What is an unloading valve?
An unloading valve is a pressure control device that is used to dump excess fluid to the tank at little or no pressure.
What does an Unloading Valve do?
Unloading valves are also used in hydraulic circuits where they would stop or remove the flow of the pump back to the tank when the machine is not operating. By the use of these valves, there is a significant reduction of heat. Energy saving is also achieved because the prime mover load is reduced.
These valves can be remotely operated. When an unloading valve is used, the pump can be operated at a minimum load. Hence, the power or energy used will be less. Unloading valves are generally used in high-low pump circuits. Unloading valves may also be used to transfer excess flow from a cylinder to the tank.
Unloading valves are used to relieve the extra pressure in a system, which is at low pressure, and connect it to the delivery pump when it is not used.
What is Pump Unloading?
In some applications, it is required to completely unload pump flow to the tank instead of relieving it over a relief valve. This is done using an unloading valve. The unloading valve responds to the pressure that comes from a remote source. It will allow the pump to build up pressure at a normal rate and then allow it to discharge it to the tank.
When it reaches the pre-set pressure, the unloading valve will transfer the fluid to the tank. Its function is similar to that of a pressure relief valve. But, an unloading valve does not need pressure from its own line to activate. It is activated when the fluid approaches a certain pressure. An unloading valve would unload the pump when system pressure is reached and the pump unloading is done by directing the pump output to a reservoir at low pressure.
Principle of Working of an Unloading Valve
An unloading valve works on the principle of hydraulic force as opposed to a spring force. Since it is a pressure control valve, when pressure builds to a certain point, where hydraulic force is greater than that of the spring force, the valve spool is shifted. It can be controlled by a special cock or a pilot valve.
Working of an Unloading Valve
In an unloading valve, a force is exerted on the valve by the spring, so the valve will stay closed. The valve spool will shift only if the external force is greater than the spring force. The external force will act on the opposite side of the valve spool. Hence, when the valve spool will shift then the output will be diverted.
When the cylinder reaches the end of the extension stroke, then the unloading valve will open. High-pressure oil is present in the pilot of the unloading valve. When the cylinder retracts, the pressure in the pilot of the unloading valve will reduce because of the motion of the piston. So, at this point, the unloading valve will be reset till the cylinder retraction. And at this time, the pump will be unloaded by the unloading valve. The unloading valve will unload the pump after the retraction strokes.
Types of Unloading Valves
There are two types of unloading valves. They are
- Direct-operated pressure Unloading valves
- Pilot-operated pressure Unloading valves
Let us have a detailed overview of both types of unloading valves.
Direct Operated Pressure Unloading Valve
Direct Operated Pressure Unloading Valves have a spool held in the closed state by a spring. (Spool is a cylindrical unit that has a large diameter and is machined to slide in a close-fitting bore of a directional control valve body) during the normal condition, the spool would block the flow from the inlet to the tank.
The high-pressure fluid from the pump will exert a force against the pilot as it will enter from the external pilot port. So, it will exert a force against the pilot when it is entering from the external pilot port. Hence, the force is exerted against the pilot piston.
When the system pressure is more than the spring pressure, then the fluid would be diverted to the tank. If the pressure goes beyond the spring setting, the spool will open fully and dump the surplus fluid into the tank at little or no pressure.
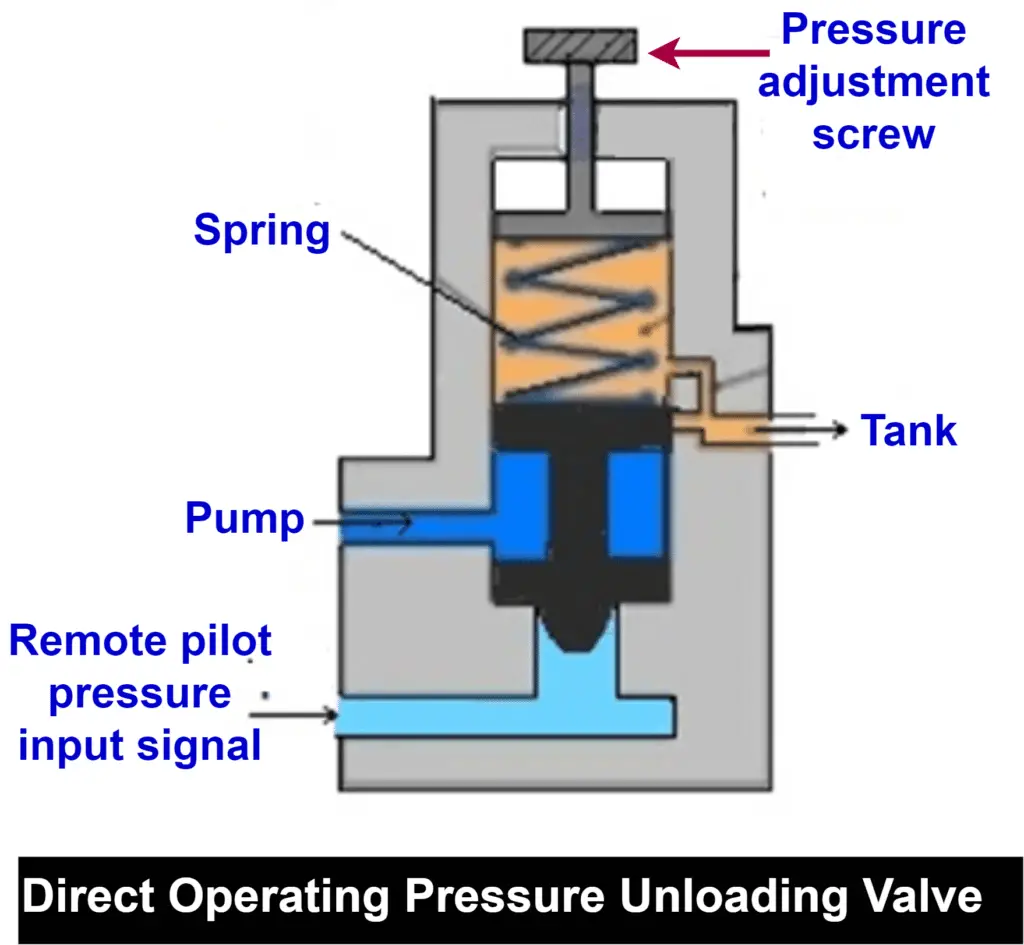
Pilot Operated Pressure Unloading Valve
If there is a need such that it is necessary to control the main valve, then the unloading valve is made up of pilots. The plunger which is present in the main valve has a port that transfers the system pressure on both ends of the plunger.
The valve will be closed as pressure is exerted by the spring. When the pressure on the system is dropped to a certain preset value, the valve would close. These valves can control the opening and closing pressure.
The pilot-operated pressure unloading valves have an unloading spool. This feature is not present in a pressure relief valve. If the unloading spool is not present it would function as a pilot-operated relief valve. The pressure build-up within the pilot section will open and a certain amount of fluid is allowed to flow to the tank. This will make the poppet unbalanced. Hence, it will open and relieve the excess pump flow to the tank.
The unloading spool will receive a signal through a remote pilot port if the pressure in the working circuit increases more than its setting. Along with it, the fluid pressure on the spring-loaded ball in the pilot section will start to open it.
The pressure drop on the front side of the unloading spool will bring back force and pilot pressure from the high-pressure circuit will force the spring-loaded ball completely from its seat.
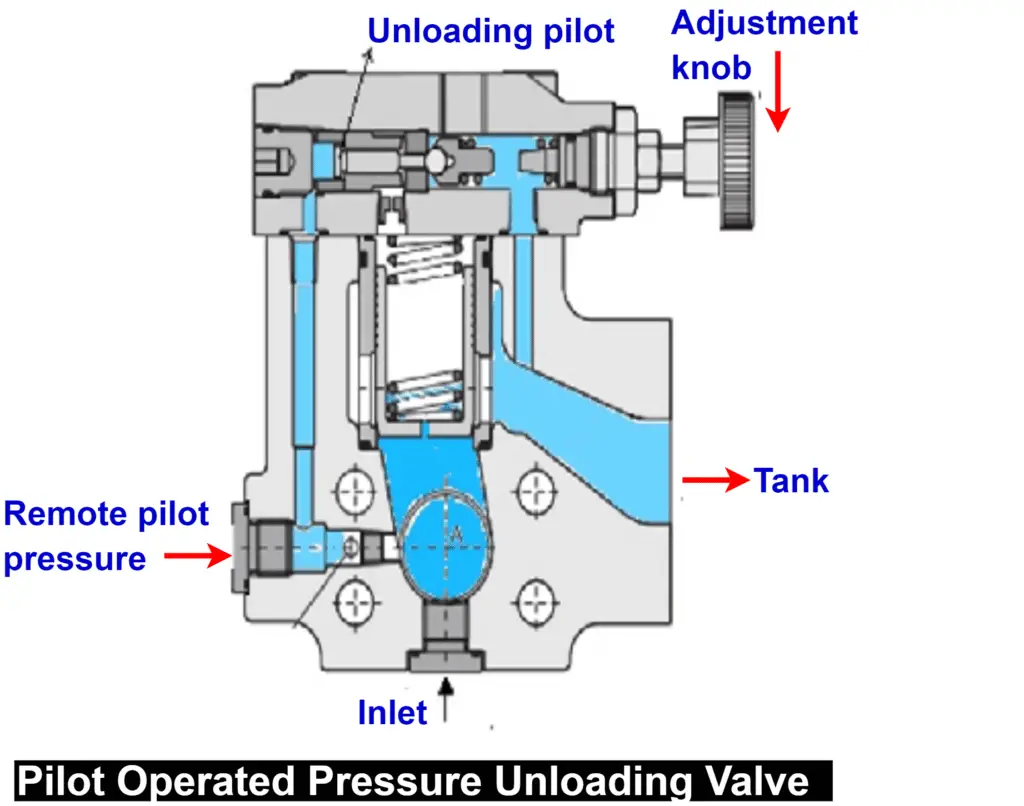
Advantages of unloading valves
Unloading valves offer the following advantages:
- In an unloading valve, the pressure is relatively less as compared to a relief valve.
- The heating of oil can be avoided by recirculating with a second pump in the circuit.
- Less energy is consumed.
- Due to the use of unloading valves, smaller and less expensive directional control valves can be used. At the same time, the pressure drop can also be kept low.