In this article, we will learn how an IO-Link works. The IO-Link is a powerful communication protocol that is an increasingly deployed point-to-point serial communication protocol.
IO link is used to communicate with sensors and/or actuators. IO link extends the globally recognized PLC standard IEC 61131. IO link also allows three types of data to be exchanged – process data, service data, and events. Most of the sensor manufacturers and industrial manufacturing companies have joined the international IO-Link Consortium to promote the IO-Link communication protocol. IO-Link has many advantages over standard IOs.
Four Generations of Automation
Before getting deep into the topic, let us look at the four generations of automation.
- First Revolution: The first revolution of automation dealt with the transition of manual labor to systems working by steam-powered or water-powered engines and other machine tools.
- Second Revolution: The second revolution of automation made the use of steel and electricity in industries. The efficiency increased because of electrification. The systems also became more reliable. The production of assembly lines also started during the second revolution of automation.
- Third Revolution: The third revolution of automation made use of computers, PLCs, robotics, digital automation, and networks. This made increasing and controlling production easier and much more efficient.
- Fourth Revolution: The fourth revolution of automation makes use of IoT (Internet of Things), cyber security, real-time data access, large and smaller network connectivity, etc.
In the fourth revolution, there are many technologies that help in smart coding and manufacturing. One of them is the IO link.
What is IO-Link?
Let us now understand the IO-link in detail.
The IO link is an interface solution that communicates with a wide variety of data concerning the sensor and actuators. IO link communicates in a fast, easy, and data-driven way. IO link has a point-to-point industrial networking protocol that provides a variety of data from sensors and actuators.
Unlike normal sensors, the sensors and actuators with the IO link give other data along with just the signals which either give simple digital output or analog output. The IO link protocol also provides information like the basic setup of the device, longevity prediction, effective operation or maintenance, diagnosis, and status information.
Similar to the HART protocol, in the IO link protocol also a device can be configured directly from PLC or a controller and enable fast replacement settings. By this the efficiency of automation would increase, downtime will be reduced, and help in decreasing maintenance activities. No extra cables are needed for this data communication. Like in the HART protocol, the 3 wire cables are used in sensors.
What does IO-Link offer you?
- It is an IEC 61131-9 global standard digital communication protocol
- IO- link easily sets up point-to-point communication.
- IO-link can be connected to control systems with Ethernet-based Fieldbus systems, such as EtherNet/IP, PROFINET, and AS-i.
Types of Data Communicated in IO-Link
As mentioned earlier, it can allow three types of data to be exchanged. They are:
1. Process Data
Process data have input or output data. It shows the latest state of the sensor or communicates the desired state of the actuator. Communication takes place during each communication cycle. It usually takes around 2 milliseconds. It can contain data between 1 bit and 32 bytes of information. Process data has the actual information from the sensor or actuator (for example, raw counts or current value).
2. Service Data
The Service Data Protocol Units (SPDUs) will allow the user to retrieve detailed information about the device. It can communicate almost everything ranging from basic device information (for example, version, type, serial number, etc) to advanced information (for example, configuration, detailed diagnosis, or status). It can communicate using up to sixteen thousand blocks. Out of these, some parts are standard to the protocol, but the device manufacturers can make any necessary information or configuration available.
3. Event Data
Events that occur very rarely are included in the process data. But these must be reported without waiting for SPDU((service protocol data unit) to be queried and can be delivered using IO-link’s event facility. This would allow standard or vendor-specific information about some alarms or informational messages to be delivered when they are encountered.
Why use the IO link?
The IO link sensors can be installed almost everywhere, in place of analog or digital sensors. They would provide significantly more information, configurability, and control. IO link has many advantages from installation to operation and maintenance. The followings are the good points of the IO link.
Installation and Commissioning
In the case of a new system or in the case of retrofitting an existing system, the IO link will make the installation and commissioning of a system less demanding as compared to traditional machine installation. Standard cables and connectors are used to reduce wiring complexity by eliminating the requirement for custom cables, connectors, or terminators.
Operating efficiency
The ability of IO links to identify devices and provide access to the parameters of devices gives much more control than traditional sensors.
Maintenance
The IO link events pinpoint issues and potential errors before they occur. For example, a sensor will automatically send a signal to PLC if the batteries are running low. So, maintenance can be done which will avoid machine downtime.
How does IO-Link Work?
IO link technology works on the master-slave protocol. The IO link master device connects various slave devices to the controller, say PLC by a standard 3-wire connection. The pin assignment of the IO-Link is given below.
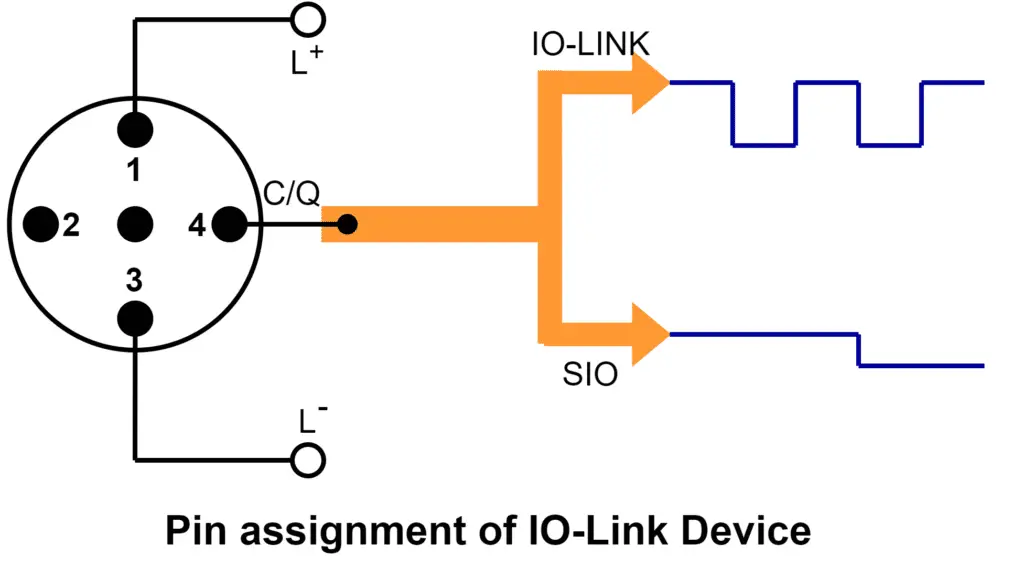
According to IEC 60974-5-2, the pin assignment is specified as follows:
• Pin 1: 24 V
• Pin 3: 0 V
• Pin 4: Switching and communication line(C/Q)
The master usually has 8 ports and can process digital as well as analog signals. The connection is done using the M5, M8, and M12 ports. The communication is fast, usually between 400 microseconds to 2 milliseconds. Transfer of data is bidirectional. There is a serial point-to-point connectivity for signal and power. The architecture of IO- Link communication is given below.
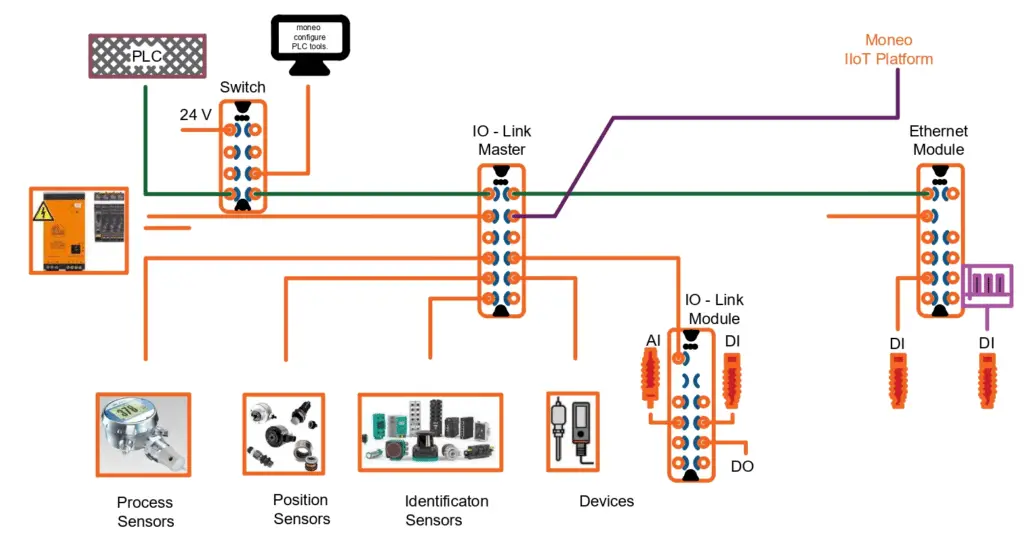
The maximum distance for connection of a device is 20 meters.
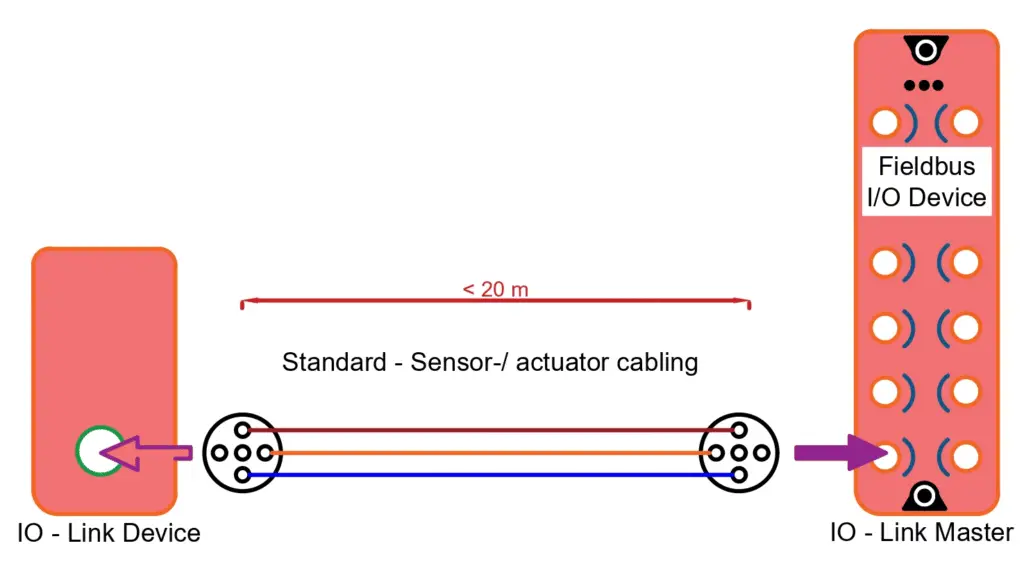
The communication protocols that the master uses for communication with PLC are Modbus, Profinet, Ethernet IP, etc.
What are IO-Link Operating Modes?
The followings are the operating modes of IO-Link.
1. IO-Link Operating Mode
In the IO-Link operating mode, the port is used for IO-Link communication.
2. DI Operating Mode
The port acts in the same way as a digital input device in the DI mode.
3. DQ Operating Mode
In this mode, the port acts in the same way as a digital output device.
4. Deactivated Operating Mode
The fourth operating mode of IO-Link is the Deactivated mode. In the deactivated operating mode, the port is unused, not assigned to any other modes, and it is reserved.
Advantages of IO-Link
- Uses standard, unshielded M8 or M12 cables of up to 20 metres
- Possible to send and receive significant data.
- No conversion loss- It receives the digitally measured values and process data directly from the sensor without any conversion losses.
- Programming & monitoring of data through software
- logging of event data and diagnostic data
- Binary( 0&1) use of sensors in SIO mode
- Use of additional digital functions in COM mode