Synchronous generators require adequate cooling in order to ensure proper functionality. Natural cooling processes do not sufficiently provide enough cooling to the alternators. Therefore, forced cooling processes are used in order to provide enhanced cooling to the generators and also to eject a large portion of the heat dissipated by the machine. Based on the method used for forced cooling, the cooling system can be categorized into the following two types.
- Open-circuit cooling
- Closed-circuit cooling
In this article, we will be discussing the open-circuit and closed-circuit cooling of synchronous generators along with their types, advantages, and limitations.
What is Open circuit cooling?
Open-circuit cooling functions by forcing air through the generator machine via fans or blowers and circulating the air drawn inside the generator. The air drawn into the generator is then dissipated out of the machine into the atmosphere. This method of open-loop cooling is used by small-sized generators or alternators.
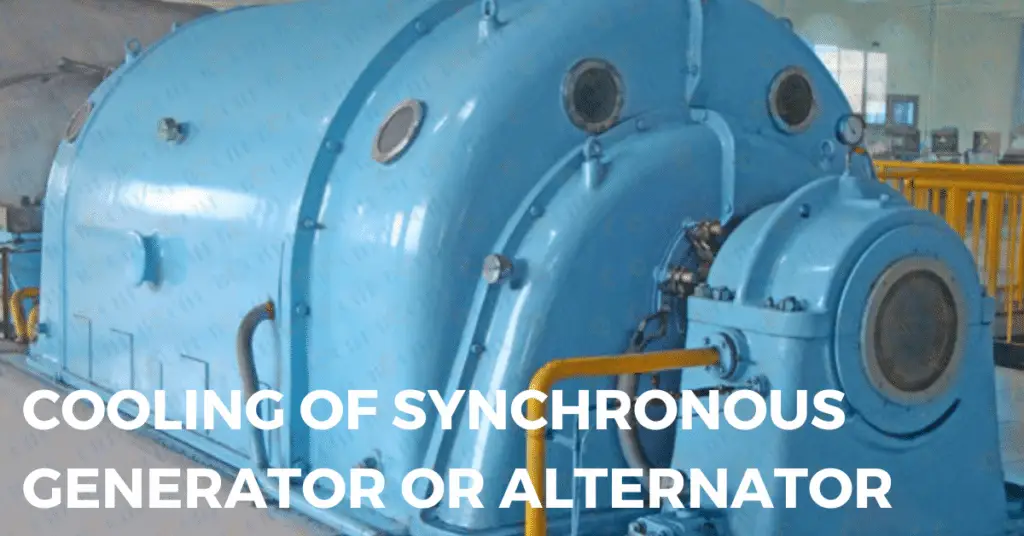
What is Closed Circuit Cooling?
Closed-circuit cooling functions like a closed loop system wherein the hot air released by the generator is cooled by a water-cooled heat exchanger, and the cooled air from the heat exchanger is then sent back to the generator or alternator via fans in order to cool the generator from within.
Cooling air ducts are installed in the cores of the stator and rotor and sometimes even on the field windings, so as to expand the surface area of contact with the cooling air. Based on the direction in which air flows through the air ducts, it can be divided into the following two types –
- Radial Flow Ventilation System
- Axial Flow Ventilation System
What is Radial Flow Ventilation System?
A radial flow ventilation system is described as a cooling system in which the cool air passes from the ducts present in the stator core via air gaps, followed by which the cool air is passed to the back of the stator where it is released to the atmosphere.
Advantages of a Radial flow ventilation
- The loss of energy whilst the cooling process is considerably low.
- The radial flow ventilation system finds its application in both small and large generator machines.
- The temperature increases in the axial direction uniformly.
Disadvantages of the Radial flow ventilation
- The dissipation of heat is comparatively less in comparison to other cooling methods.
- Due to the 20% occupation of the ventilation cooling air ducts within the generator, the size of the generator increases, i.e., it becomes bulkier.
- The radial flow system also has an issue of instability when it comes to the quantity of cool air flowing through the generator ducts.
What is Axial Flow Ventilation System?
Axial flow ventilation system functions by forcing the flow of cooled air through the air ducts in the axial direction, present in the stator and rotor cores. Besides the generators with longer axial lengths, this method of cooling in the axial direction is highly effective.
But the major drawback of the axial cooling air system is that the transfer of heat is not uniform throughout the axial ducts. Since the axial duct loses its cooling effect and gets heated by the time the air has to be released from the outlet part of the generator, this outlet region is not sufficiently cooled, resulting in non-uniform cooling throughout the axial duct.
Circumferential Ventilation System
The circumferential cooling system function by forcing cooled air through numerous inlets of the generator machine present on the outer side of the stator core. The cooled air is passed in a circumferential manner via the air ducts present between the laminations of desired outlets. To suit the application, the size of the ducts can be enlarged.
Moreover, to enhance the process of cooling the synchronous generators, both radial flow and circumferential ventilation flow systems are integrated together. But the major drawback in this combination of the two ventilation systems could be the possible interference of the two cooling air streamflow. In order to prevent this interference from happening, the alternating radial duct pathways are shut at the outer side of the generators.
What are the Necessities of Air Cooling?
In order to ensure adequate cooling of the generators and alternators, the cooling air forced through the air ducts installed within these machines has to be dust and soot-free, particularly in commercial areas. The dust particulates present in the cooling air could block the ventilation ducts, resulting in the minimal or non-uniform transfer of heat throughout the generator ducts.
Air filters installed within the generator and alternators are the solution to circulating dust and soot-free cooling air through its ducts. For instance, specific filters such as cheese filters can be utilized as they are renewed on a frequent basis. In some situations, the cooled air might have to pass via a spray chamber to wash off the dust and other impurities present in the cooling air. Practically and most commonly, water coolers are used for cooling and filtering air and reusing it again in a continuous cycle.
Limitation of Cooling Air
- One of the major drawbacks of air cooling is that above a specified threshold of the generator rating, the cooled air cannot maintain the temperature of the generator within the safety threshold.
- The use of air cooling processes is not ideal for use in the case of large-sized generators and alternators as it would be highly expensive to use bulky fans for cooling and other costly equipment requiring high power consumption.
Hydrogen cooling of Synchronous Generator
Hydrogen gas has a superior cooling property and generators of rating below 500 MW are cooled using a hydrogen cooling system. The ratio of hydrogen and air is marinated in the hydrogen cooling system to avoid an explosion. The hydrogen-to-air ratio of 9:1 is used in a large rating generator.
Direct Water Cooling in Synchronous Generator
The synchronous generator of 500 MW and above rating requires a large volume of hydrogen gas for its cooling. The hydrogen cooling system is uneconomical for such applications.
Direct water cooling is used for the synchronous generator rating 500 Mw and above. In very large turbo-generators, hydrogen cooling is used for the cooling of the rotor and the stator winding is cooled with direct demineralized water. The centrifugal pump circulates the water. The water cooling system has cartridge filters that prevent metallic corrosive particles from entering into winding hollow conductors. The metallic corrosive particles may generate in winding and piping.
Advantages of Water Cooling
- The thermal conductivity of the water is more than that of hydrogen. Therefore, a water cooling system is more efficient for the extraction of heat from the equipment.
- The higher thermal conductivity allows for keeping the lesser duct area for water. It means more space is available for conductors in the slot.
Disadvantages of Water Cooling
- Pure water is non-conductive. Therefore, for a water cooling system, the water should be highly purified.
- Water cooling is comparatively more expensive than the other cooling system.
This is all about the Cooling of a Synchronous Generator or alternator.