Dynamic braking is the method of stopping the motor by dissipation of heat in the resistor. When VFD drives a motor, the motor acts as a generator when the motor’s actual speed is more than the VFD frequency. The generated energy dissipates in the resistor( Dynamic braking resistor), leading to the motor’s braking.
What is braking?
When the motor is required to stop faster than the normal speed of the motor, it is known as the braking of the motor. During the motor’s deceleration, the motor’s actual speed can be more than the drive set point if the load inertia is greater.
The opposite torque against the normal running torque is applied to bring the motor speed down as per the set point of the inverter frequency.
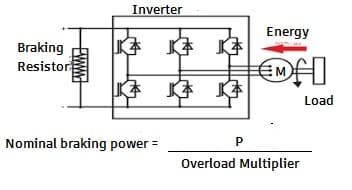
Braking is required in applications like centrifugal fans and rotary kilns because of high inertia loads. The braking is also required in machine tools, winches, and crane applications. The motor can be operated in four quadrants: Forward and reverse driving and forward & reverse braking.
Why is Braking Required?
Because of high inertia, the load connected to the motor shaft does not allow the motor to decrease the speed at the same rate as the inverter frequency. In this situation, the motor speed is more than the synchronous speed of the motor, and it will work as a generator. The synchronous speed of the motor is;
s= (Ns-N)/Ns
s- slip, Ns- Synchronous speed, N- actual Rotor speed,
If the motor’s actual speed is more than the synchronous speed, the slip of the motor is negative, and the motor will act as a generator. As a result, the motor starts feeding energy to the source side. The energy can either be dissipated in resistance or fed to the source for braking the motor.
Methods of Braking Induction Motor Fed from VF Drive
There are three methods that can be used for breaking the motor.
1. DC injection in the stator of the motor
2. Dynamic braking
3. Regenerative braking
In this article, let us first discuss dynamic braking, primarily used in variable frequency drives.
Dynamic Braking in Variable Frequency Drive
First, let us understand the working principle of the VF drive. The drive has three major sections: the converter, DC capacitor, and inverter. The converter section rectifies the three-phase supply using the p-n junction diodes or the IGBTs. The converter section can be of 6 pulses or 12-pulse configurations. If the drive is of large rating, 12 pulse rectifications should be preferred so that lower-order harmonics 5th and 7th get eliminated. The block diagram of the VF drive is given below.
The input three-phase supply is fed to the diode bridge rectifier that converts AC voltage into DC voltage. The magnitude of the DC voltage at the capacitor terminal is 1.35 * Vrms, where Vrms is the input supply’s root mean square (RMS) value.
The DC voltage is fed to the inverter circuit. The inverter circuit has six IGBTs (Insulated Gate Bipolar Transistor). The IGBTs are switched on and off through the PWM(pulse width modulator) controller.
In pulse width modulation, the carrier frequency (Range 1KHz-15 KHz) is modulated with the sinusoidal frequency (Range 0.1 -50 Hz) to get the base drive pulses. In the PWM inverter, both the voltage and frequency are increased/decreased at the same rate to maintain the constant flux in the motor to ensure constant torque delivery.
Working of Dynamic Braking in VFD
When the motor is driving a high inertia load and if the speed of the motor is reduced by decreasing the frequency, the speed of the driving equipment does not lower according to the set point of the inverter.
In this condition, the actual speed of the motor is more than the synchronous speed, and the motor acts as a generator, and it starts feeding energy into the capacitor bank through the IGBTs of the inverter. As a result of this, the voltage across the capacitor bank increases. In normal conditions, for a 440 Volt drive, the voltage across the capacitor is 635 volts; however, if the motor goes into generating mode, the voltage across the capacitor bank increases.
The additional energy that gets stored in the capacitor bank during generating mode operation needs to be dissipated to lower the speed of the motor.
Block Diagram of Dynamic Braking in VFD
The block diagram of the dynamic braking in VFD is given below.
When the voltage increases above its rated voltage, the drive senses it as an over-voltage, and the controller switches on the dynamic braking transistor, and the additional energy gets dissipated in the braking resistor. The capacitor voltage returns to normal voltage level after dissipating the additional energy in the braking resistor.
Good learning platform