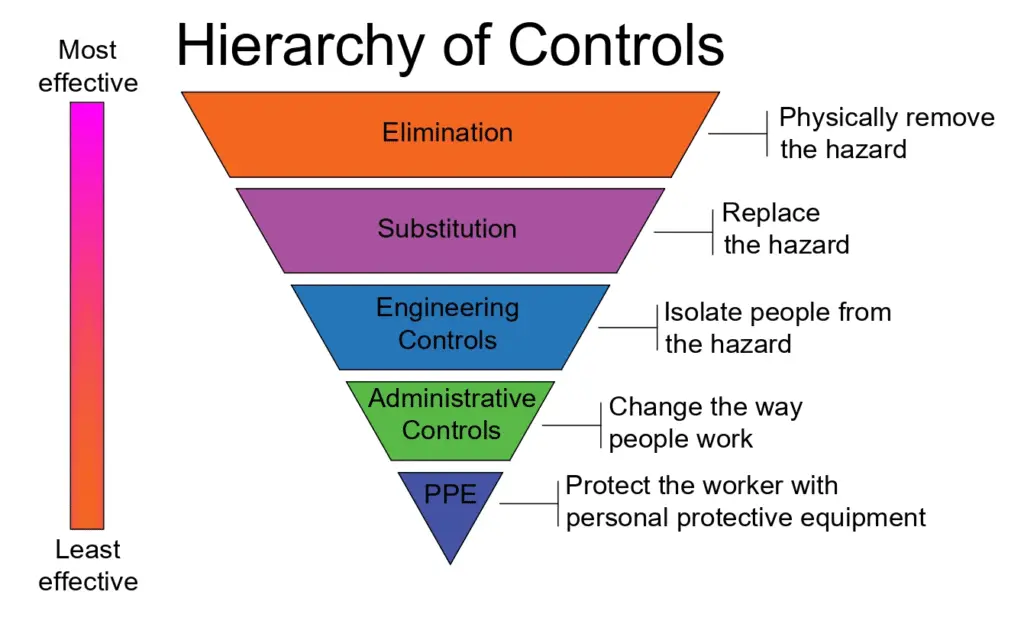
Risk Assessment Stages
The risk assessment has five stages. They are:
- To determine the scope of risk assessment
- To determine the resources needed.
- To determine the type of risk analysis measures.
- To determine the stakeholders involved.
- To determine the appropriate regulations or standards applicable as per organizational policies.