A LASER sensor is a measurement value recorder that works using the LASER technology. A LASER sensor converts the physical measured value into an analog electrical signal. LASER sensor uses LASER light/ rays to sense an object. If we talk about LASER sensors as transducers, LASER sensors convert light energy into electrical energy. LASER sensor is used for contactless measurement.
What is a LASER?
LASER is an acronym for Light Amplification by Simulated Emission of Radiation. In a LASER, the energy is amplified to extremely high intensity. LASER sensor generates energy in form of light which is close to the optical portion of the electromagnetic spectrum.
Working Principle of a LASER Sensor
In a LASER sensor, the measurement of distance is based on the triangulation principle. By this principle, the LASER beam will be incident on the object. LASER sensor would strike the object as a small point; some part of the light will be reflected back. The receiver of the sensor will detect the position of this point. The angle of incidence will change according to the distance and so will the position of the LASER point in the receiver.
Working of LASER Sensor
LASER beam is incident on the object which is to be sensed. Since LASER is a highly focused beam of light, it would appear as a small bright dot.
When the LASER beam is incident on the object which is to be sensed, some part of light would be reflected back by the object. This reflected light is sensed by a receiver in the sensor, say a photodiode. The sensor has internal circuitry that would do the signal processing part.
In signal processing, the time taken by the light to emit and the time taken by the light to reflect back are calculated. The speed of LASER light emission is fixed. So, the object’s distance from the sensor can be calculated simply by using speed and time. The sensor will generate an electrical signal according to the distance sensed. This signal is either digital or analog.
Types of LASER sensors
Different types of sensors that function on the basis of laser light are as follows.
- LASER Distance Sensors
- Laser Displacement Sensors
- Laser Projector
- LASER Photoelectric Sensors
- LASER Edge Detection Sensors
- Laser Light Curtains
- Laser Positioning sensor
1. LASER Distance Sensors
As the name suggests, LASER distance sensors are used to measure distance. LASER distance sensors can be used for larger distances also. LASER distance sensor work on the principle of Time of Flight (ToF). The time between the LASER sent and received is recorded by the internal circuit. The speed of the LASER is already known. So, by a simple formula of speed = distance/time, we can know the distance.
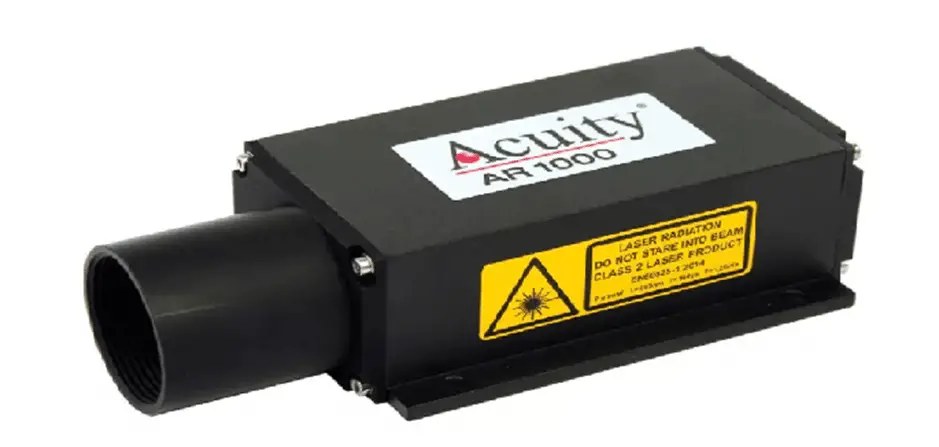
There are three types of Laser displacement sensors. They are-
1a. Reflective Laser Sensor
The Reflective laser sensor is called a transmitter/receiver. It has an emitter that emits laser light, and a receiver that receives the light. The emitter emits a light beam. The light beam reflects from the target object and the receiver detects the reflected light and detects the target.
1b. Through Beam Laser Sensors
In Through Beam laser sensor optical axis generate a signal beam. The sensor detects the target objects by detecting whether the emitted laser beam is interrupted by the target.
1c. Retro-reflective Laser Sensors
The sensor creates a signal beam between the reflector and the sensor. The sensors receive the reflected light from the surface of the object and thus the object can be detected.
2. Laser Displacement Sensors
Displacement sensors are generally used to detect objects. Displacement sensors are not aimed to measure distance. In Displacement sensors, the sensor would emit LASER light. A passing object would reflect the beam when the object crosses the displacement sensors. This reflected beam would make the sensor judge the received reflection as a detection of the object.
Displacement sensors are more versatile. Displacement sensors can be used in thickness measurement also. Displacement sensors can be used in profile measurements and position measurements.
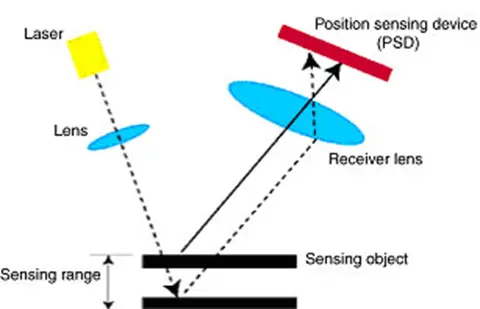
3. Laser Projector
LASER projectors are LASERs that can project LASER light on the desired surface. The projected light can determine margins, dimensions, or position in an application. LASER projectors are used in industries like textile or electronics. LASER projectors are also used for presentations in offices, classrooms, hotels, museums, showrooms, and attractions to simulation applications.
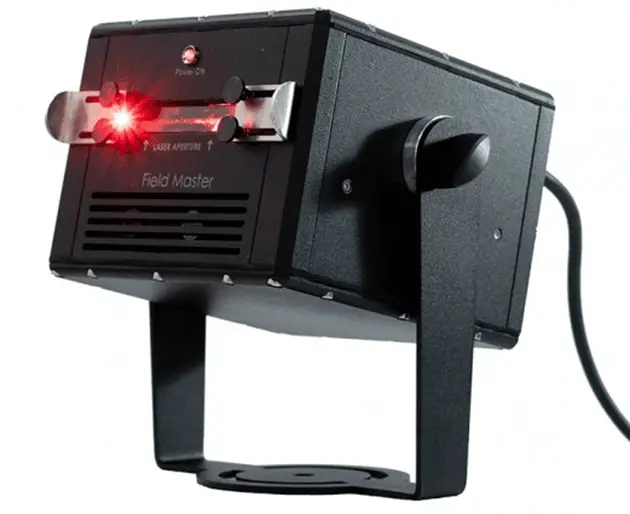
4. LASER Photoelectric Sensors
LASER photoelectric sensors are used where the processes are carried out at high speed. For example, counting/detecting the product. Because of their capacity to detect objects at high speeds, they are also known as trigger sensors.
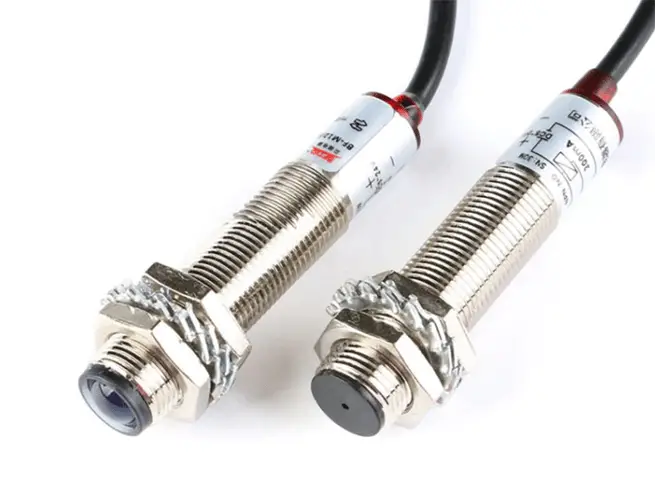
5. LASER Edge Detection Sensors
LASER edge detection sensors are used where inline detection and counting one side of the product are needed. The LASER edge detection sensors are mounted in the production line. The LASER edge detection sensors are used where thin sheets/plates must be detected on the basis of thickness so as to limit accumulations and production errors.
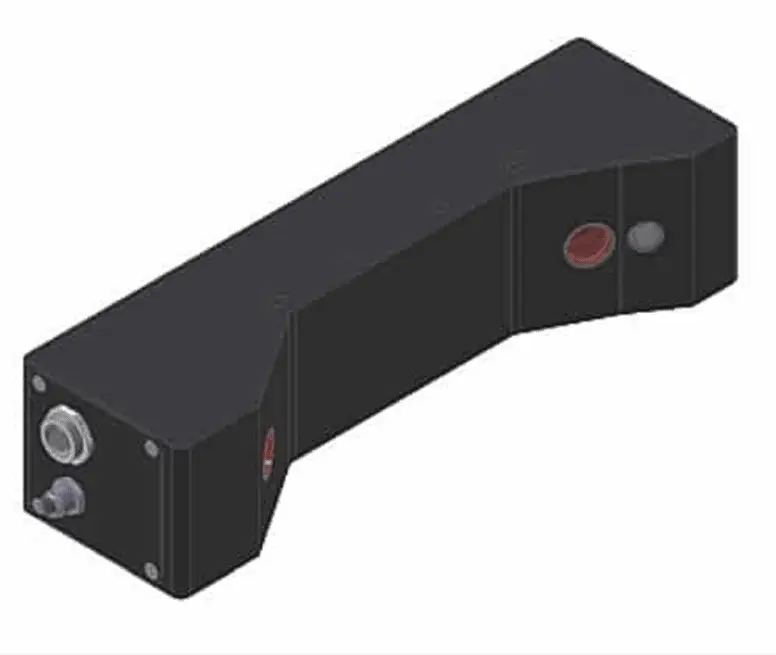
6. Laser Light Curtains
These types of laser sensors consist of a transmitter and a receiver. There is a barrier of parallel laser beams emitted between the transmitter and receiver. Objects passing through the barrier are detected and also measured.
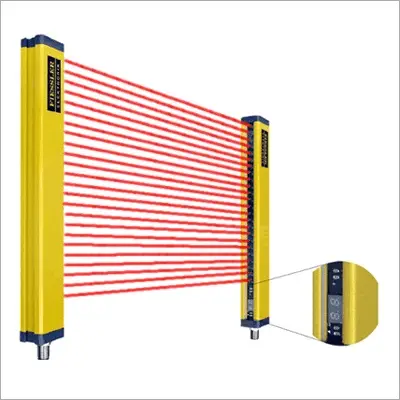
7. Laser Positioning sensor
These lasers are used for the positioning of the products. The positioning laser transmits a projection and it does not receive the reflection.
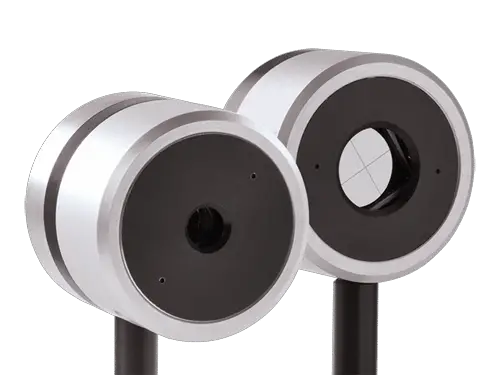
Advantages of LASER sensors
- The LASER sensor’s measurement is very accurate.
- LASER sensors have a high direction of the beam and a small divergence angle of light.
- The level of brightness is high for LASER sensors.
- LASER sensors can range up to several kilometers.
- The frequency width for LASER sensors is smaller than ordinary light.
- Contactless measurement is done by LASER sensors, so does not interrupt the process.
- Digital, as well as analog outputs, are available for LASER sensors.
- LASER sensors can be used in all industrial environments.
- Detects a wide range of materials.
- It is easy to install Laser sensors.
- Resistant to interference and environmental noise.
Disadvantages of LASER sensors
- LASER sensors are more expensive than analog measuring devices.
- LASER sensors are very delicate because very precise calibration needs to be maintained.
- In some processes, a very high level of precision is not needed. Hence LASER sensors are not suitable there.
- LASER sensors can damage eyesight.
Applications of LASER sensors
- Location of object
- Quality control
- Aligning the railway track
- Measuring wire diameter
- Welding head position
- Measure brake rotor thickness
- Vehicle counting
- Limit recognition of the width and height of the vehicle
- Measuring the distance between two sheets
- Power tool control
- Checking wood thickness
- Deviation control in the process
- Quality Control
- check the wood thickness